Eddy current sensors, also known as ‘eddy current’ sensors, belong to the category of displacement transducers and are based on an inductive measuring principle. They work without contact and are therefore very low-wear and durable.
Eddy current sensors, also known as ‘eddy current’ sensors, are displacement transducers and are based on an inductive measuring principle. They work without contact and are therefore very low-wear and durable. An inductive eddy current sensor generates a high-frequency electromagnetic field around a coil. Depending on the distance, this induces an eddy current in the target material to be detected, which in turn generates a magnetic field in the opposite direction to the original magnetic field - prerequisites: The target material must be electrically conductive and the target area must be of a certain size. The sensor then detects a change in resistance, which can be used to determine the distance, position, thickness, alignment, inclination or other properties of the target material. The concentricity of rotating system parts can also be checked in this way; in this case, very small changes in distance in the range of 0.5 to 60 mm are involved.
Non-conductive materials between the eddy current sensor and the target object are not detected, meaning that dirt, dust, adhesions or other materials such as plastic do not affect the measurement. This insensitivity predestines eddy current sensors for use in harsh environmental conditions. However, this does not always include fluctuating temperature conditions, which can certainly have an influence on the measurement result. In addition, the distance to the target material must be at least 10 % of the sensor measuring range. Eddy current sensor measurements are also carried out in a vacuum or in liquids.
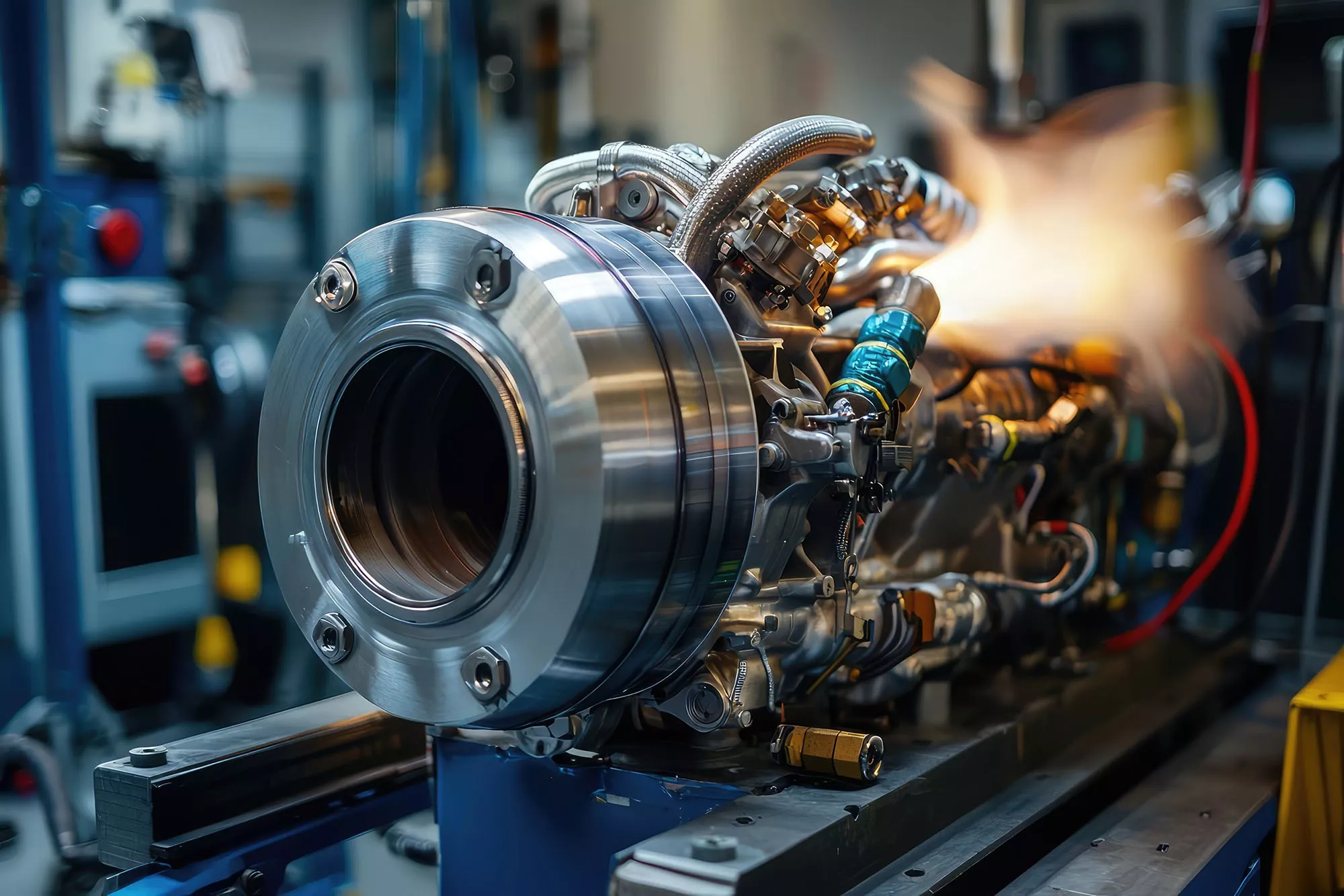
Possible applications
Many position sensors work primarily via contact between the sensor and the measured object. Eddy current sensors are a good choice for displacement measurement when such a contact measurement method is not possible, e.g. due to a dirty environment or when very small changes and limited installation space are required. They can also be easily integrated in unfavourable structural positions. Examples of applications include in the automotive and aerospace industries, for distance measurements of shafts or rotor shaft measurements, dimensioning, sorting and thread testing, but also in industrial production for extensive series testing.
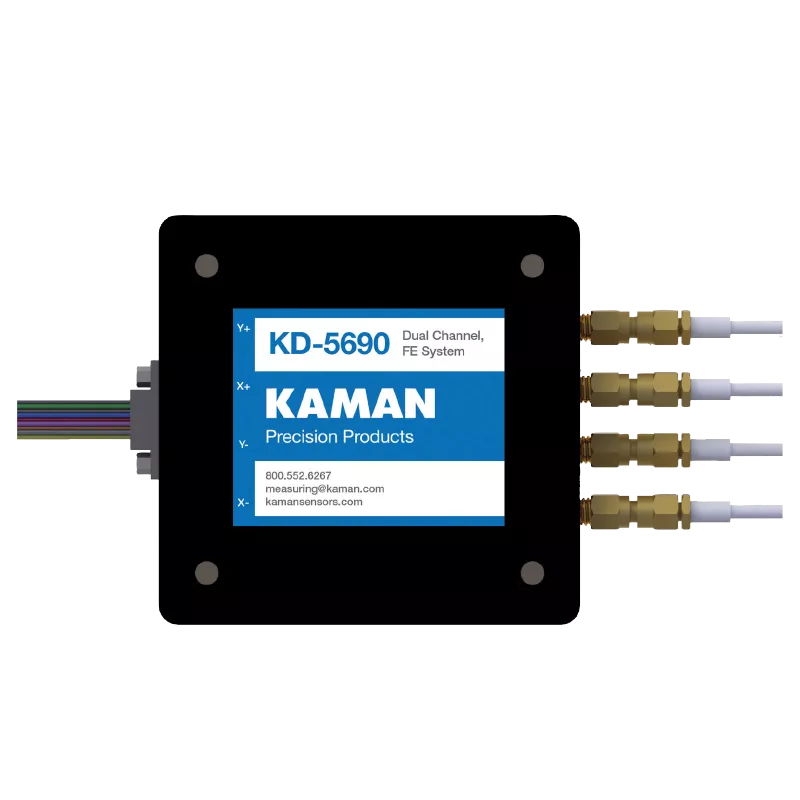
High resolution and frequency
A good eddy current sensor is characterised by a high resolution (our finest sensors have a resolution of 0.1 µm) and a higher frequency response. The latter means that the alternating field changes more quickly and thus reacts to smaller changes in distance. We use eddy current sensors from a premium manufacturer with over 40 years of experience in measurement technology. In addition to selecting the application-specific sensor, we also provide support with value-adding work, e.g. integrating the sensors and electronics into higher-quality assemblies such as housings, plus displays or amplifiers and application-specific calibration to provide plug & play-capable measuring chains.
-
Non-contact measurement:Low-wear and durable
-
Highly accurate measurements:Distance changes in the range from 0.5 to 60 mm
-
No detection of non-conductive materials:No impairment of the measurement due to contamination
-
Small and space-saving:Good integration in difficult structural conditions
Calibration
Calibration is very important for reliable measurements in such small measuring ranges with such high resolution. This includes both the initial calibration and recalibration if the sensor has already been in use for some time. For the initial calibration, the sensor must be set up for the target material. As a rule, customers send in the target material to ensure the best possible calibration (e.g. aligned to the respective magnetic permeability of the material, etc.). Althen can arrange this initial calibration and carries out recalibrations in-house.
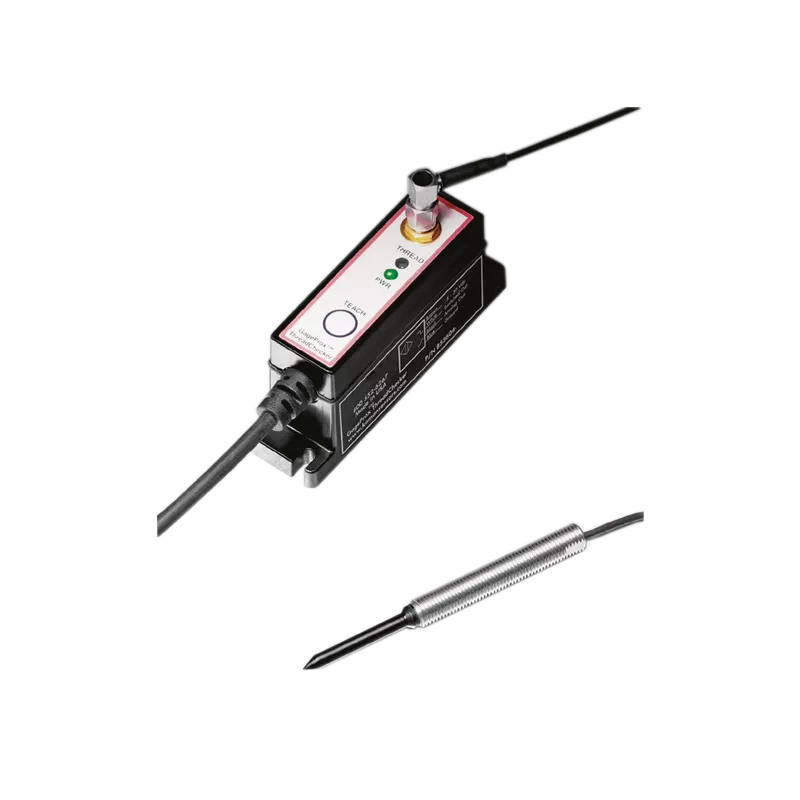
Special sensor: ThreadChecker
To illustrate the wide range of possible applications for eddy current sensors, we will look at an example application, the ThreadChecker, a special type of eddy current sensor. As the name suggests, it is used to check the presence and quality of threads. It uses an analogue output signal to indicate whether or not an accurate thread has been drilled in an automated process. In the mass production of parts that are to have a thread, for example for the automotive industry, the use of the ThreadChecker saves time and resources if parts can be checked during production in real time instead of at the end of the production process.
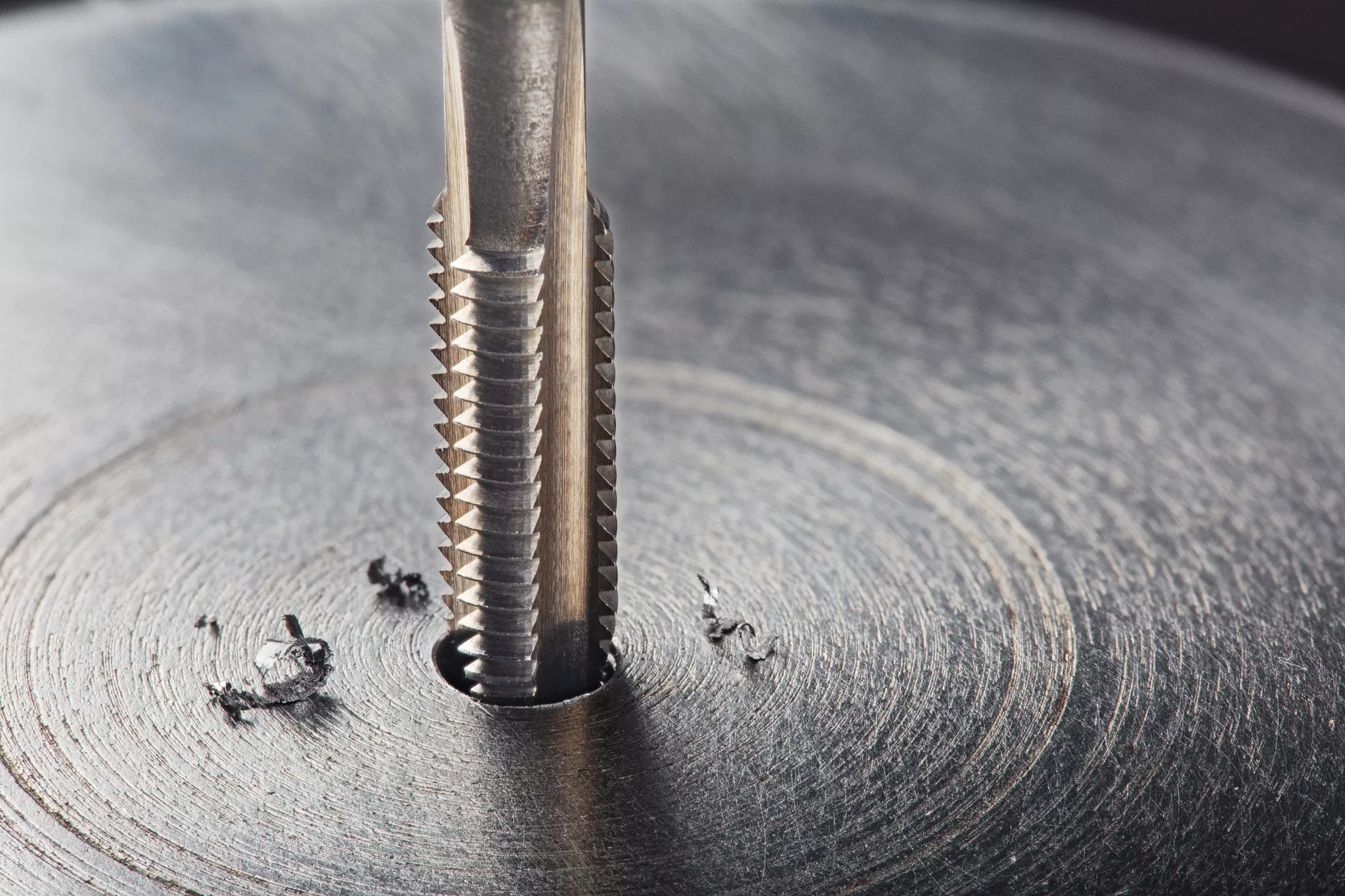
Distinguishing threads
To check a thread, the eddy current sensor is immersed in the thread. The device must first be taught in, i.e. the height, immersion depth and centring for the sensor must be defined. In the next step, the ThreadChecker is immersed in a defined manner and recognises whether the thread is OK (indicated by a red or green light). It is also possible to differentiate between different threads. When threads are immersed, various signals are emitted that move around a certain level. The level can be used to determine which thread is involved.
Alternatively, laser or capacitive sensors could also be used for thread testing. However, these require a clean test environment, meaning that the parts to be tested would first have to be cleaned of lubricants, chips and cutting fluids. In contrast, an eddy current sensor, which works precisely under dirty conditions, has the edge.