Miniature accelerometers and gyroscopes are essential for applications such as vehicle dynamics, navigation and logistics. In this blog post, we present what characterises them and where they can be used.
Linear acceleration in one or more axes or acceleration in several directions of movement in the smallest of installation spaces: there is no way around miniature sensors in many applications. Our powerful MEMS sensors are designed for use on printed circuit boards. They are mounted on top or on the side. Depending on the application, an accelerometer, a rotation rate sensor (gyroscope) or the particularly versatile inertial measurement unit (IMU) for recording six degrees of freedom may be the right choice. All miniature accelerometers in our portfolio are characterised by their high precision, long-term stability and a wide measuring and operating temperature range. Shock and vibration resistance and low power consumption are also strong arguments in favour of their use in demanding applications. A balanced, vibrating silicon MEMS ring is used as the sensor element in our gyroscopes. This design ensures very low time and temperature-dependent bias drift and high repeat accuracy.
Three measuring principles depending on requirements
There are three main measuring principles for miniature sensors (both accelerometers and gyroscopes): piezoelectric, capacitive or piezoresistive. With all of them, the measured movement triggers an electrical signal that is accessible to all types of further processing.
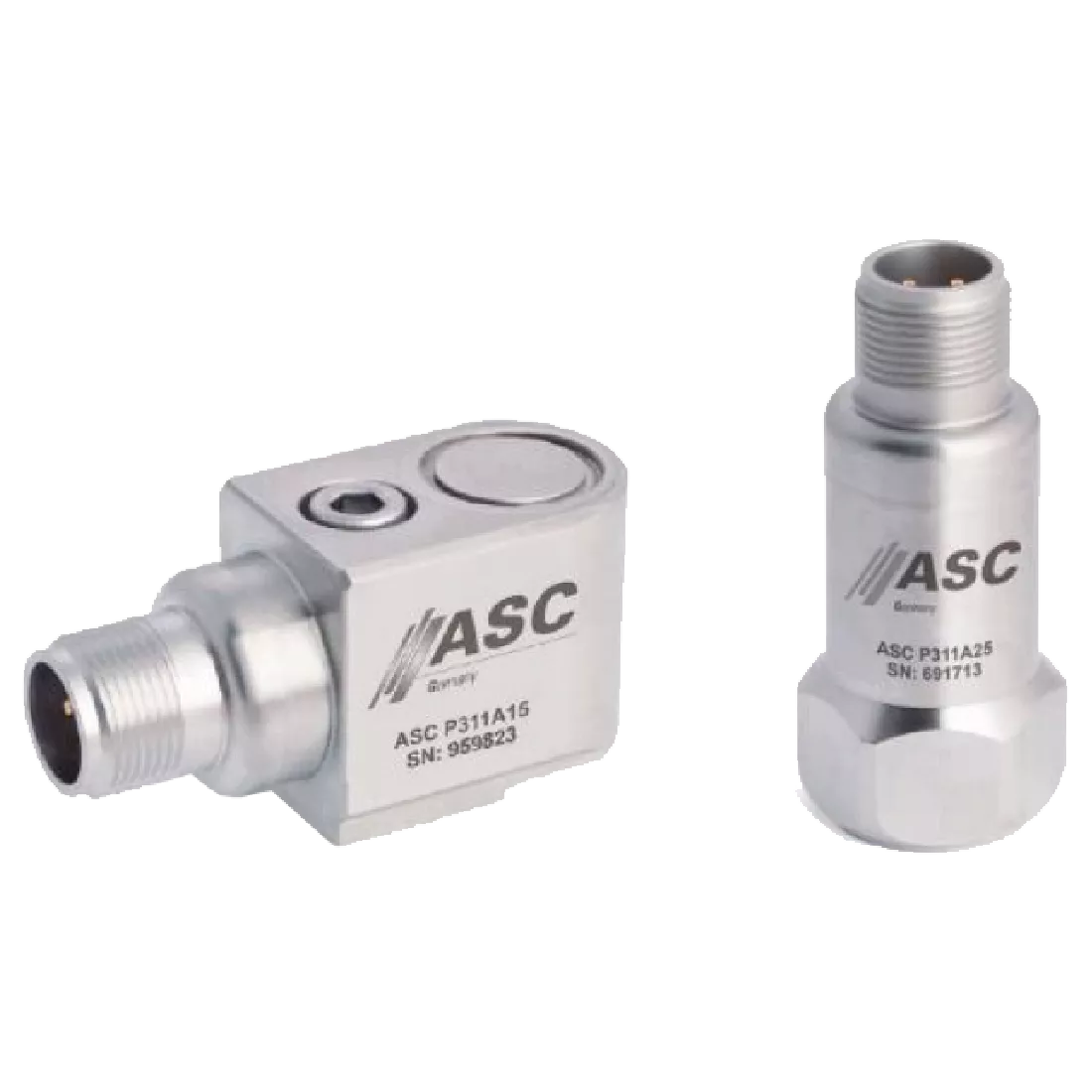
Piezoelectric sensors
The piezoelectric sensor utilises the ability of certain materials to generate electrical voltage when subjected to mechanical stress. Capacitive sensors measure the change in capacitance between two electrodes, which is triggered by a change in the environment. Piezoresistive sensors measure the resistance of a material that changes under mechanical stress.
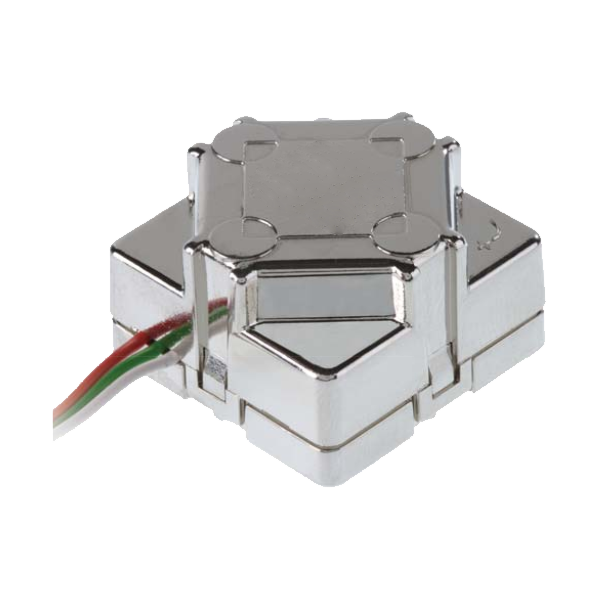
Gyroscopes
Gyroscopes measure rotational movements and angular or rotational speeds. Unlike other rotation meters, our gyroscopes do not require a fixed reference point. They measure from +/- 25°/sec to +/- 900°/sec. This large measuring range makes them suitable for a wide variety of systems, from robots to drones.
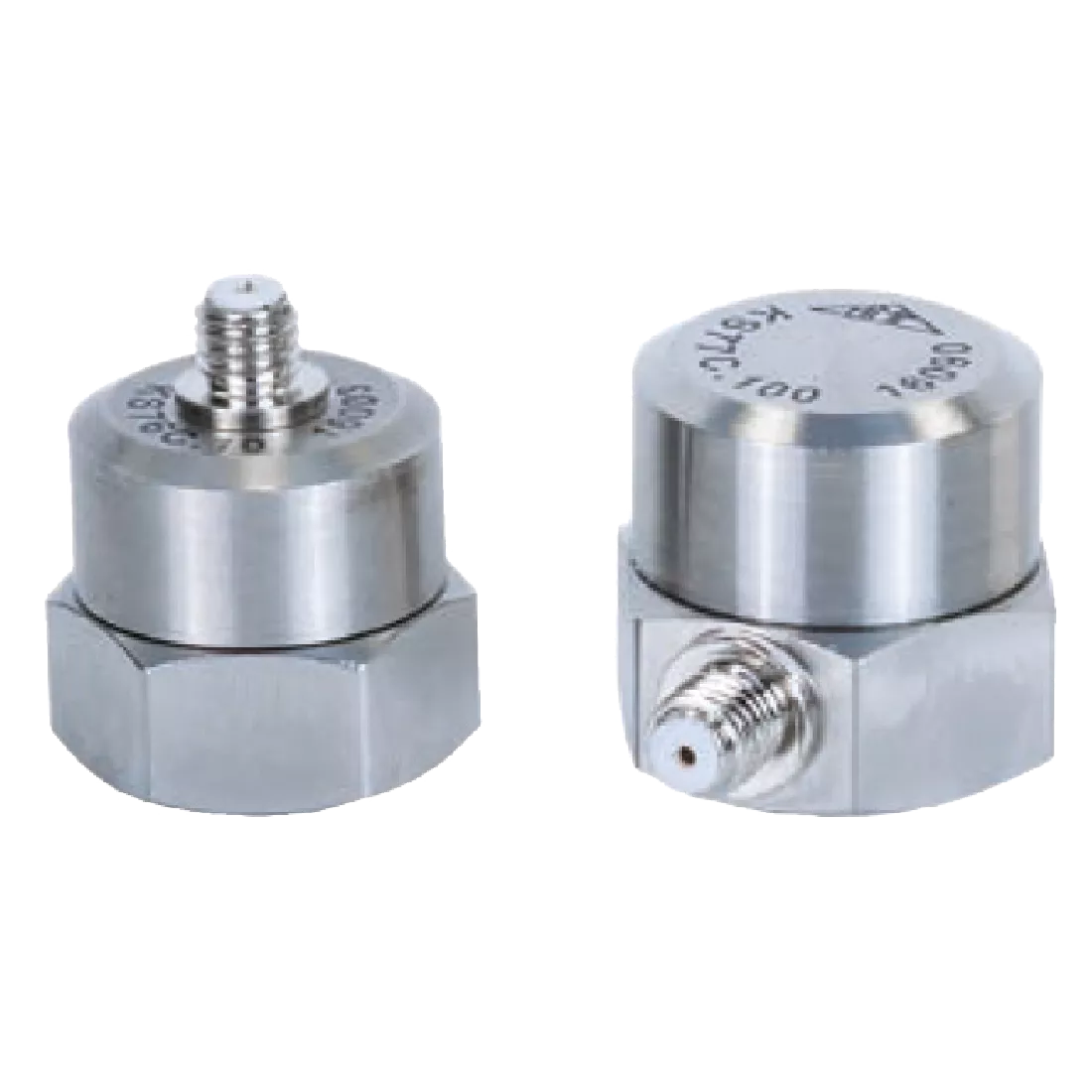
Linear acceleration sensors
The linear acceleration sensors cover the measuring range of ± 0.25 g and ± 70,000 g in one or more axes. In addition to speed measurement, they are also suitable for vibrations, displacements or tilting movements.
Areas of application for miniature accelerometers in the automotive industry
The main areas of application for miniature accelerometers in the automotive industry are steering and navigation in demanding environments and increasingly also for autonomous vehicles. Another field of application is stabilisation, for example in high-precision industrial environments. Precise positioning of transmitters and receivers is essential for modern communication systems. Particularly important in this context is insensitivity to shocks and vibrations in harsh environments and even in space. Whether in industry or for scientific purposes, the recording of movement data in several axes forms the basis for many applications.
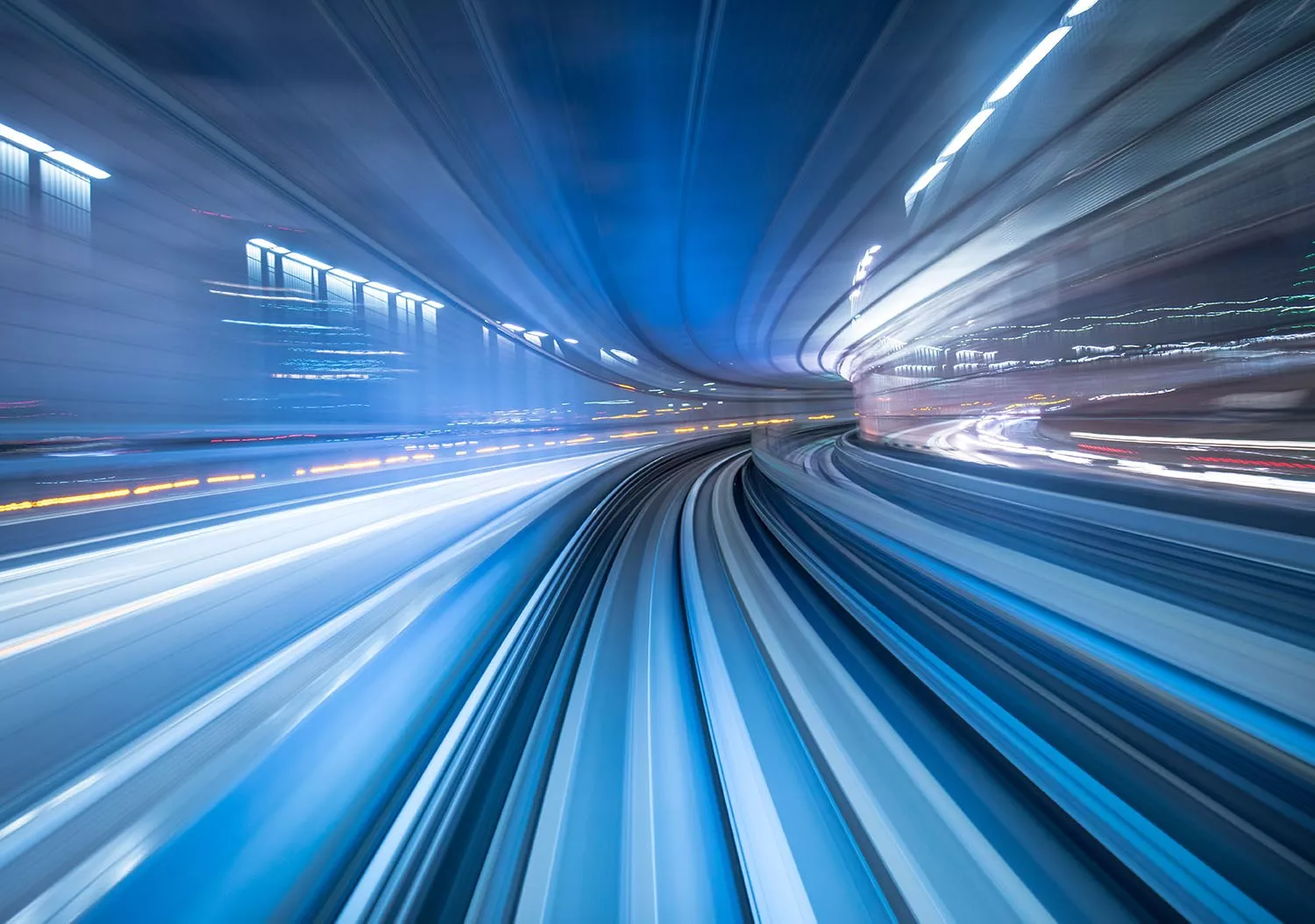
So that the sat nav still works in tunnels
Acceleration sensors and gyroscopes ensure that in-car navigation systems are updated even if the GPS signal fails, for example when driving through tunnels. The acceleration sensor records changes in speed, while the gyroscope records steering movements. In this way, the sensors record all the important information for the navigation system.
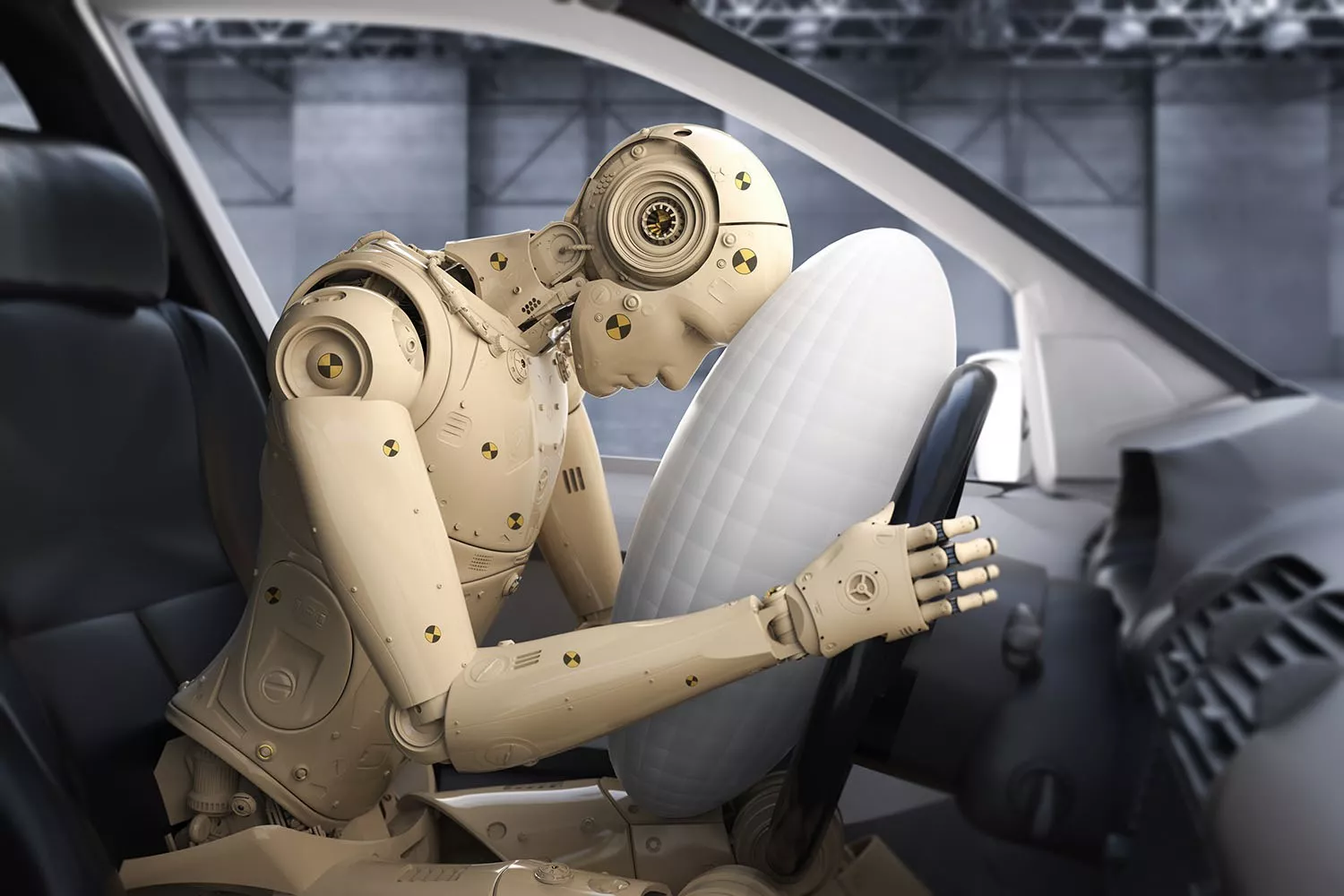
Driving dynamics
The life-saving airbag needs a signal to trigger it. For this purpose, an acceleration value is defined that corresponds to a collision and subsequently activates the deployment of the airbag. The acceleration sensor measures continuously. The vibration resistance has a positive effect because the pure acceleration signal is measured and is not disturbed by other movements of the vehicle.
Skidding and other unwanted movements are detected by gyroscopes. They are there to activate the stability system when the set values are exceeded so that the vehicle returns to the desired smooth road holding. In concrete terms, this means that the information from the sensor must flow to the various control units in fractions of a millisecond, for example: ‘G-forces at level X are acting on the front axle - block the rear right-hand tyre immediately.’ The stabilisation and other driver assistance systems can only work properly if this flow of information functions smoothly thanks to the sensor system.
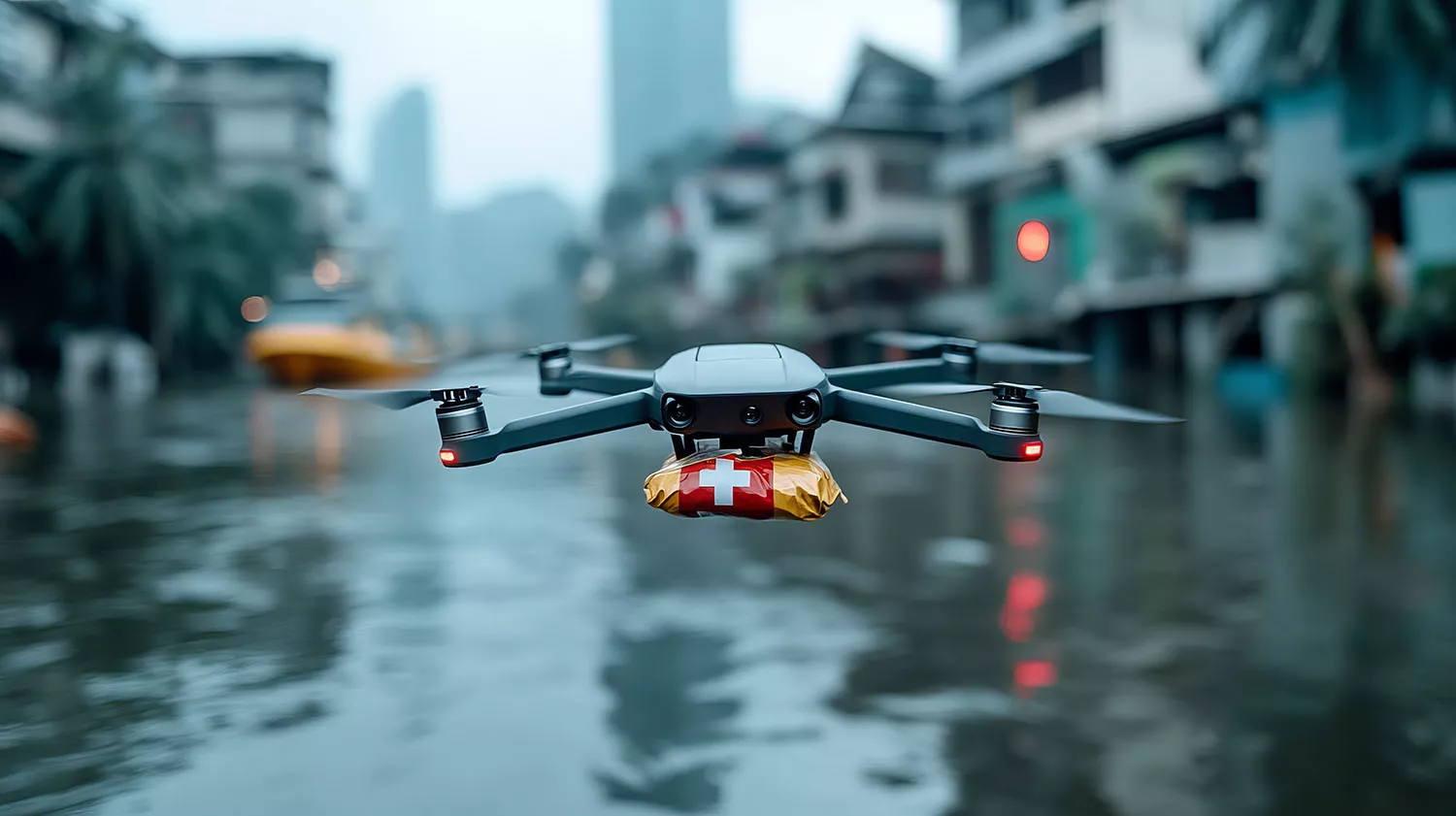
Parcels by drone
Everything that flies has to be mindful of its weight. This is why miniature sensors with a low mass are the right choice for capturing movement information in civilian drones. One possible application is the delivery of medicines or small parcels. Delivery from the air is also intended to relieve traffic congestion in cities and combat staff shortages. In multi-storey buildings, there could even be no need to go to the front door if the delivery drone ‘knocks on the window’.
Drones are also being used in agriculture: In so-called smart farming, individual plants can be targeted and supplied with specific products, for example in viticulture.
In addition to their technical functionality, all mobile applications must be optimised in terms of their power consumption so that the batteries they carry can remain as light as possible. At the same time, even the most compact format must be highly resistant to shock and vibration in order to achieve reliable results. The selection of a suitable transducer for the respective application is always a trade-off between the required power and the associated consumption or the weight of the components. Our solutions are customised to the respective application.
Inertial sensors (IMUs) with Six Degrees of Freedom
The IMU combination sensors detect all movements. IMUs combine a three-axis accelerometer with a three-axis angular rate sensor. This is referred to as the detection of six degrees of freedom. These all-rounders are used in production robots, for example, where all arm movements and the respective acceleration are measured. Not all components may be exposed to high acceleration. The IMU also provides information on the position, i.e. where the robot arm and hand are at any point in the production process.
OEM version or complete system
We generally offer our miniature transducers in two versions: as an OEM version or with its own housing. The version in the housing is ready for immediate use with its own connector. In the OEM version, our customers can integrate the circuit board with the soldered-on sensors into their own system - either with solder points or pins. The sensors can be mounted flat (plain) or upright (orthogonal) on the board. We can realise individual OEM designs within a short period of eight to twelve weeks and also supply them in large quantities for series application by our customers.
Even better with developer tools
We also support our customers in the assessment and further integration of acceleration sensors and gyroscopes. With special development boards, which we can provide, tests and analyses can be carried out for pure evaluation. This makes the customised development of OEM solutions even more targeted and efficient.