Um Veränderungen an Bauteilen festzustellen, lassen sich Dehnungsmessstreifen (DMS) zur Feindehnungsmessung einsetzen, die direkt an der Oberfläche des Prüfkörpers aufgebracht werden. Welche Einflussgrößen bei der Dehnungsmessung relevant sind, zeigt dieser Blogbeitrag auf.
Dehnungsmessstreifen sind ein gefragtes Prüfmittel, um Materialeigenschaften von Werkstoffen und Bauteilen zu beurteilen. Sie können unkompliziert am zu prüfenden Material oder Bauteil aufgebracht werden und erfassen dann die Widerstandsänderung, die durch eine Dehnung am Prüfkörper verursacht wird. So können z. B. Kennwerte wie die Festigkeit, Steifigkeit oder Bruchdehnung eines Materials ermittelt werden. Bestimmte Einflussfaktoren können jedoch das Messergebnis beeinträchtigen und sollten bei der Vorbereitung von Zug-, Schub-, Druck- oder Biegeprüfungen berücksichtigt werden. Dazu gehören die Größe des Bauteils und die Messgitterlänge, das Trägermaterial, der K-Faktor, das Temperaturverhalten hinsichtlich Umgebungstemperatur, DMS-Material und Bauteilwerkstoff, die Installation und die Querdehnungsempfindlichkeit. Wir gehen auf diese Faktoren nachfolgend einzeln ein. Je nach zu erwartenden Einflüssen kann ein für die Anwendung passender DMS gewählt werden.
Größe des Bauteils und Messgitterlänge
Je größer das Bauteil und die zu prüfende Stelle sind, desto besser lässt sich ein möglichst großer DMS platzieren, der über ein größeres Messgitter verfügt und die Dehnung umso präziser abbilden kann. Wenn es sich um einen nicht-homogenen Werkstoff handelt, der vielleicht Verjüngungen oder Sollbruchstellen aufweist, wird das Messergebnis bei einem großen DMS fehlerhaft, da an diesen Stellen ein Dehnungsgradient besteht, der von den größeren Messgittern nicht wahrgenommen wird. Hier ist ein kleinerer DMS zu bevorzugen, der direkt an der verjüngten Stelle aufgebracht wird. In der Regel ist dies bei einer Dehnung die am meisten belastete Stelle.
Bestimmte inhomogene Materialien, wie Faserverbundwerkstoffe, profitieren ebenfalls von einem größeren DMS, da die größeren Messgitterlängen über mehrere Faserbündel hinwegmessen und so eine gute Mittelung über die Werkstoffprobe erzielen.
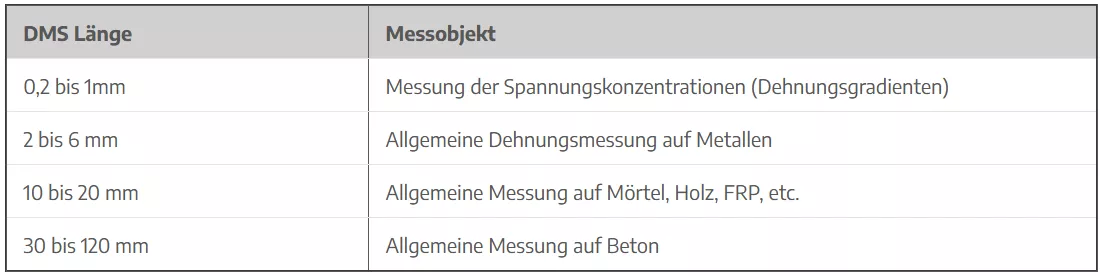
Trägermaterial des DMS
Je nach Anwendung, Umgebungstemperatur, möglichen Lastzykluswechseln, der geforderten Festigkeit oder der Höhe der Dehnung sind DMS mit einem passenden Trägermaterial auszuwählen. Die gängigste Legierung ist Konstantan, die bei geringer Temperaturabhängigkeit einen geringen K-Faktor (Dehnungsempfindlichkeit des DMS) aufweist und einen spezifischen Standard-Widerstandwert von 120 Ohm hat. Für Anwendungen mit hohen Temperaturen, aber auch kryogene Anwendungen bei weniger als minus 150 Grad, können DMS mit höheren spezifischen Widerständen (350 Ohm oder 1.000 Ohm) eingesetzt werden, die mit Karma beschichtet sind (eine Nickel-Chrom-Legierung).

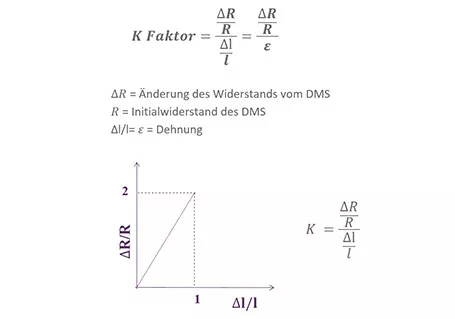
K-Faktor
Der K-Faktor bezeichnet die Dehnungsempfindlichkeit eines DMS. Diese ist stets temperaturabhängig. Wie sich der K-Faktor des jeweiligen DMS temperaturbedingt ändert, ist herstellerseitig angegeben und sollte für die jeweilige Anwendung berücksichtigt werden.
Weitere Informationen
Temperaturverhalten
Temperaturen haben in verschiedener Hinsicht Einfluss auf das Ergebnis einer Dehnungsmessung. Zu beachten sind die Umgebungstemperatur sowie das Temperaturverhalten des DMS-Materials und des Prüfkörpers. Wenn alle Parameter bestmöglich aufeinander abgestimmt sind, können temperaturbedingte Messfehler vermieden werden.
Wenn sich der DMS aufgrund des entstehenden Stromflusses selbst zu sehr erwärmt, kann eine Nullpunktdrift entstehen und das Messergebnis verändern. Daher sollte bei höheren Speisespannungen ein DMS mit höherem spezifischem Widerstand gewählt werden, damit er sich weniger stark erwärmt. Grundsätzlich kommt es dabei auch auf die Dauer der Prüfungen an. Bei Langzeitprüfungen ist eine höherohmige Variante ratsam; bei kürzeren Zugversuchen ist der Aspekt der Selbsterwärmung unerheblich.
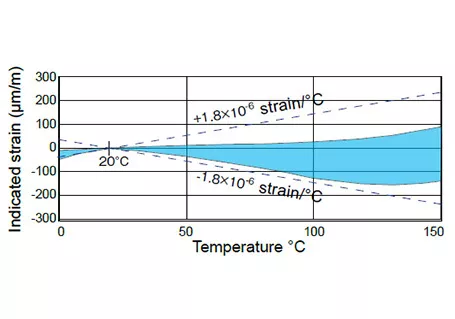
Ebenfalls zu beachten sind bei Langzeitprüfungen die jeweiligen Temperaturausdehnungskoeffizienten der unterschiedlichen Materialien, also des Bauteils und des Trägermaterials des DMS. Da DMS auch Temperaturveränderungen als vermeintliche Dehnung wahrnehmen, würde bei sehr voneinander abweichenden Temperaturkoeffizienten als Messsignal die Differenz der beiden Koeffizienten als Dehnung angezeigt werden. Daher sollten beide Werte nah beieinander liegen, um scheinbare Dehnungen zu vermeiden.
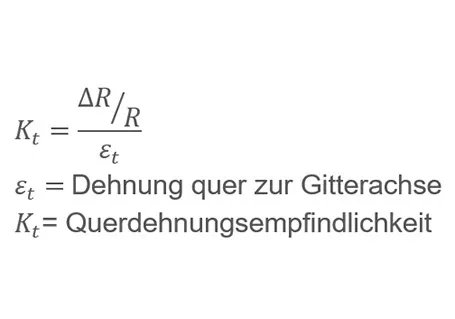
Querdehnungsempfindlichkeit
In erster Linie dehnt sich ein DMS in Richtung der jeweiligen Gitterlängsachsen. Jedoch kann er auch in Querrichtung auf eine Krafteinwirkung reagieren. Diese Querdehnungsempfindlichkeit wird stets herstellerseitig angegeben, um eventuelle Messfehler zu berechnen. Letztere entstehen vor allem bei mehrachsigen Spannungsfeldern, bei denen vorab nicht klar ist, wo die Kräfte angreifen werden. Um ein genaues Prüfungsergebnis zu erzielen, sollte an verschiedenen Stellen des Bauteils in unterschiedlichen Winkeln gemessen und die Querdehnungsempfindlichkeit zusätzlich herausgerechnet werden.
Whitepaper: Richtig messen mit DMS
Erfahren Sie alles über Funktionsweise, Eigenschaften, Vorteile, Einflussgrößen und Kennwerte von Dehnungsmessstreifen.
Für ein sicheres Messergebnis Parameter genau definieren
Dehnungsmessstreifen ist nicht gleich Dehnungsmessstreifen. Um den passenden DMS für die jeweilige Applikation auszuwählen, sollten mögliche Einflussfaktoren eingehend geprüft werden. Je genauer die Parameter und die zu erwartende Dehnung definiert werden können, desto einfacher ist die Auswahl des passenden DMS und desto präziser fällt das Messergebnis aus. Wir unterstützen bei der Auswahl der Dehnungsmessstreifen und beraten bei der Durchführung von geeigneten Prüfungen zur Ermittlung von Materialkennwerten.