Les principales pièces de l'A350 XWB, telles que le fuselage, les ailes, les moteurs et l'empennage, sont fabriquées dans les usines européennes d'Airbus en France, en Allemagne, en Espagne et au Royaume-Uni. Sur la chaîne d'assemblage final de l'A350 XWB (FAL) à Toulouse, toutes les pièces de l'avion sont ensuite assemblées comme un puzzle de haute technologie.
Le fuselage de l'A350 XWB se compose de trois parties principales - une partie avant, une partie centrale et une partie arrière. Toutes les parties - y compris le train d'atterrissage - sont assemblées à la première station d'assemblage principale, la P50. Une fois cette étape terminée, le fuselage est transporté vers le poste d'assemblage P40, où les sections d'aile et de queue sont assemblées. La chaîne d'assemblage final est extrêmement flexible. Elle peut être utilisée aussi bien pour l'A350-900 que pour les modèles -1000.
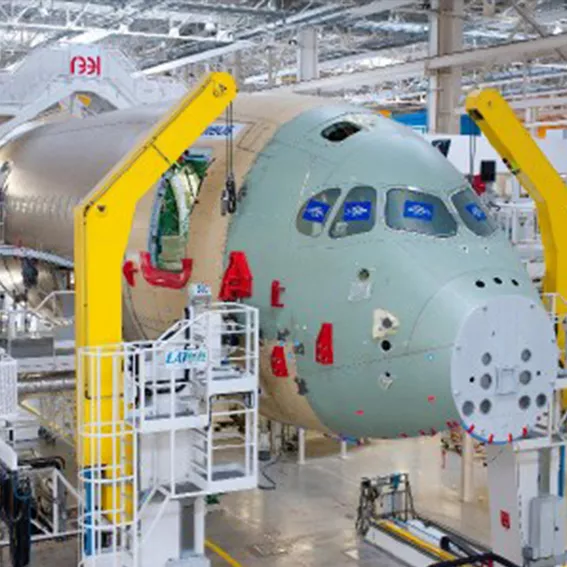
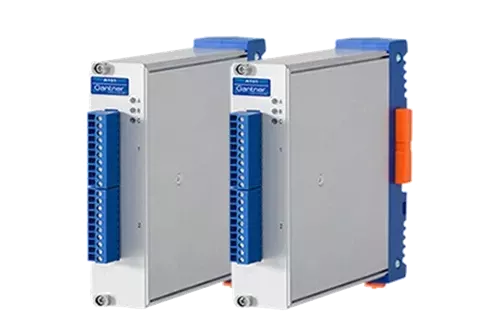
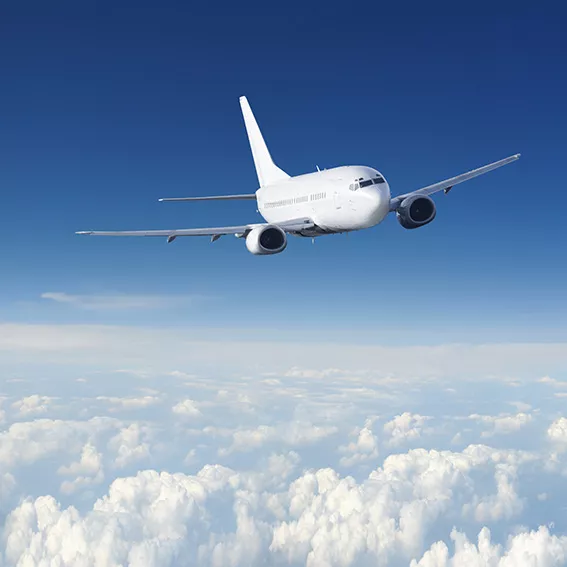
Processus d'assemblage
Le processus d'assemblage et de liaison des grands sous-ensembles est une tâche complexe. En particulier pour les pièces en plastique renforcé de fibres de carbone (PRFC), utilisées en grande quantité sur l'A350 XWB, la gravité et les conditions ambiantes entraînent des déformations géométriques. Afin de garantir une localisation et un positionnement sûrs des grandes pièces de l'avion, un système d'assemblage est assisté par des mesures. Une série de systèmes de positionnement multiaxes soulève, déplace et aligne la structure du fuselage et des ailes afin de garantir un ajustement optimal. Pour protéger au mieux les grandes pièces pendant l'alignement, des cellules de pesage sont utilisées et montées dans le mécanisme d'entraînement du positionneur. Elles permettent de contrôler les forces exercées sur la structure pendant le mouvement. Les éventuels dommages dus aux tensions et aux contraintes subies par les pièces pendant l'assemblage sont ainsi évités.
L'ensemble du système de montage contient 300 cellules de pesage. Les cellules de pesage à un axe surveillent la course (Fz) et les cellules de pesage à trois axes surveillent la force pendant le montage (Fx, Fy et Fz). Toutes les cellules de pesage ont une sortie à double pont pour permettre une redondance dans le système. Les cellules de pesage sont connectées à un système de mesure Q.bloxx de Gantner. Au total, 150 modules Q.bloxx A101 sont utilisés pour la surveillance primaire des forces. De plus, 300 modules Q.bloxx A102 sont utilisés pour la surveillance redondante.
Fonctionnement du système de mesure
La distance entre la cellule de pesée et le système de surveillance peut atteindre 75 mètres. Le placement des convertisseurs de signaux à proximité des points de mesure proprement dits est l'une des exigences les plus importantes lors de la conception d'un système de montage basé sur la mesure. La granularité optimale des canaux du Q.bloxx, combinée à la possibilité de combiner et de répartir librement les modules, offre à Airbus une flexibilité maximale. Les modules communiquent via RS-485 avec un contrôleur Q.station placé au centre, qui se charge des tâches d'acquisition de données, de synchronisation et de contrôle. La transmission des données s'effectue via un protocole très efficace avec une vitesse de transmission pouvant atteindre 48 MBaud. Malgré la structure décentralisée, la mesure s'effectue de manière synchrone avec une gigue de moins de 1 µs. Cette architecture garantit des résultats de mesure fiables avec un câblage réduit.
Le système de surveillance de la chaîne de montage comprend un PLC Schneider Electric Safety. Le contrôleur Q.station à architecture ouverte communique avec le Safety PLC via le mode TCP/IP. En séparant le contrôleur Q.station des modules de mesure, la communication et la compatibilité avec le système de surveillance sont nettement optimisées. Un autre avantage pour Airbus est la possibilité de remplacer le contrôleur si les exigences en matière d'interface ou de performance changent - sans nouvel investissement important.
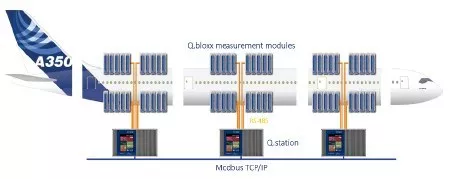
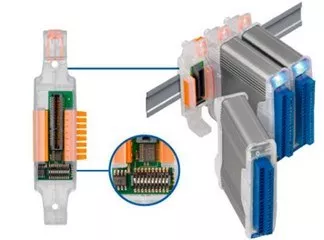
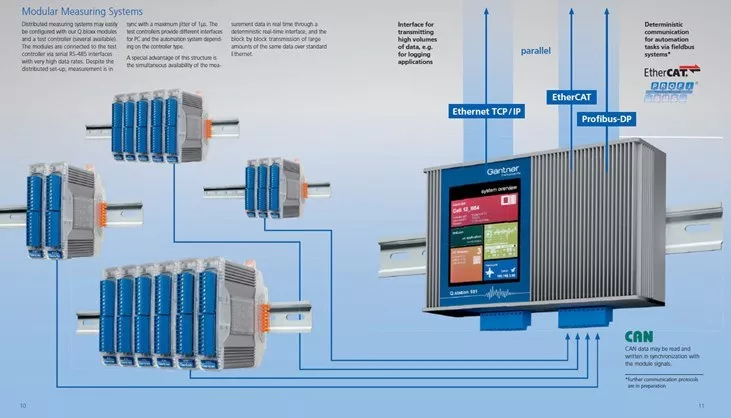
Fonctionnement et structure de la solution de mesure
Les Q.bloxx A101 et A102 sont équipés de microprocesseurs embarqués, de convertisseurs A/N 24 bits, de filtres matériels anti-alias et d'une isolation complète à trois voies jusqu'à 500 VDC sur chaque canal. Les modules de mesure supportent des taux d'échantillonnage allant jusqu'à 100 kHz par canal.
Comme la transmission de grandes quantités de données brutes sollicite fortement les ressources du réseau, chaque module est équipé d'un FPGA. Celui-ci permet un conditionnement complet du signal et un traitement des données directement à l'endroit où les données du capteur entrent dans le système de mesure. Ainsi, seules les données contenant des informations importantes pour le processus, telles que la valeur moyenne, la mesure min/max et la mesure des pics, sont envoyées au système de surveillance. Cela évite de longs temps de chargement et améliore les temps de réaction.
Q.bloxx pour des mesures décentralisées, rapides et précises
Les coûts de montage de la cabine d'avion représentent jusqu'à 40% du budget total de la construction. C'est pourquoi la disponibilité fiable du système de montage revêt ici une importance particulièrement élevée. Chaque module Q.bloxx est relié à un socle qui contient une puce de mémoire flash intégrée avec une copie de la configuration complète du module. Ainsi, en cas de remplacement d'un module défectueux, il n'est pas nécessaire de reconfigurer manuellement le nouveau module ou le système de surveillance. Les modules peuvent être remplacés en cours de fonctionnement, sans qu'il soit nécessaire de couper l'alimentation électrique. En seulement 5 secondes, la configuration est copiée du socle sur le nouveau module. La mesure se poursuit automatiquement dès que la configuration est rétablie. La fonction "Hot Swap" du Q.bloxx permet une maintenance et un entretien efficaces du système de mesure, minimise les temps d'arrêt et augmente l'efficacité de la ligne d'assemblage final.
Graphique 1 : @AIRBUS S.A.S. 2012 photo by e*m company / P. Pigeyre
autres photos/graphiques : GI