In the test & measurement sector for vehicle construction, a large number of components have to undergo thorough testing before they can actually be installed. These include leak and temperature tests, acceleration measurements and efficiency determination. The pedal force of the individual pedals of a vehicle is also tested: accelerator and brake pedals as well as the clutch. The sensors used here are specific force transducers, which can be used to determine whether the respective pedal is set to the correct pressure point. Measurement specialist Althen GmbH Mess- und Sensortechnik explains what characterises the special force transducers and what needs to be taken into account during the tests using the project examples of an automotive supplier and a vehicle manufacturer.
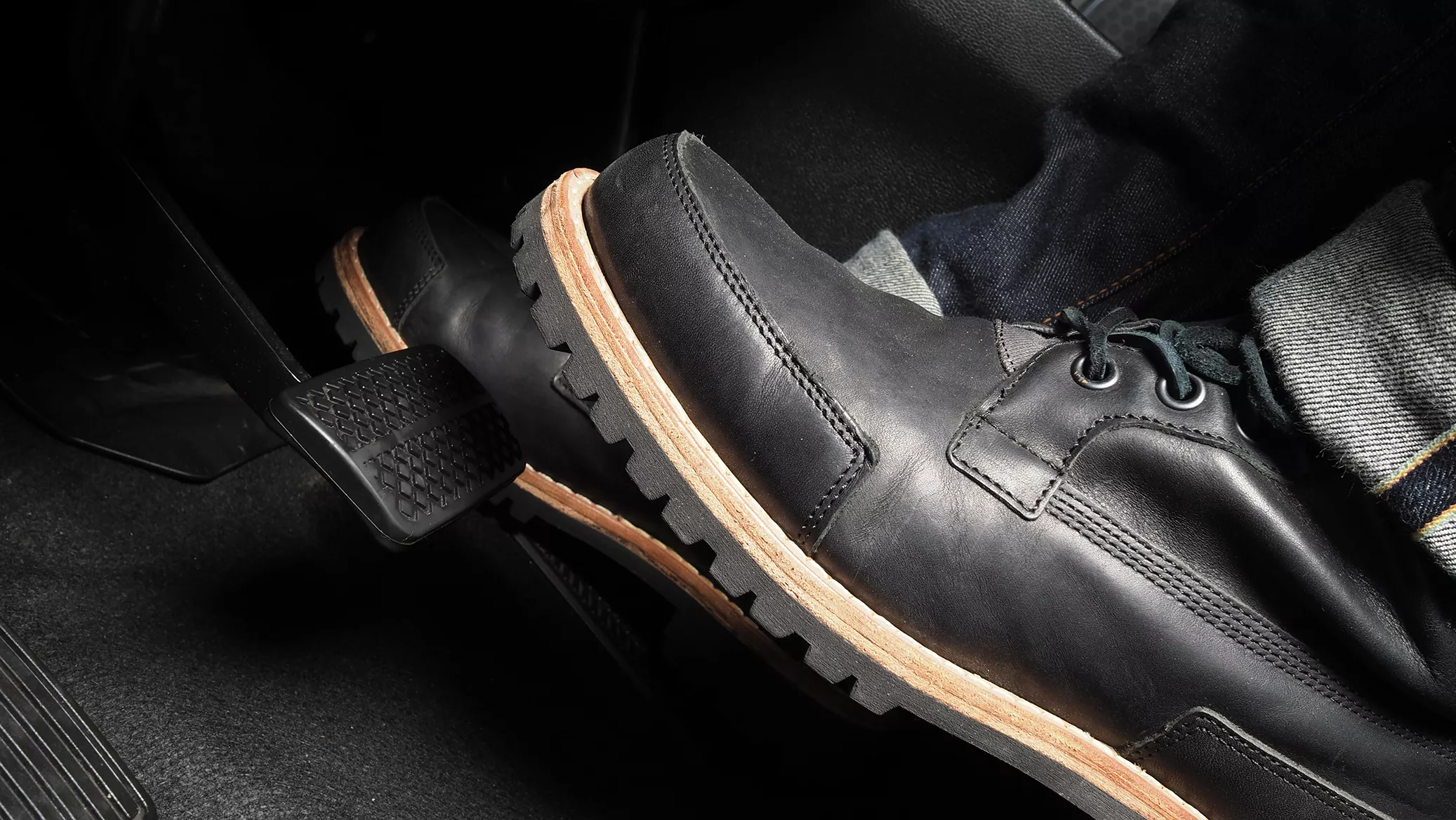
What initially seems trivial - how hard should a pedal be depressed - is, on closer inspection, an important ergonomic question for the vehicle user. Pedals should be comfortable to operate, i.e. the setting should not be too stiff, and not too much force should be required to operate them in order to be able to complete longer journeys without tiring the feet. On the other hand, a brake pedal, for example, must not be too smooth in order to avoid unintentional abrupt stops. It is clear here that the pedals require different pressure points: An accelerator pedal requires a different pedal force than the brake pedal and this also depends on the type of vehicle, for example a car or forklift truck. The extent to which the pedals should be set softer or harder is the subject of the respective tests.
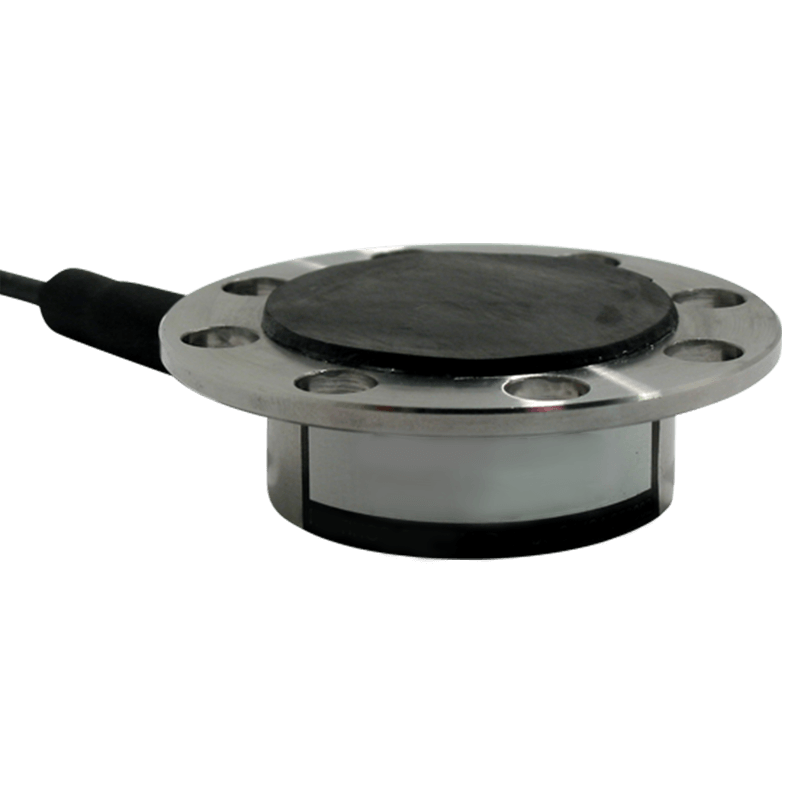
ALF304: Diaphragm and bending beam force transducer in one
To test the pedal force, force transducers are attached directly to the pedal. Measurement specialist Althen supplies one of its automotive customers with a hybrid of diaphragm force transducers and bending beam force transducers for this purpose. A pure diaphragm force transducer, which would be very suitable for test bench applications due to its compact size, is generally very sensitive to non-axial loads, which can occur when determining the pedal force. For this reason, the supplier uses a force transducer with a bending beam structure, in which the diaphragm is reinforced with a cross structure (ALF304 series transducer). This can compensate for possible angular forces much better than a pure diaphragm force transducer. This results in only very small measurement errors. Depending on the type of pedal and the expected compressive force, force transducers with a suitable measuring range are used - the ALF304 series has three different force transducers, which are designed for 2.5 kN, 1 kN and 250 N.
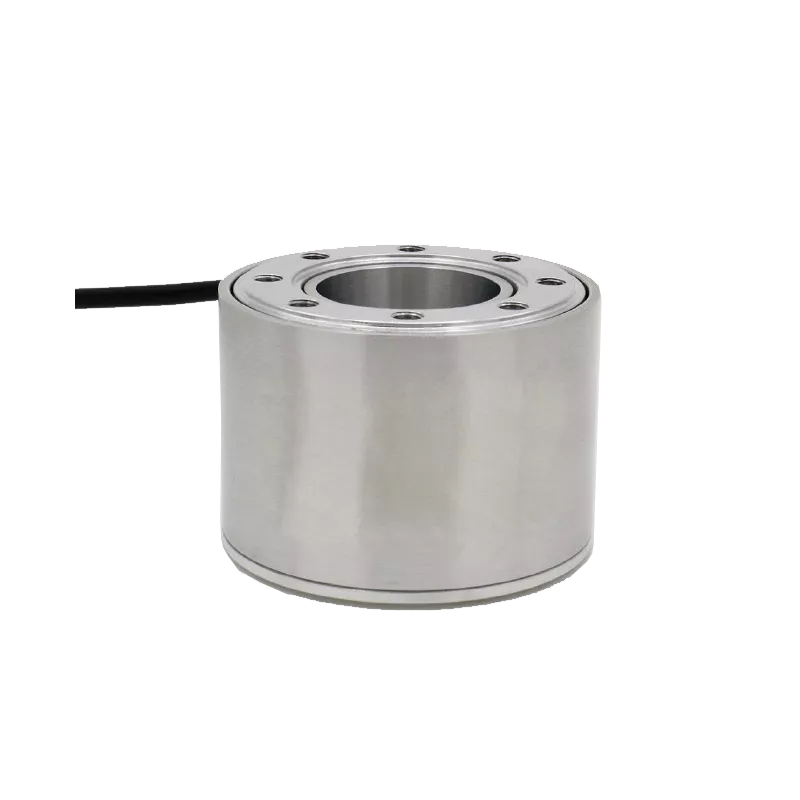
For more precision: ALF300 with bending beam structure
If even greater precision is required - as requested by an automotive manufacturer customer - Althen recommends the ALF300 force transducer, which has a very special structure: it is designed in a cylindrical ring shape and has a complex bending beam structure on the inside. This enables even better error compensation. If a force transducer is not loaded exactly in the centre and therefore one side is loaded more than the other, measurement angles can occur which the ALF300 compensates for, thus enabling even more precise measurement. Due to its design, however, the sensor is significantly larger than a standard pedal force transducer from the ALF304 series. For the customer, however, the size was acceptable in favour of the higher accuracy.
Compensation of non-axial loads
Pedal force checks can be carried out automatically, i.e. actuators act on a pedal. This variant is particularly repeatable, as the same point is always approached. However, suppliers and manufacturers also have testers check the optimum pressure point of the pedals ‘manually’. This comes closer to everyday use, where the optimum actuation point is also not always hit. In this case in particular, the ALF300 is better suited as a force transducer, as it can compensate for non-axial actuation. The measurement result is therefore significantly more accurate, which was a key requirement for the customer. Due to its complex structure, however, the ALF300 is more complex to manufacture and requires more material, meaning that the costs for the transducer are also higher than for a model from the 304 series.
Simple integration of the force transducers
To measure the pedal force, it is sufficient to attach one force sensor per pedal to the pedal using cable ties. Alternatively, they can also be screwed in place. Thanks to the flat, complex design, the pedal force transducers, such as the ALF304, have very little influence on the measurement result. They are also very robust and durable and can withstand several measuring cycles - it is not possible to give a generalised service life, as it depends very much on how the force transducer is stressed. It makes a difference whether it is loaded 100,000 times or just 10 times a day. Similarly, one customer may only use 70 per cent of the measuring range, while another application regularly generates more than 100 per cent load. Thanks to regular recalibration, however, the sensor has an extremely long service life. Althen carries out these recalibrations for customers on request.

Supply of evaluation electronics
Once the sensor has been determined and installed, evaluation electronics are required for recording. While some customers integrate the force transducers into their own control systems, Althen provides the automotive supplier with an entire measuring chain consisting of transducer and measuring amplifier. We particularly recommend purely analogue measuring amplifiers, which have a very good cut-off frequency with a high sampling rate. This allows certain peaks, i.e. very small, short-term changes, to be recorded very well. Each measuring amplifier must then be adjusted and calibrated by Althen to the respective transducer and the type of signals.
Customer-specific customisations
If an ALF force transducer from the standard portfolio does not quite meet the requirements of the application, Althen has many options for customising the transducers. This starts with modified measuring ranges, e.g. to increase the measuring range from 2.5 kN to 5 kN - the internal structure is reinforced and different material is used if necessary. Different temperature requirements can also be met. For example, if the sensor is to be used in a temperature chamber from -40 to 110 degrees Celsius, the force transducer is compensated for these temperature ranges. It is also possible to adapt the dimensions. The transducer itself is a very small box to which a larger ring with a plastic plate is attached. This ring can be enlarged, for example, so that the sensor fits better on a pedal, or the customer requires through-holes on the ring at certain intervals. Other internal threads can also be attached to the underside or different cable lengths made possible. For example, the automotive customer required the force transducer entirely without a plastic plate and with specially defined measuring ranges, which Althen calibrated accordingly.