Railway safety and efficiency rely on meticulous maintenance of wheelsets. One of the critical parameters in wheelset inspection is the wheel diameter, which directly affects train stability, traction, and braking performance. Over time, due to wear and tear, wheel diameters reduce, impacting operational safety and requiring precise monitoring.
High-accuracy, non-invasive method
The Wheel diameter measuring gauge (FDK Series) offers a high-accuracy, non-invasive method to measure wheel diameter directly on rolling stock, providing essential data for maintenance teams to make informed decisions. Let’s explore the significance of wheel diameter measurement and the technology behind this advanced gauge.
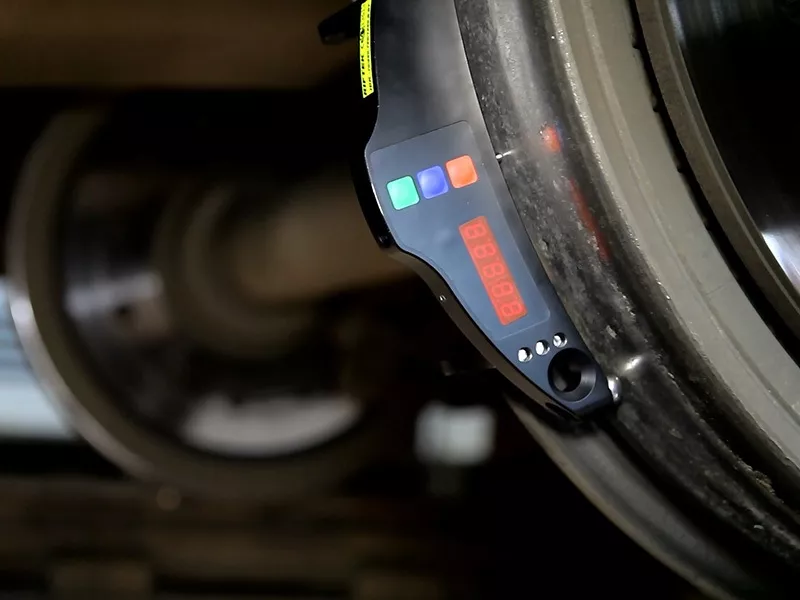
Why measure wheel diameter?
The wheel diameter is a fundamental parameter in railway operations for several reasons:
- Wear monitoring: Continuous wear of wheels can lead to uneven surfaces, reducing contact efficiency with rails and increasing derailment risks.
- Safety compliance: Railway authorities impose strict limits on wheel wear. Regular measurement ensures compliance with safety standards.
- Efficient maintenance planning: Knowing the exact wheel diameter allows railway maintenance teams to predict when re-profiling or replacement is necessary.
- Optimized train performance: Variations in wheel diameter among wheelsets can lead to imbalanced loads and increased rolling resistance.
Integrated laser measurement
One of the most innovative features of the FDK Series Wheel Diameter Measuring Gauge is its integrated laser sensor technology, which enhances measurement accuracy and repeatability. Real-time calculation of displacement changes as the laser interacts with the wheel. Consistent and highly repeatable measurements, independent of operator variability.
The sensor projects a laser beam onto a high-resolution CCD (Charge-Coupled Device) or CMOS sensor inside the gauge. The system then calculates the exact displacement of the measuring tip, allowing for precise diameter computation without requiring direct mechanical contact. So the gauge utilizes an integrated non-contact laser scanning method to ensure:
-
Sub-millimeter accuracyThe optical triangulation method ensures that even microscopic deviations in wheel diameter can be detected. This is critical for early wear detection and preventive maintenance.
-
No surface contact errorsSince laser technology eliminates the need for physical contact, it minimizes the influence of surface roughness and operator inconsistencies.
-
Fast data acquisitionThe laser sensor can process measurements within milliseconds, allowing railway technicians to inspect multiple wheels in a short time. The built-in microprocessor then converts the data into an easily readable format displayed on the digital screen.
-
High-speed scanningLaser sensors can accommodate various wheel diameters and profiles without the need for additional adjustments. The system is flexible enough to work with locomotives, metro trains, trams, and high-speed rail wheelsets.
Measurement principle
The gauge operates on the chord measurement method, where the wheel diameter is calculated using the known length of a segment chord. This is achieved through:
- Ball bearing supports placed on the wheel surface.
- A measuring tip that detects displacement.
- A built-in digital display showing precise readings.
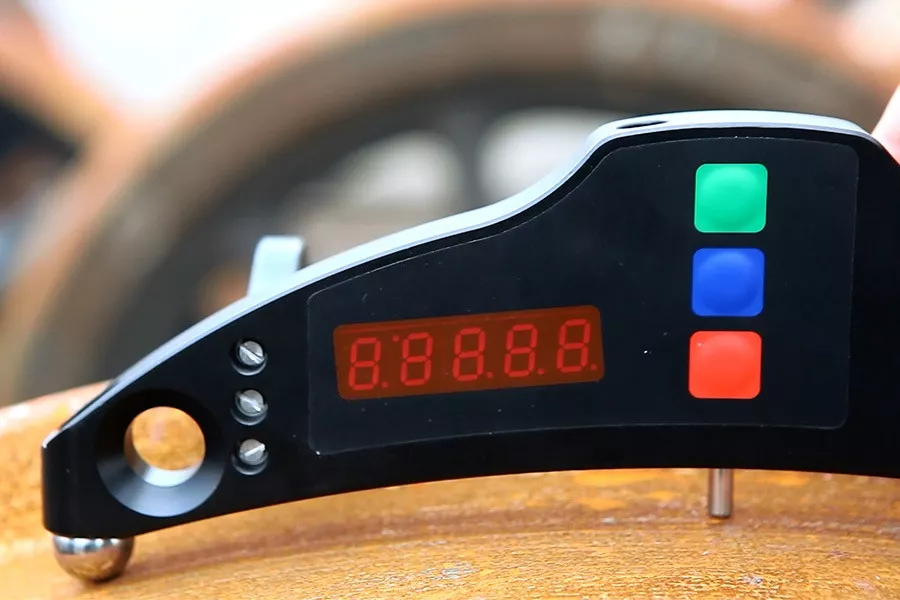
Measurement procedure
- Surface preparation: Clean the wheel surface from debris to ensure accuracy.
- Gauge placement: The ball supports and measuring tip must firmly contact the wheel.
- Activation: Press the measurement button, and within a second, the display shows the wheel diameter.
- Averaging mode (optional): For enhanced accuracy, multiple readings can be averaged to minimize surface defects’ impact.
Digital calibration for accuracy
Calibration is crucial for ensuring precise readings. The gauge features two main calibration procedures:
- Sensor zero calibration: Ensures the baseline reading is correct using Johansson gauge references.
- Device base calibration: Verifies the distance between ball bearing supports using a reference wheel.
Applications in railway maintenance
The FDK Series Wheel Diameter Measuring Gauge is widely used in:
- Mainline railway depots: For regular inspections of trains, locomotives, and wagons.
- Metro and trams depots: Ensuring compliance with urban rail safety standards.
- Wheelset manufacturing: Quality control checks during production.
- On-site maintenance: Quick assessments during in-field service inspections.
Other railway hand tools
The Wheel diameter measuring gauge is just one of a few other hand tools that offer a solution in measuring railway and wheel parameters. We offer the following railway portable measuring tools within our entire Railway measurement systems portfolio.
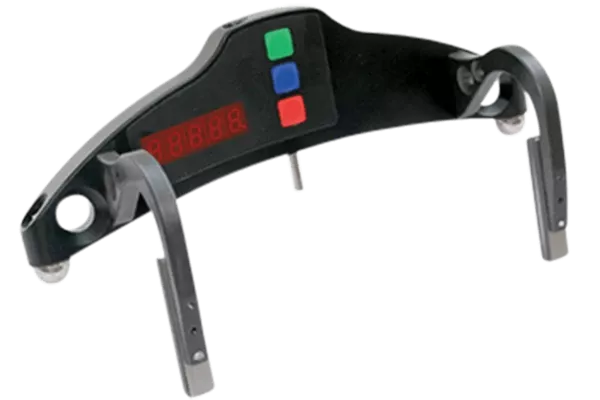
Wheel diameter measurement tools
High-accuracy, non-invasive method to measure wheel diameter directly on rolling stock, providing essential data
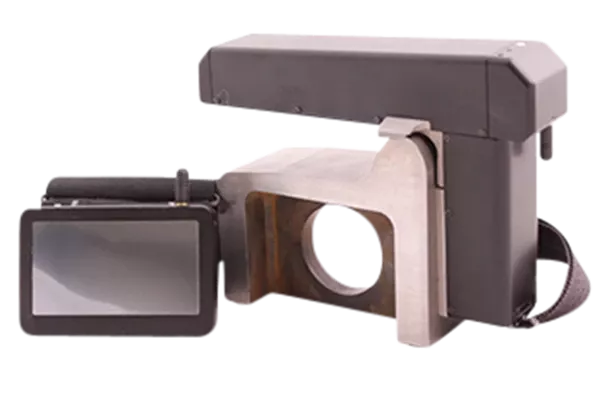
Wheel profile measurement tools
Wheel profile measuring instruments are used to measure the properties and dimensions of a wheel's profile.
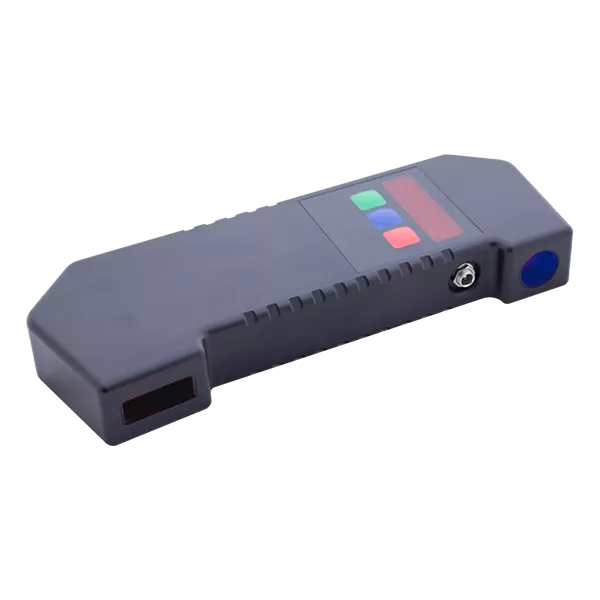
Back-to-Back measurement tools
Made for non-contact measurement of back-to-back distance between track wheels during repair, examination, inspection and formation of wheel sets.
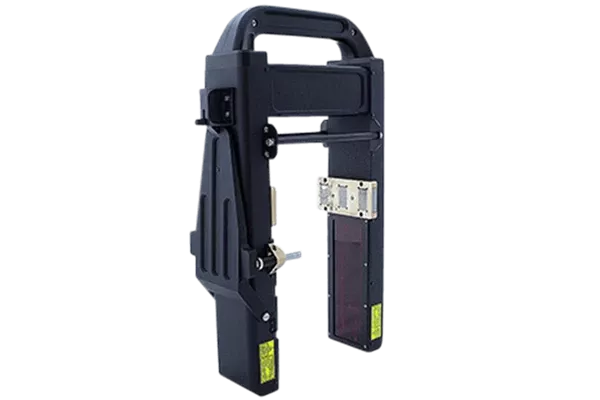
Disk brake profile measurement tool
Measuring instruments for disc brake profiles are used to measure the geometry and wear of disc brakes.
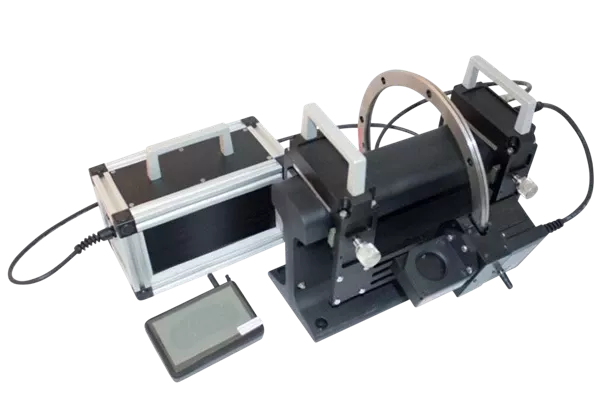
Rail profile measurement tools
Measuring instruments for rail profiles are used to measure the geometric characteristics of rail tracks.
Integrated non-contact laser measurement
The FDK series Wheel diameter measuring gauge is an indispensable tool for railway professionals. Its laser sensor technology, digital precision, ease of use, and robust design make it ideal for regular maintenance, helping ensure railway safety and efficiency.
By integrating non-contact laser measurement, technicians can now achieve higher accuracy, reduce errors, and optimize maintenance schedules, ultimately leading to better rail performance and longer wheel life.