Tilt measurement is a fundamental requirement across various engineering disciplines, from industrial automation and civil engineering to aerospace and defense. Inclinometers, also known as tilt sensors, angle sensors, or level sensors, are essential in capturing angular displacement relative to gravity, ensuring high-precision positioning and stability. Two primary inclinometer technologies—MEMS (Micro-Electro-Mechanical Systems) and Servo inclinometers—offer distinct advantages and limitations. Understanding their operational principles and performance characteristics is key to selecting the optimal sensor for your application.
Engineering fundamentals of inclinometers
Inclinometers measure angular deviation and inclination across multiple industries, with applications including:
- Structural health monitoring – evaluating tilt and deformation in bridges, tunnels, and high-rise buildings with geotechnical tilt monitoring sensors.
- Aerospace & defense – ensuring precise orientation and stabilization of aircraft, satellites, and military vehicles using high-resolution tilt meters.
- Industrial automation & robotics – enabling real-time feedback for automated positioning and motion control with machine-leveling sensors.
- Medical & biomechanical systems – Facilitating motion tracking in rehabilitation equipment and wearable devices with angular position sensors.
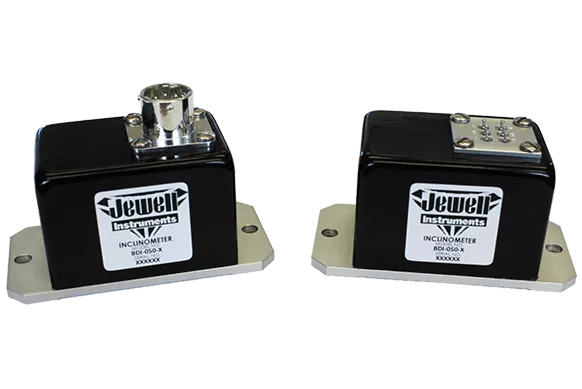
Technical overview: MEMS and Servo inclinometers
MEMS inclinometers: microfabricated precision
MEMS-based inclinometers leverage micro-machined mechanical elements embedded within silicon substrates. These sensors operate by detecting capacitance variations corresponding to tilt-induced displacement.
-
Compact, lightweight designIdeal for space-constrained and mobile applications.
-
Cost-effective manufacturingEnables large-scale deployment at reduced expense.
-
High shock and vibration resistanceWell-suited for dynamic and rugged environments.
-
Low power consumptionOptimal for battery-powered and energy-efficient systems.
Performance limitations MEMS inclinometers
- Lower intrinsic accuracy – Typically within 0.01° to 0.1°.
- Sensitivity to thermal drift – Requires periodic recalibration in precision applications.
- Decreased stability in low-frequency environments – Can introduce noise and non-linearity under minimal motion conditions.
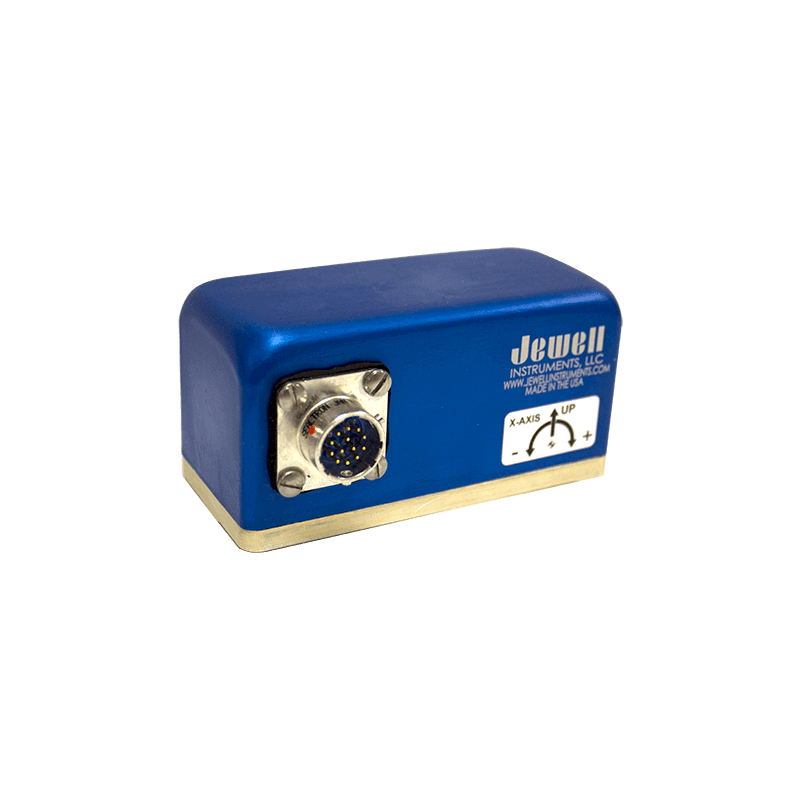
Servo inclinometers: electromechanical feedback for high accuracy
Servo inclinometers employ an electromechanical feedback loop with a dynamically stabilized pendulum system, ensuring high-precision angle measurement with minimal drift.
-
Superior accuracy and resolutionAchieves precision levels as fine as 0.001°.
-
Minimal long-term driftEnsures reliability in extended operational deployments.
-
High responsiveness and low latencySuitable for high-speed control systems.
-
Low-frequency performanceIdeal for applications demanding absolute stability.
Performance limitations Servo inclinometers
- Larger form factor and increased weight – Not optimal for miniaturized applications.
- Higher cost per unit – Premium technology with added complexity.
- Sensitivity to mechanical shock – Requires careful mounting and isolation in high-impact environments.
Comparative engineering analysis
When selecting an inclinometer, engineers must consider trade-offs in accuracy, stability, cost, and environmental resilience. MEMS inclinometers are highly suitable for applications where cost efficiency, shock resistance, and compact size are the primary concerns, such as industrial automation and automotive systems. However, they may experience drift over time and are less effective in ultra-low-frequency applications.
Servo inclinometers, in contrast, offer unparalleled accuracy, stability, and long-term reliability, making them the preferred choice for high-precision applications in aerospace, geotechnical monitoring, and defense systems. While their higher cost and sensitivity to shock may limit their deployment in rugged environments, their superior performance justifies the investment in scenarios where precise tilt measurement is critical.
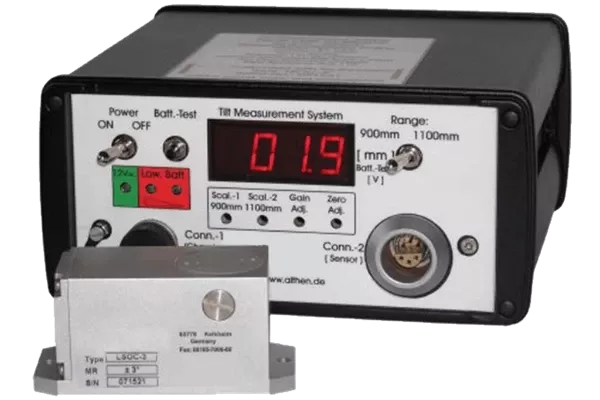
Engineering decision: selecting the optimal inclinometer
The appropriate choice between MEMS and Servo inclinometers hinges on specific performance requirements and environmental conditions:
- MEMS inclinometers (also referred to as G-force sensors or slope measurement devices) are preferable for cost-sensitive, high-durability applications requiring compact form factors, such as industrial automation, automotive systems, and consumer electronics.
- Servo inclinometers, often used in dual-axis inclinometer applications, are the optimal solution for applications where precision, stability, and low drift are paramount, including aerospace navigation, defense systems, and structural health monitoring.
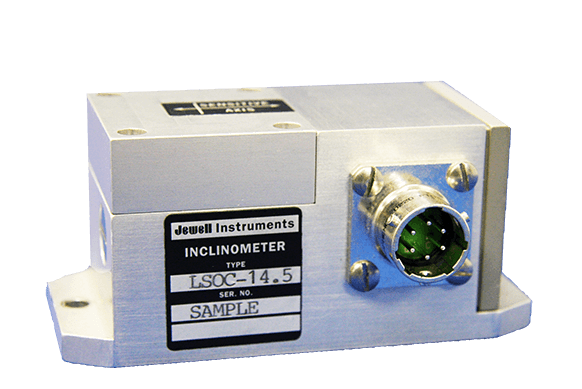
Tilt and inclinometers
Static or mobile measurement of inclination. Find out more about: Geotechnical inclinometers, tilt angle measurement systems,, and submersible tiltmeters.
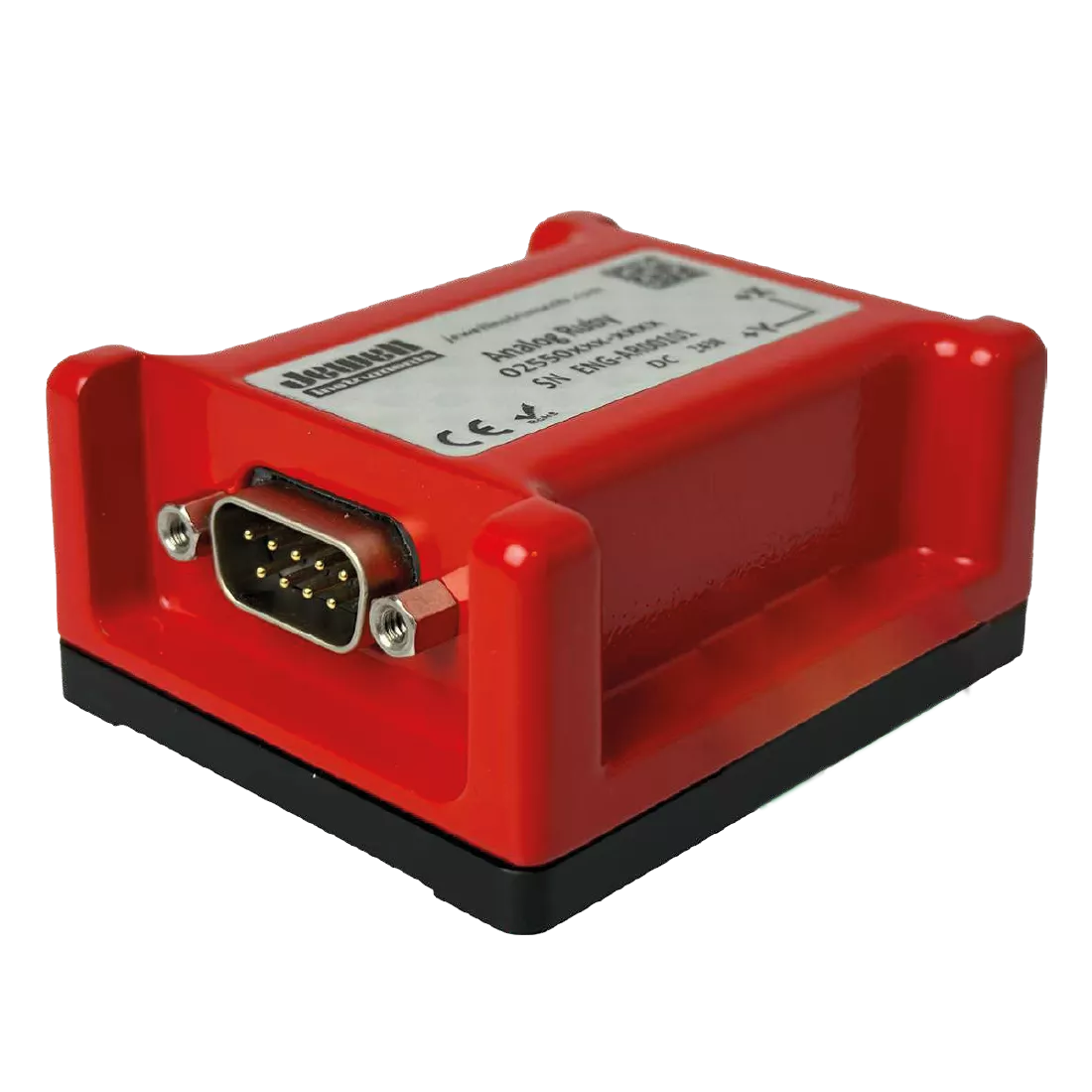
MEMS inclinometers
Each MEMS inclinometer is capable of measuring positive and negative inclination (angle) from +/-1° to +/-90° in one and two-axis configurations.
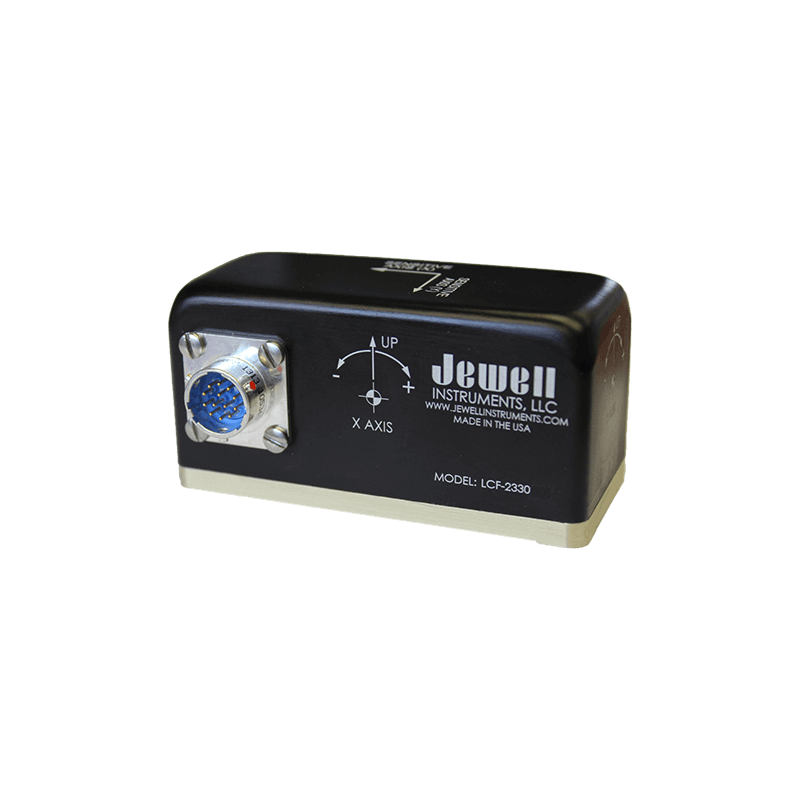
Servo inclinometers
They use servo technology to obtain accurate measurements and are often used in various industrial and scientific applications where precision is important.
Engineering the future of precision measurement
Both MEMS and Servo inclinometers serve essential roles in modern engineering applications. While MEMS inclinometers provide cost-effective, robust solutions for general-purpose use, Servo inclinometers excel in high-accuracy and stability-dependent applications. Althen Sensors & Controls offers expert guidance in selecting the right inclinometer technology to meet the stringent demands of your project.
Need assistance in choosing the right inclinometer, tilt sensor, or angular position sensor for your engineering application? Contact Althen Sensors & Controls today for expert consultation.