Machine failures in the pulp, paper, film and textile industry are expensive. Sensors are used to minimize downtimes and ensure consistently high product quality. Various parameters must be monitored to prevent damage to the paper or film web or to the machine. These include position detection, continuous checking of the winding diameter of the roll and the uniform, automatic winding and unwinding of roll material.
Winding/unwinding and rewinding is carried out at high speeds. Traditional measuring systems with measuring rollers or impellers quickly reach their limits here due to wear. Single point laser distance sensors or 2D laser scanners measure without contact, independent of material and surface, with constant precision at all speeds and a long service life.
Laser displacement sensors in the paper industry
The following questions play an important role in the paper and film industry:
- What is the current winding diameter of the paper roll?
- How much does the paper/film web vibrate during unwinding or winding?
Single point laser distance sensors and 2D laser scanners enable non-contact, material-independent and precise optical thickness measurement to determine the winding diameter as well as measurements of the vibration of the paper web at low and very high running speeds of the material.
The following schematic shows a side view of a roll on which paper, film or textiles are wound. In order to control the production process, it is necessary to know the winding diameter. To ensure a reliable and uninterrupted production process, while at the same time maximizing the process speed, the oscillation amplitude of the web must be monitored during winding and unwinding. If defined threshold values are exceeded, the rotational speed is reduced or an alarm message is generated. Depending on the process, an emergency shutdown may also be required if critical trigger thresholds are exceeded.
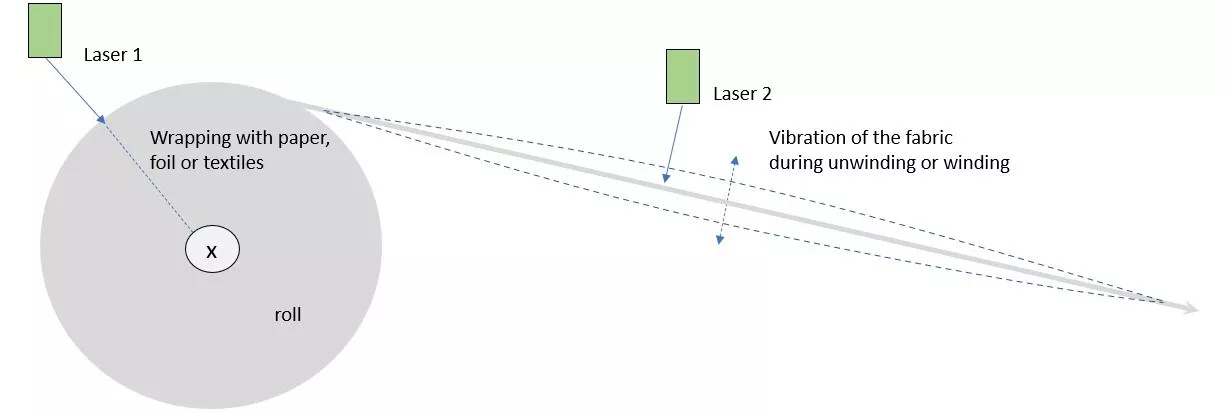
Suitable materials:
- Graphic paper, carbonless paper, thermal paper, filter paper, wallpaper, decorative paper, ...
- Base paper, coated paper, uncoated paper, machine-smooth, satin, ...
- Cardboard, paperboard, tissue paper, hygiene paper, ... (all basis weights and grammages)
Suitable machines for the use of single point laser distance sensors
and 2D laser scanners:
- Slitter rewinders, winders
- Winding machines, rewinders
- Slitters
-
DurableWear-free, long service life and low maintenance costs.
-
RobustSuitable for high running speeds, large distance tolerance range.
-
DigitalDigitalized measurement across the entire process (traceability and 100% documentation of measurement results).
-
Independent of materialLargely material-independent measurement, no material damage (abrasion marks/tracks).
Single point laser distance sensors in automated production
In automated production, triangulation sensors (single point laser distance sensors) are used to measure the thickness of components such as foils, sheets or pipes. During the production process, the component is moved by a robot through a defined area between two laser sensors. The thickness of the object to be measured can be determined, for example, by calculating two distance measurements (laser 1 and laser 2).
The measurements are suitable for quality control - deviations can be detected immediately and corrective measures initiated. Other areas of application include end-of-line inspection (final inspection of components after production, before they are packaged or further processed) as well as automated assembly and material usage optimization.
Production monitoring in the metal industry during the manufacture of an endless sheet of metal
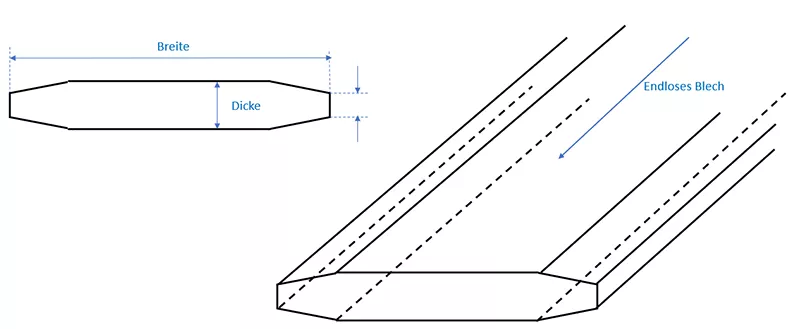
Measurement with single point laser
Laser triangulation sensors can be used to monitor geometric dimensions such as width, thickness, bevels, etc. Single point laser distance sensors, if punctual, random monitoring of the thickness is sufficient, or 2D laser scanners if the entire width or bevels need to be monitored.
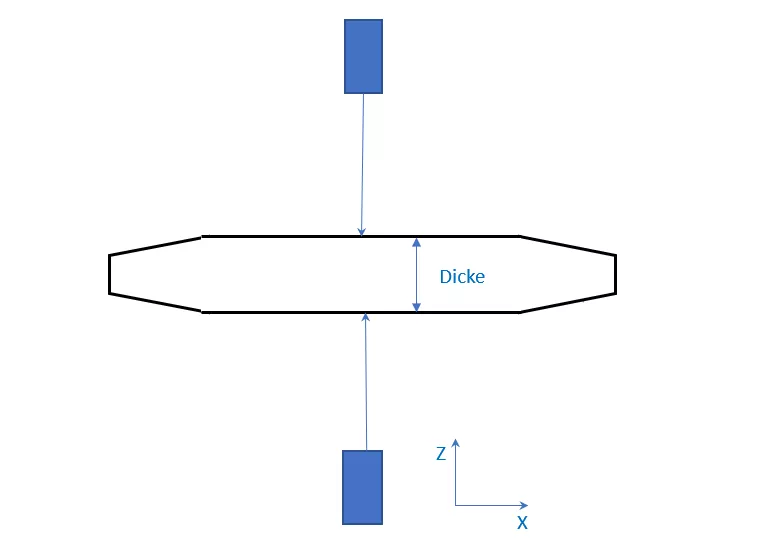
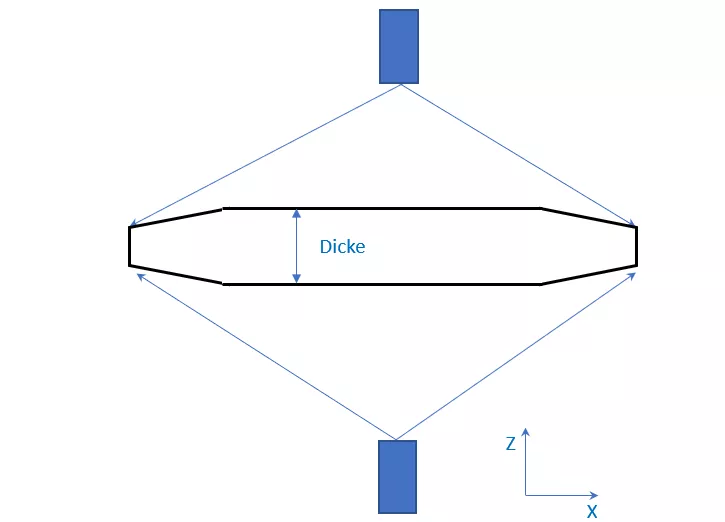
Measurement with 2D laser scanners
Monitoring of the geometry across the entire width with two opposing 2D laser scanners. The thickness is calculated across the entire width from the difference between the distance measurements of the opposing lasers.
Suitable sensor: FDRF627
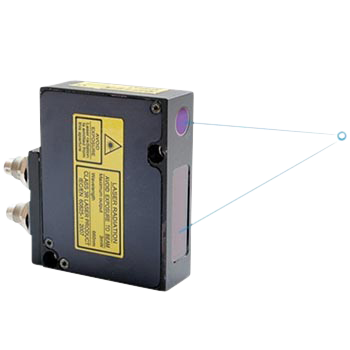
How single point laser sensors work
Our single point laser distance sensors work according to the principle of optical triangulation. The light beam is focused onto an object by the semiconductor laser. The scattered light beam reflected by the object is imaged by the input lens onto a CCD/CMOS line or a PSD element. The intensity of the reflected beam depends on the surface of the object being measured. If the object moves, the image also moves. The built-in signal processor calculates the distance to the object according to the position of the light spot image on the CMOS array.
Single point laser distance sensors are easy to use and align, as the laser dot on the measurement object is visible even in daylight. Depending on the design, the optical principle allows measuring distances of more than one meter. They detect both very small and large measuring ranges - depending on the required accuracy. The electronics of many sensor models quickly compensate for fluctuations in the intensity of the reflected laser dot.
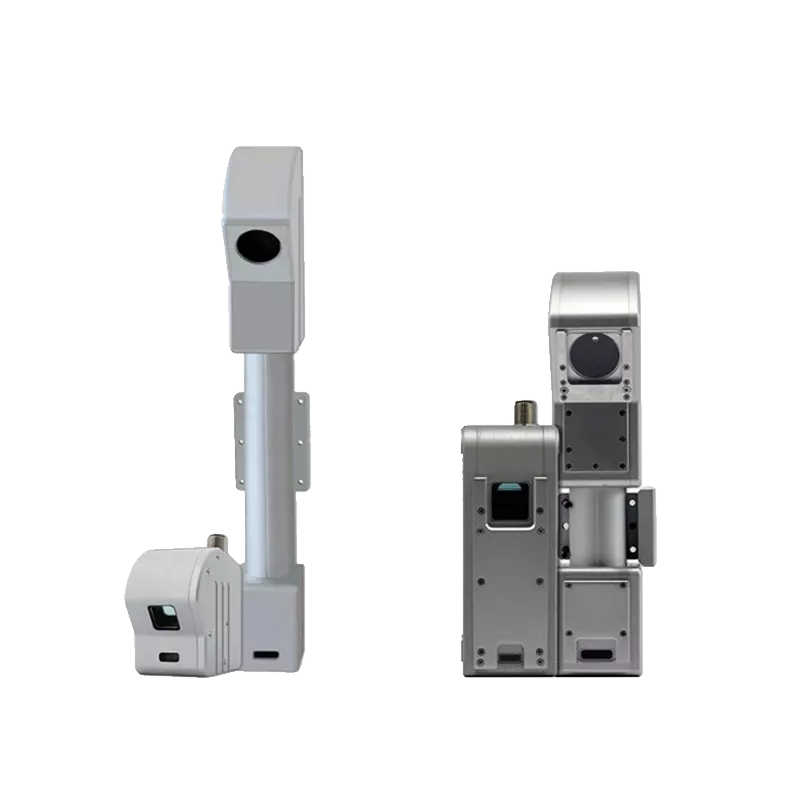
How 2D laser scanners work
2D laser sensors - also known as laser scanners - scan surfaces or bodies with a laser beam in lines or grids. This allows a two- or three-dimensional image of objects to be generated. Laser scanners consist of a scan head as well as driver and control electronics. The emitted laser beam is reflected by the measured object and picked up by the receiving optics. The beam is deflected by a rotating deflecting mirror and the received laser light is evaluated accordingly.
2D laser scanners are often used for multi-dimensional quality control, for example for profile or contour measurement. The classic laser works with red laser light. However, there are also blue lasers. This is suitable for high-temperature resistant, mirrored and semi-transparent objects, for example.