Die Herausforderung
Um das Wasserstoffauto für den öffentlichen Straßenverkehr zuzulassen und alle 1.301 Anforderungen der niederländischen Fahrzeugbehörde (RDW - the Netherlands Vehicle Authority) zu erfüllen, legte das Eco-Runner Team dieses Jahr besonderer Wert auf die Sicherheit. Neben der Technik wurden für den Straßenverkehr u.a. Nummernschilder, Spiegel, größere Fenster und ausreichende Lampen benötigt. Dass die Effizienz nicht auf Kosten der Sicherheit gehen muss, wollte das Team mit einem Weltrekordversuch beweisen. Das Team der Universität Delft plante, mit seinem Auto 2.056 Kilometer weit zu fahren, mit nur 1,45 Kilogramm Wasserstoff. Der Rekordversuch fand auf der Strecke der berüchtigten Elfstedentocht statt: Hier legte das Team zehn Runden in nur 72 Stunden zurück. Auf diese Weise wollten die Studenten zeigen, dass es im Vergleich zu den aktuellen Industriestandards noch viel zu gewinnen gibt, und Impulse für eine nachhaltige Zukunft setzen.
Das Eco-Runner Team Delft verwendet verschiedene Sensoren von Althen - sowohl im Auto selbst als auch in der Testausrüstung. So werden beispielsweise Kraftsensoren im Bremspedal zur Steuerung der Bremslichter, Drucksensoren im Bremssystem zur Erkennung von Druckverlusten und ein Drehmomentsensor zur Bestimmung und Optimierung der Effizienz des Antriebsstrangs eingesetzt.
Der Nachteil von Massenbauteilen
Die größte Herausforderung bei vielen Teilen aus der Automobilindustrie ist die Anwendung in einem Prototyp. Oft gibt es zwar Serienteile für ein System, aber diese Produkte sind oft zu groß, schwer oder unnötig aufwendig für unsere Anwendung. In anderen Fällen funktionieren diese Teile nur mit bestehenden Systemen und es können z.B. keine Rohdaten ausgelesen werden. Hier bietet Althen Lösungen mit präzisen und spezialisierten Sensoren an. Dabei sind die Sensoren gleichzeitig noch einfach und standardisiert genug, um sie flexibel in einem maßgeschneiderten System einzusetzen.
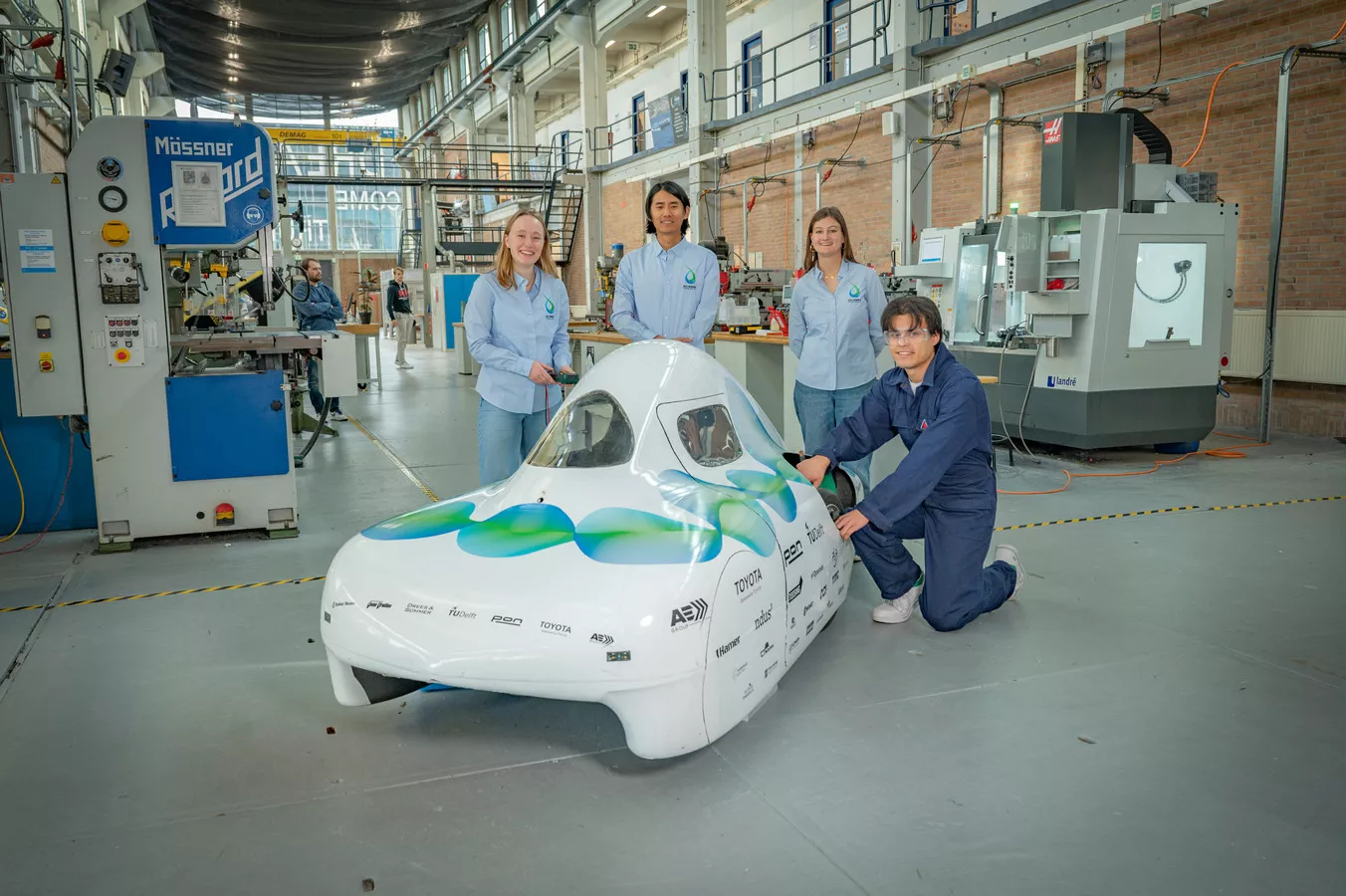
Rotierender Drehmomentsensor zur Optimierung der Effizienz
Mit dem Drehmomentsensor kann auf einem Prüfstand die Leistung des Motors gemessen werden. In Verbindung mit der elektronischen Leistung, die an verschiedenen Punkten des Antriebsstrangs gemessen wird, kann das Team die Effizienz bestimmen und optimieren. Auf der Teststrecke ist dies jedoch weder genau noch wiederholbar oder praktisch möglich. Da der Sensor im gesamt möglichen Bereich mit einem Drehmoment von -50 bis +50 Nm und einer Drehzahl von 0 bis 650 U/min eingesetzt werden kann, ist es dennoch möglich, jedes Belastungsszenario zu simulieren.
Da es bei diesen Optimierungen oft um Bruchteile von Prozenten geht, ist eine hohe Genauigkeit der Messgeräte sehr wichtig. Außerdem können die Daten einfach mit der TorqView6-Software überwacht und exportiert werden.
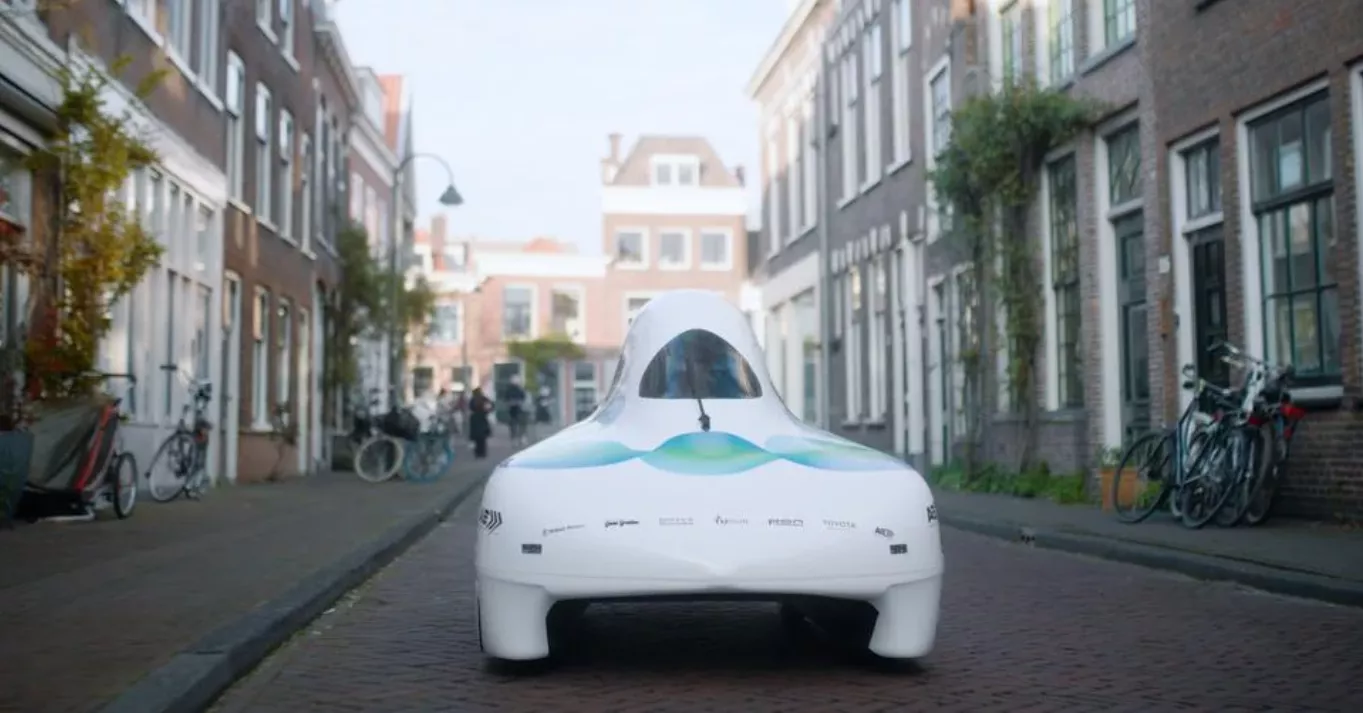
Wäge- und Drucksensoren für die Bremse
Die RDW erwartet, dass eine Warnleuchte aufleuchtet, wenn bei einer bestimmten Kraft auf das Bremspedal zu wenig Druck in den Bremsleitungen vorhanden ist, da dies auf ein Leck und den Verlust von Bremsflüssigkeit hinweisen kann. Um dies zu messen, werden ein Gewichtssensor im Bremspedal sowie zwei Drucksensoren an den beiden getrennten Kreisläufen der vorderen und hinteren Bremse eingesetzt. Mithilfe der Prüfstatistik kann vorhergesagt werden, welcher Druck in den Kreisläufen bei einer bestimmten Bremskraft auftreten sollte. Auf diese Weise kann ein mögliches Leck erkannt werden. Wenn der gemessene Druck niedriger ist als der Druck, der bei der gemessenen Kraft auf das Bremspedal erwartet wird, leuchtet die Warnleuchte auf.
Produkte
Diese Sensoren kamen zum Einsatz:
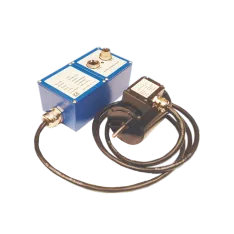
ORT 230/240 Drehmomentaufnehmer
- Messbereich: 0,02 bis 100 Nm
- Geringes Trägheitsmoment - Hohe Drehzahlfähigkeit
- Berührungslose/bürstenlose Messung
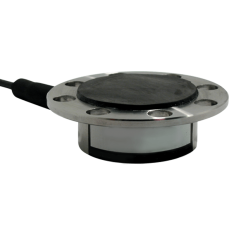
ALF304 Pedalkraftaufnehmer
- Messbereiche 0 ... 2.500 N
- Für Druckbelastung
- Linearitätsabweichung 0,05 % v.E.
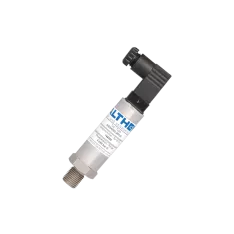
AGS4000 Standard-Druckaufnehmer
- Messbereich: 0-500 mbar bis 0-700 bar
- DMS-Technologie
- 0,4% Genauigkeit & ±2 % FS Gesamt-Fehlerbereich
Einsatz des Drehmomentsensors
Der Drehmomentsensor wird in der Mitte des Prüfstandes zwischen zwei Elektromotoren angebracht: Zwischen dem leistungsfähigen Motor des zu prüfenden Fahrzeugs und einem zweiten Motor, der als mechanische Last dient, um verschiedene Fahrbedingungen zu simulieren. Im Laufe der Jahre wurden von den Teams verschiedene Reduktionsteile hergestellt, um das Schraubenmuster des Flansches am Sensor an die verschiedenen Elektromotoren anpassen zu können. Der Sensor wurde auch direkt an den Speichen der Felge montiert, um Motoren im Rad zu testen. Hier sind die flexiblen Kupplungen zwischen den beiden Seiten wichtig, um eventuelle Produktionsabweichungen oder Abweichungen vom Rotationsgleichgewicht auszugleichen. Der Datenexport und die Versorgung des Sensors erfolgt über den digitalen Ausgang mit dem entsprechenden Adapterkabel. So können die Daten einfach über USB und die TorqView6 Software ausgelesen und protokolliert werden.
Bremspedal und Schaltkreise
Der Wägesensor hat zwei Befestigungsflächen, auf einer davon ist eine Platte montiert, auf die die Kraft mit dem Fuß aufgebracht wird. Auf der anderen Fläche befindet sich ein Bauteil, das an der Welle befestigt ist, um die das gesamte Pedal schwenkt. Die beiden Drucksensoren sind an den beiden getrennten Bremskreisen angebracht, so dass der Druck für beide Kreise getrennt gemessen werden kann.
Unserer Erfahrung nach ist die Arbeit mit Althen sehr wertvoll für unser Projekt. Diese Meinung haben wir auch von mehreren Eco-Runner-Alumni gehört. Es ist spürbar, dass Althen sich in unser Projekt einbringt und mit Begeisterung hilft, wo immer es möglich ist. Wir können jederzeit Fragen stellen und uns wird gut geholfen. Außerdem werden die Teile schnell geliefert und wir erhalten wertvolle Hilfe bei der Suche nach den richtigen Produkten für alle Anwendungen.
Die Ergebnisse für Eco-Runner
Die Effizienz des Antriebsstrangs wird seit Jahren mit einem Althen-Drehmomentsensor getestet und optimiert. Dank dieser Tests hat das Team mehrere große Erfolge erzielt. So konnte das Eco-Runner Team Delft in den letzten Jahren den Eco-Marathon gewinnen, bei dem die Optimierung des Motors auf dem Prüfstand entscheidend für eine hohe Effizienz war. Darüber hinaus hat Eco-Runner es tatsächlich geschafft, einen Guinness-Weltrekord aufzustellen, bei dem die umfangreichen Tests und Messungen unabdingbar waren, um drei Tage lang nonstop fahren zu können.Das Team Eco-Runner hofft, noch in diesem Jahr ein vollständig RDW-zertifiziertes Bremssystem im Eco XIV fertigzustellen, das verschiedene Althen-Sensoren verwendet. Diese Zertifizierung wird den zuverlässigen Betrieb und die einfache Integration der Sensoren belegen.
Benötigen Sie Hilfe bei einer messtechnischen Herausforderung?
Kontaktieren Sie uns! Wir sind gerne für Sie da!