At Althen Sensors & Controls, we are committed to pushing the boundaries of sensor technology to meet the evolving needs of the aerospace industry. With our advanced sensors, aerospace engineers can achieve unparalleled levels of performance, efficiency, and safety in their mission-critical applications.
Gyroscopes - the revolutionary MEMS
Back in the days traditional spinning wheel mechanical gyroscopes where used in aircrafts. They were heavy, big and expensive. And like all things that spin on bearings, they needed routine maintenance. These days our MEMS Gyroscopes and Air Pressure Probes are commonly used in the aviation sector. These MEMS Gyroscopes are tiny, especially compared to the old ones. MEMS Gyroscopes don't contain moving parts and they are named after the MEMS technology. An unique silicon ring technology that is coupled with closed loop electronics. The hermetically sealed ceramic body provides the gyroscopes with excellent resistance to humidity and temperature. The MEMS Gyroscopes offer highly accurate and stable performance over temperature and time. The new DMU30 is the first of a family of High Performance IMUs (HPIMUs).
MEMS air data measurement
Next to the MEMS gyroscopes the air pressure probes are often used in the aviation branche. They represent a robust method for air data measurement. Designed for high-accuracy, real-time applications, they return the angles of an aircraft or vehicle with respect to the apparent wind. Air Pressure Probes can be heated internally for use on high-altitude Unmanned Aerial Vehicles (UAV), that makes them perfectly suited for the aviation sector. Data reduction performance in real-time by on-board computers and flight control systems. Almost 90% of the air pressure probes are tailor made, in order to suit your specific requirements.
Accelerometers
An Accelerometer helps a device understand its surroundings and the forces around it better. These forces may be static, such as gravity, or they could be dynamic – caused by moving or vibration. Accelerometers are used extensively in transportation such as aerospace, aviation and the automotive industry as well as inertial navigation and guidance systems in such things as airplane and ship autopilots. We offer a wide range of high precision accelerometer sensors to measure linear acceleration and deceleration with the highest levels of accuracy and reliability. Our sensors are used in demanding aerospace, aviation, military and industrial applications around the world.
Inertial measurement units (IMUs)
IMUs are fundamental to aerospace systems, providing crucial data on orientation, velocity, and gravitational forces. Our IMUs feature high accuracy, low noise, and robust construction, making them ideal for navigation, guidance, and stabilization in aircraft, satellites, and unmanned aerial vehicles (UAVs).
-
High accuracy and precisionAlthen's sensors are engineered to deliver exceptional levels of accuracy and precision, meeting the stringent requirements of aerospace applications where reliability is paramount.
-
Rugged constructionOur sensors are designed with durability in mind, featuring rugged construction and robust materials that can withstand the extreme conditions encountered in aerospace environments, including temperature variations, vibration, shock, and radiation.
-
Customization capabilitiesAlthen offers customization options to tailor sensors to the specific needs of aerospace customers, ensuring optimal performance and compatibility with their unique applications and requirements.
-
Comprehensive testingOur sensors undergo rigorous testing and certification processes to ensure compliance with industry standards and regulations, providing aerospace customers with confidence in the reliability and performance of our products.
Typical aerospace sensor categories
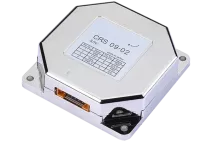
High precision gyroscopes
- Measuring range ±75°/s to ±900°/s
- Excellent accuracy and non-linearity
- Ideal for for aerospace applications
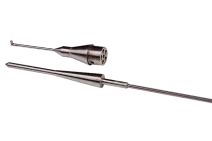
Aeroprobe
- Miro air data computer
- Probes and multi-hole probes
- Various shapes, sizes and geometries
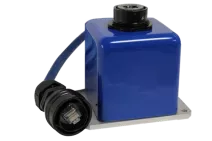
Servo inclinometers
- Measuring range from ±1.0° to ±90.0°
- High accuracy & resolution and low noise
- Robust & sensitive sensing technology
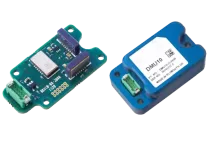
Inertial systems (IMU)
- Measuring range ±75°/s to ±24,000°/s
- Acceleration range ±2 g to ±6.000 g
- Six-degrees-of-freedom (6-DOF) IMU's
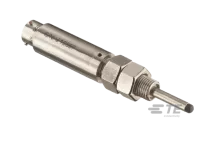
LVDT sensors
- Measuring range 0.13 mm to 508 mm
- Excellent linearity & infinite resolution
- High durability and reliability
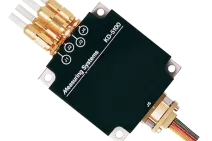
Eddy current sensors
- Measuring range 0,25 mm to 60 mm
- Non-contacting measurement technology
- Perfect for harsh environment application
Advanced technology, responsive customer support
Althen continuously invests in research and development to incorporate the latest advancements in sensor technology, offering aerospace customers access to state-of-the-art sensors with advanced features and capabilities. We pride ourselves on providing responsive customer support, offering technical expertise, troubleshooting assistance, and personalized service to aerospace customers throughout the sensor selection, integration, and lifecycle management processes.
Choosing the right sensor
Selecting the right sensor for aerospace applications is a critical decision that requires careful consideration of various factors to ensure optimal performance, reliability, and safety. When choosing a sensor for aerospace use, engineers should take into account the following key considerations:
- Accuracy and precision: Aerospace systems demand high levels of accuracy and precision to ensure reliable operation. Select sensors with proven accuracy and low measurement uncertainty to meet stringent performance requirements.
- Reliability and durability: Aerospace environments can be harsh, with exposure to extreme temperatures, vibration, shock, and radiation. Choose sensors that are ruggedly constructed and engineered to withstand these conditions, minimizing the risk of failure and ensuring long-term reliability.
- Temperature and pressure ratings: Evaluate sensors based on their temperature and pressure ratings to ensure compatibility with the operating conditions of the aerospace system. Select sensors capable of operating within the specified temperature range and pressure levels without compromising performance.
- Size, Weight, and Power (SWaP): Space and weight constraints are critical considerations in aerospace design. Opt for sensors that are compact, lightweight, and energy-efficient to minimize impact on overall system size, weight, and power consumption.
- Response time and frequency range: Consider the sensor's response time and frequency range to ensure timely and accurate data acquisition, especially in dynamic aerospace environments. Choose sensors with fast response times and broad frequency ranges to capture transient events and high-frequency phenomena.
- Calibration and maintenance: Regular calibration and maintenance are essential to ensure sensor accuracy and reliability over time. Select sensors that are easy to calibrate and maintain, with accessible calibration procedures and long-term stability.
- Compatibility and integration: Assess the sensor's compatibility with existing aerospace systems and interfaces to facilitate seamless integration and interoperability. Choose sensors with standardized communication protocols and interface options to simplify integration into the overall system architecture.
- Cost and lifecycle considerations: Evaluate the total cost of ownership, including initial procurement costs, maintenance expenses, and lifecycle considerations. Choose sensors that offer the best balance of performance, reliability, and cost-effectiveness over the entire operational lifecycle of the aerospace system.
By carefully considering these factors when selecting sensors for aerospace applications, engineers can ensure the successful integration of sensors into their systems, achieving optimal performance, reliability, and safety in the challenging aerospace environment.
Aerospace projects
Some of our aerospace applications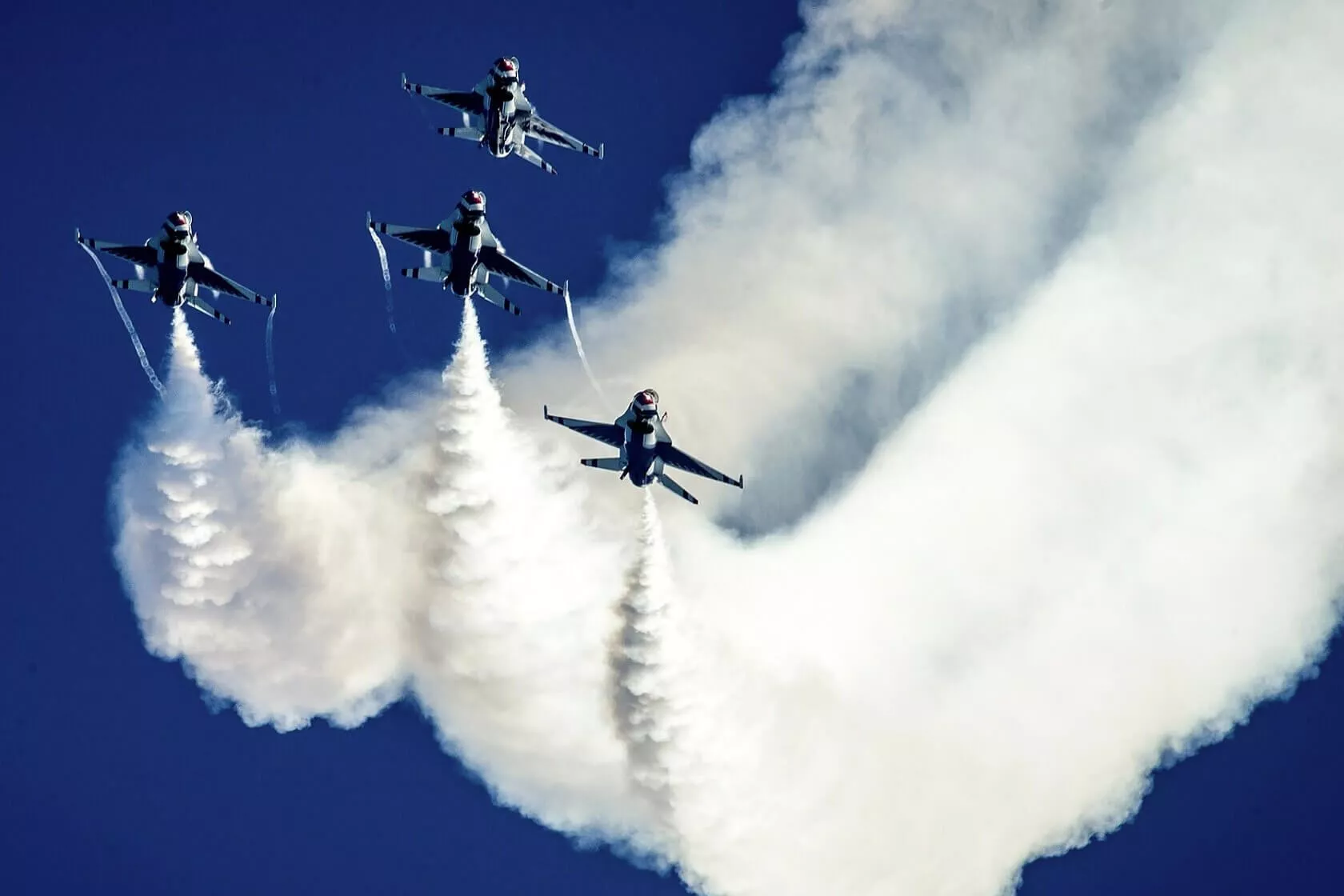
Exciting posibilities
In the realm of aerospace engineering, the future holds exciting possibilities for sensor technology. Advancements in materials science, miniaturization, and data analytics are poised to revolutionize sensor capabilities in aerospace applications. We anticipate the development of sensors with enhanced sensitivity, reduced power consumption, and greater resilience to extreme environments, paving the way for more efficient aircraft designs, autonomous navigation systems, and space exploration missions. Furthermore, the integration of artificial intelligence and machine learning algorithms will enable sensors to adapt and optimize performance in real-time, unlocking new frontiers in aerospace innovation. At Althen Sensors & Controls, we are at the forefront of these transformative developments, continuously exploring new avenues to push the boundaries of sensor technology and propel the aerospace industry towards a future of unparalleled performance and reliability.