Strain gauges are a cornerstone of accurate force measurement in industrial and test environments. When combined with a Wheatstone bridge circuit, they enable precise detection of both static and dynamic loads. This article explains how strain gauges work, how signal accuracy is enhanced through bridge configurations, and how to manage factors like temperature effects and cross-talk—key for anyone working with force sensors or structural monitoring systems.
Strain gauges and resistance change
A strain gauge with a resistance of 350 ohms and a gauge factor (GF) of 2, mounted to a structure undergoing 1000 microstrain (µε), will experience a resistance change of 0.7 ohms. Although modern digital ohmmeters can detect such a change, resolving just 1/1000th of the applied load requires detecting a difference between 350.0000 and 350.0007 ohms—a level of precision that demands highly sensitive circuitry.
Measuring dynamic forces with strain gauges
When the force to be measured is dynamic—such as a machine component striking a locating stop—the measurement setup can be simplified. One effective method involves:
- Exciting a single strain gauge with a constant current source.
- Using an AC amplifier to isolate and amplify only the AC component of the signal.
- Implementing a capacitor to remove any common mode voltage, leaving only the relevant dynamic signal for amplification.
This approach delivers a clean and responsive control signal, ideal for high-speed automation or impact force detection.
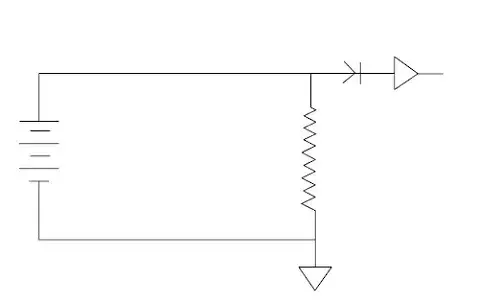
Static and dynamic measurement
A more robust and versatile solution involves the use of a Wheatstone bridge circuit, which is suitable for both static and dynamic force measurements. Conceptually, the Wheatstone bridge functions as two voltage dividers connected to a common excitation source. When all resistors in the bridge are equal, the voltage at the midpoints is the same, resulting in zero output voltage. However, even a small resistance change in one arm produces a differential signal, which can be amplified by a DC amplifier to deliver a high-resolution output.
When a Wheatstone bridge is constructed with four equal strain gauges, it is considered balanced in its unstrained state. Any mechanical strain on the structure will alter the resistance of one or more gauges, unbalancing the bridge and generating a corresponding output voltage. The strategic placement of gauges enables this circuit to:
- Amplify desired signals (e.g., bending moments)
- Cancel out unwanted influences (e.g., thermal drift or axial forces)
Temperature Compensation and Signal Isolation
One of the Wheatstone bridge's key benefits is its ability to cancel non-strain-related resistance changes, such as those caused by temperature variations. For example:
- Gauges placed in tension and compression zones can be configured to additively enhance signal output while negating common-mode effects like thermal expansion.
- This allows engineers to isolate strain in specific force directions or axes, improving the accuracy of multi-axis force sensors.
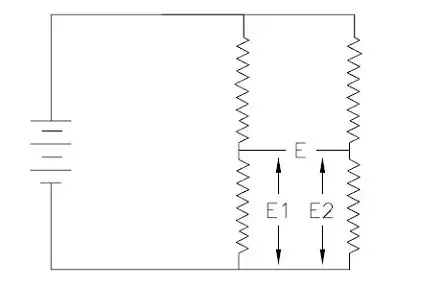
Cross-talk minimization and shunt effects
For precise force measurements, it's critical that each gauge pair produces equal but opposite resistance changes. However, this balance can be unintentionally disrupted. A common issue arises when users introduce external passive resistances (shunts) across the bridge arms:
- This not only alters the gauge’s base resistance, but also its effective gauge factor.
- While sometimes used deliberately to correct cross-talk or fine-tune the force sensitivity axis, such modifications can unintentionally degrade sensor performance.
Certain commercially available readout instruments contain integrated shunt or T-balance networks, which may affect the true output of the sensor. Users should carefully evaluate these effects during system integration to avoid misinterpretation of the force signal.
Precision matters in strain gauge and force sensor applications
In summary, whether measuring high-speed impacts or slow mechanical loads, choosing the right strain gauge configuration and understanding the nuances of Wheatstone bridge circuits is essential for accurate and reliable force measurement.
Applications that benefit from this knowledge include:
- Industrial test benches
- Automated production lines
- Aerospace structural testing
- Biomechanical force sensing
- Robotic actuator feedback