Battery test with load cells
The battery is not only the largest and heaviest component in a car but also the most expensive. Comprising multiple battery modules, it can represent up to 40% of an electric car's total cost. Among the various types of batteries, lithium-ion batteries have become the standard for today’s electric vehicles (EVs). They are favored for their compact design, lighter weight, high energy density, and extended lifespan compared to alternatives like solid-state or magnesium-sulfur batteries. Manufacturers often provide warranties on battery capacity, ensuring a certain level of performance for a specified period. To estimate a battery’s lifespan, manufacturers conduct rigorous and extensive testing.Lithium-ion batteries function through a chemical process between the negative electrode (cathode), made of lithium metal oxide, and the positive electrode (anode), composed of graphite. These electrodes are separated by a conductive medium known as the electrolyte. During vehicle operation, lithium atoms migrate from the cathode to the anode, generating an electric current. During charging, lithium ions are stored in the graphite of the anode, causing its volume to expand.
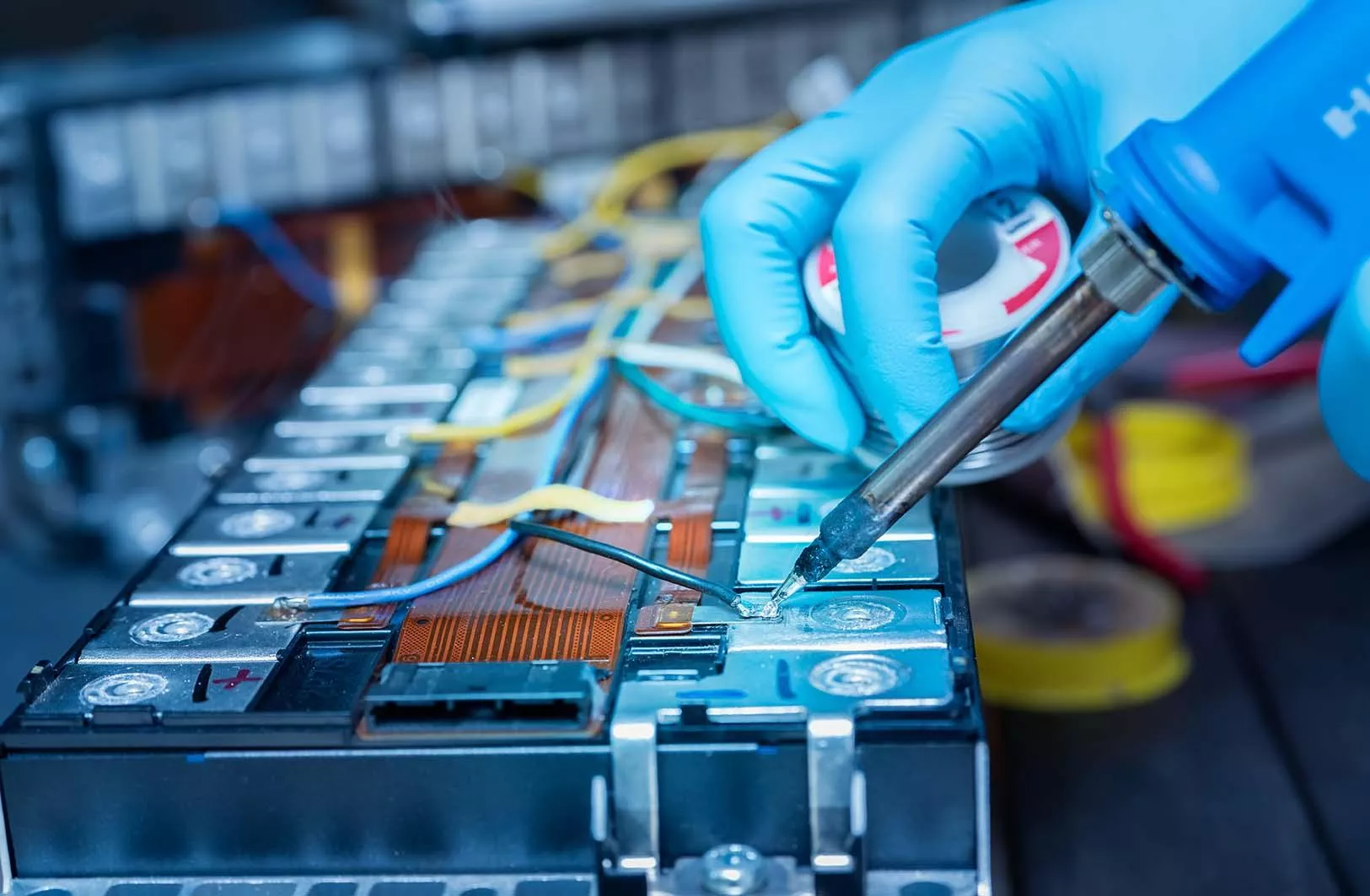
Monitoring cell thickness and force in Lithium-Ion batteries
The expansion of cell thickness caused by charging can typically be reversed during discharge. However, under certain conditions, such as low temperatures or high charging currents, this reversal may not be fully effective due to a phenomenon known as lithium plating. This occurrence not only reduces the lifespan of the battery cells but also elevates safety risks.
To accurately measure the forces acting on the battery during these processes, specialized force transducers are employed. These devices are designed to maintain precision even under challenging environmental conditions. Moreover, they are capable of detecting even the smallest changes in force with high reliability, ensuring accurate measurements throughout extended test durations.
-
Extensive knowledgeMore than 75 years of experience in the measurement and sensor technology sector
-
High-quality sensor solutionsAlways up-to-date: technology and knowledge
-
Customized measurement solutionsTailored to your needs
-
In-house R&D and design departmentIn-house development and production
Product categories
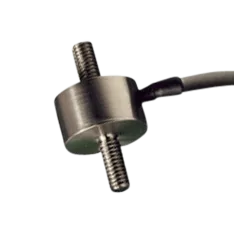
ALF255 Miniature Force Sensor
- Measurement ranges: up to 6.4 kN
- Versions operating up to +250°C possible
- ø30mm x 25mm body
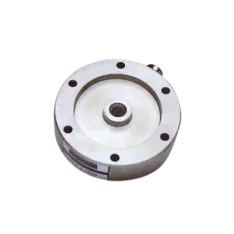
ALF252 Pancake Force Sensor
- Measuring range: ~1 kN to ~10 kN
- Non-lin./hysteresis: 0.1/0.1% RL
- Various designs possible on request
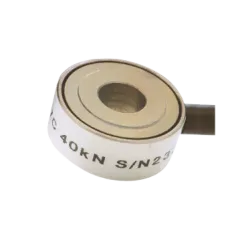
ALF207 Load Washer
- Measuring range: ~10 kN to ~200kN
- For spaces with restricted height
- Various designs possible on request
Crash tests for vehicle safety
Modern vehicles are equipped with numerous sensors that enhance comfort, environmental efficiency, and, most importantly, the safety of all road users. Among the various tests conducted to ensure vehicle safety, crash tests hold particular significance. These tests simulate real-world scenarios to evaluate a vehicle’s structural integrity and occupant protection systems.
The sensors and measurement systems used in crash testing must meet exceptionally high standards. They are required to endure extreme forces during physical tests conducted in controlled environments and to process vast amounts of data during computer simulations. These rigorous demands ensure accurate results and help manufacturers design safer vehicles for the road.
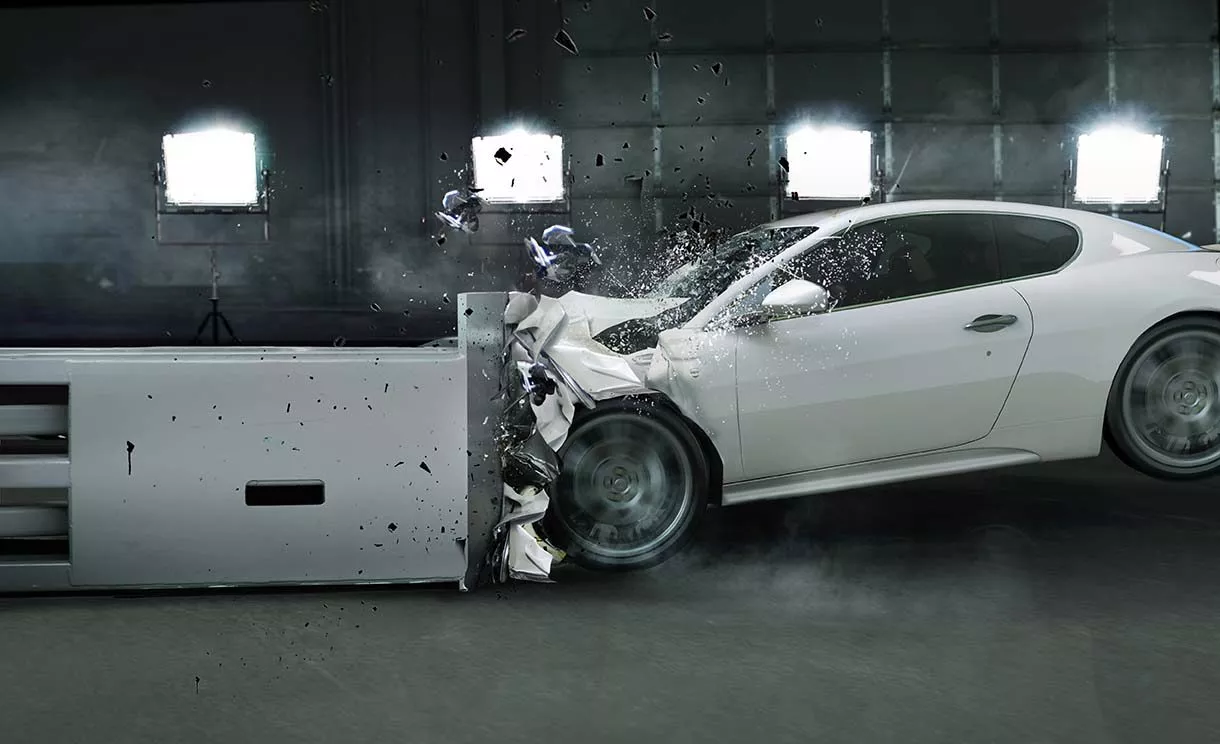
Battery crash testing
The lithium-ion battery serves as the central power source for electric vehicles, but its positioning differs significantly from the fuel tank in conventional cars. Typically housed beneath the passenger compartment for added protection, the battery is particularly vulnerable during collisions.
When subjected to external forces during a crash, a charged battery can experience a short circuit. This may trigger a chemical reaction that, in the presence of oxygen, can ignite and lead to a fire. To mitigate these risks, batteries are designed with reinforced housing and placed in carefully selected locations within the vehicle.
Comprehensive testing ensures battery safety under collision scenarios. Specialized test benches measure parameters such as distance, power, voltage, and temperature, while full-scale crash tests are conducted in dedicated facilities. For example, Mercedes-Benz performs approximately 900 such tests annually (Autosport, Luca Leicht, March 19, 2022).
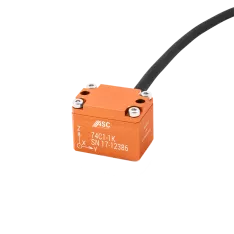
ASC 74C1 Piezoresistive Accelerometer
- Aluminium Housing
- Made in Germany
- Range: 500g, 1000g and 2000g
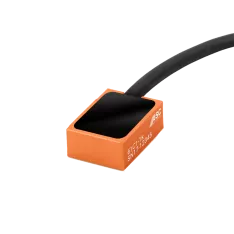
ASC 61C1 Piezoresistive accelerometer
- High shock resistance up to ±5000g
- Compact, low-mass aluminium housing
- Gas damped with DC response
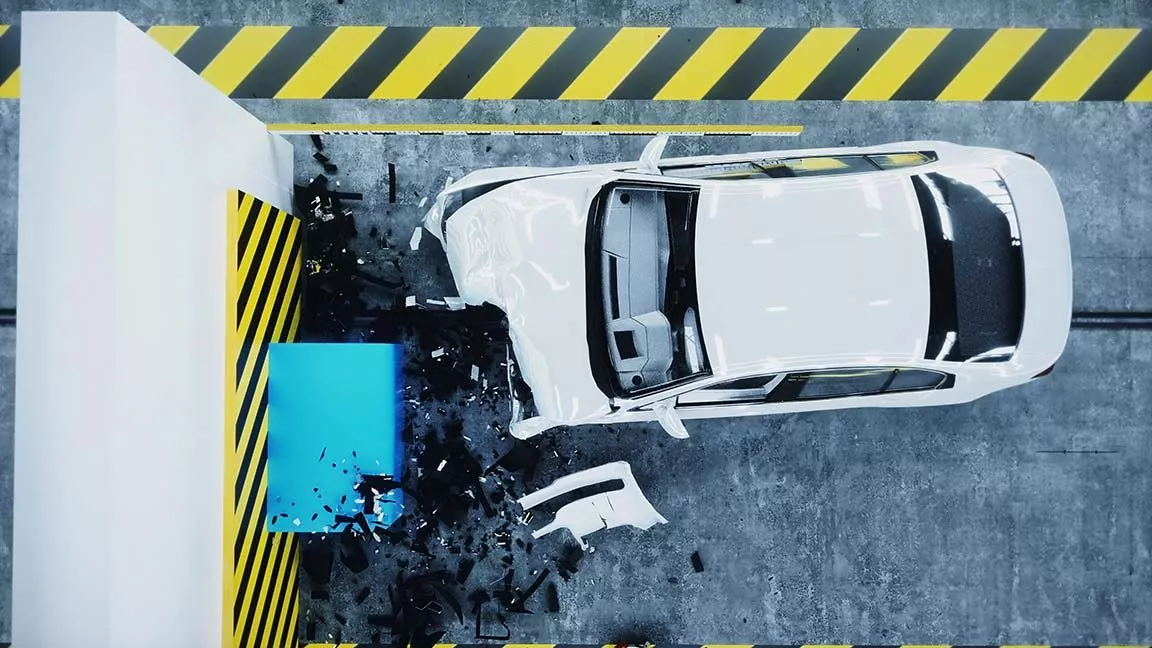
Crash test vehicles: Safety through real-world simulations
Crash tests play a crucial role in evaluating the risks associated with vehicle accidents. While computer simulations provide valuable insights, real-world crash tests remain indispensable. These tests involve specialized force sensors placed both in the vehicle and in crash test dummies, which are meticulously designed to replicate various occupant types.
Modern crash test dummies are equipped with up to 220 measurement points, enabling detailed analysis of biomechanical loads experienced by occupants during a collision. Data collected from these physical tests is compared with computer simulation results to validate their accuracy and reliability.
The outcomes of these tests offer critical insights into occupant protection, vehicle structural weaknesses, and the performance of advanced safety and assistance systems. This comprehensive approach ensures that vehicles meet stringent safety standards before they reach the roads.
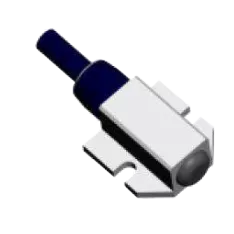
EGAS-S398C Shock Testing Accelerometer
- Standard <10mV ZMO
- Linearity <1%
- Transverse Sensitivity <1%
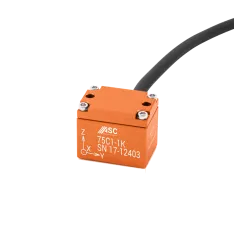
ASC 75C1 Piezoresistive Accelerometer
- Range: 500g, 1000g and 2000g
- Small Size
- Light Weight
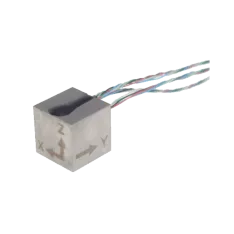
EGAXT3 Mini Critically Damped Triaxial Accelerometer
- Miniature Triaxial, Low Weight
- Static and Dynamic Measurement
- Frequency Response from DC to 3000 Hz
Sensors for navigation in autonomous vehicles
Self-driving cars aim to make roads safer and more efficient, and navigation systems are at the core of their operation. Among these, Inertial Measurement Units (IMUs) and Inertial Navigation Systems (INS) play a critical role in ensuring the safety and efficiency of autonomous vehicles. Whether analog or digital, IMUs continuously and precisely track an object’s position and movement, providing highly accurate positioning and enabling seamless navigation.An IMU is a sophisticated module comprising a 3-axis linear accelerometer and a 3-axis gyroscope, together measuring the six degrees of freedom (6 DOF). This configuration captures both linear movements (X, Y, Z) and rotational dynamics (roll, pitch, yaw), allowing it to record every aspect of a vehicle's movement. IMUs are versatile, used not only in systems like airbags and vehicle stability control but also for providing real-time data on a vehicle's full position and orientation.
In the latest generation of Advanced Driver Assistance Systems (ADAS) and autonomous vehicles, highly accurate IMUs are indispensable. They enable precise prediction of a vehicle’s movement and determine its exact position in real time. To further enhance accuracy, IMU data is often integrated with inputs from GPS receivers and image-based sensors, such as lidar and cameras. This combined information allows for continuous and reliable estimation of the vehicle's position, ensuring safe and effective navigation.
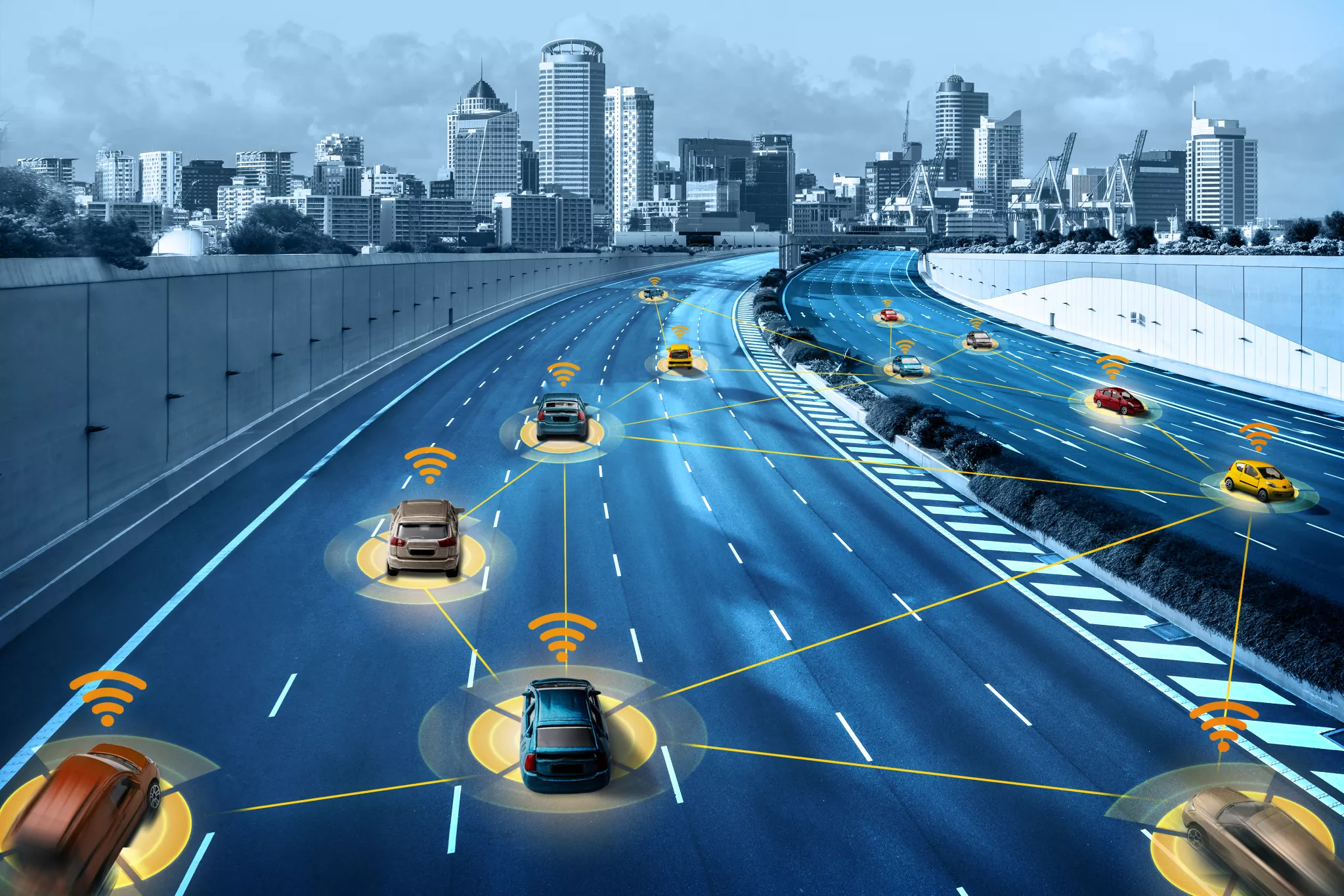
IMUs for navigation of autonomous vehicles
In the latest generation of Advanced Driver Assistance Systems (ADAS) and autonomous vehicles, highly accurate IMUs are indispensable. They enable precise prediction of a vehicle’s movement and determine its exact position in real time. To further enhance accuracy, IMU data is often integrated with inputs from GPS receivers and image-based sensors, such as lidar and cameras. This combined information allows for continuous and reliable estimation of the vehicle's position, ensuring safe and effective navigation.
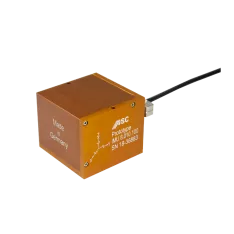
ASC IMU 8.X.Y Inertial Measurement Unit (IMU)
- MEMS Capacitive and Vibrating Ring Technology
- Measurement Range Accelerometers: ±2 to ±30 g
- Measurement Range Gyroscopes: ±10 to ±400 °/s
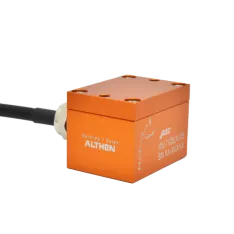
ASC IMU 7.X.Y Inertial Measurement Unit (IMU)
- MEMS Capacitive and Vibrating Ring Technology
- Measurement Range Accelerometers: ±2 to ±50 g
- Measurement Range Gyroscopes: ±75 to ±900 °/s
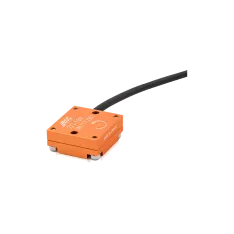
ASC 271 Uniaxial angular rate sensor
- MEMS vibrating ring gyro with high shock resistance
- Angular rate sensor with ±900 °/s range and 0.2 °/√hr ARW
- Designed for navigation, robotics, and mobile platforms
Force transducers for vehicle testing and test benches
Althen offers a series of special force transducers especially for the automotive test sector. On the one hand, high forces need to be measured in hard-to-reach places with little flexible installation space. On the other hand, the quality of gear shifting, shift feel, the force required to depress the clutch or even the strength of the seat belt make an important contribution to the driving experience. There are special measurement solutions for determining objective metrics and thus the subsequent possible adjustment of forces to the desired feel.
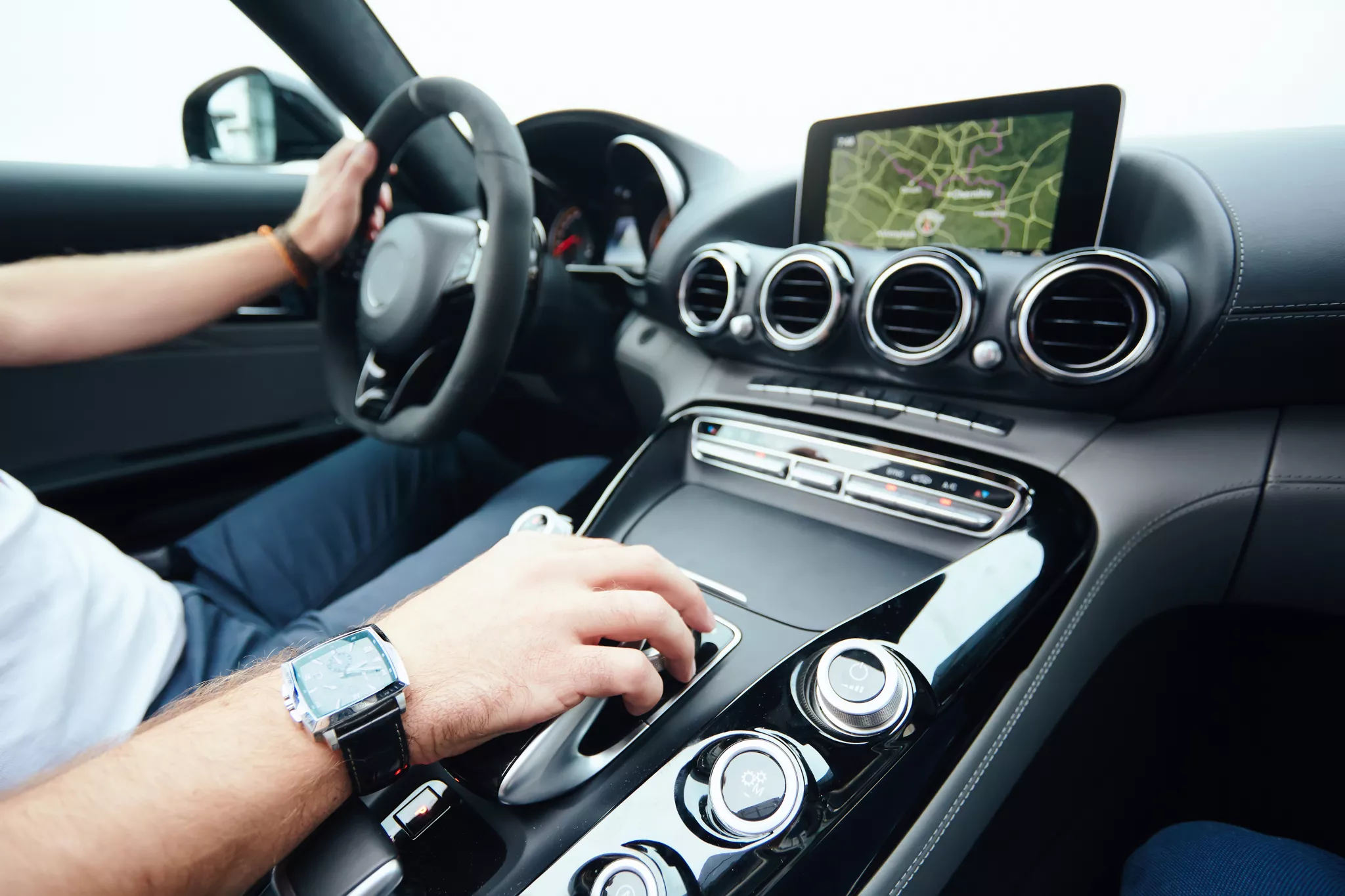
Applications of Force Transducers in Vehicle Testing
Pedal force transducers are essential tools for measuring the forces required to operate the brake, accelerator, and clutch pedals. These measurements provide critical insights into ergonomic factors and the interplay of various muscles involved in generating force. By analyzing these dynamics, manufacturers can optimize pedal design for enhanced user comfort and performance.
Similarly, 3-axis force sensors are used to assess gear lever operation, allowing for early evaluation of shift quality. These sensors provide precise measurements by outputting the force components along three axes as separate signals. Delivered fully calibrated, these force transducers are ready for immediate use in testing environments.
For safety belt testing, specialized force transducers are employed to perform accurate force measurements. Characterized by their low weight and high strength, these sensors are ideal for dynamic applications, such as crash tests, where distortion-free measurements are critical. Their robust design ensures reliable performance under extreme conditions, providing valuable data for the development of safer vehicles.
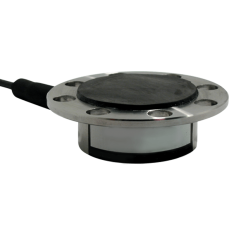
ALF304 Brake Pedal Force Sensor
- Measuring range: 0 to 2,5 kN
- Measures brake pedal application forces
- Allows attachment to any shape pedal
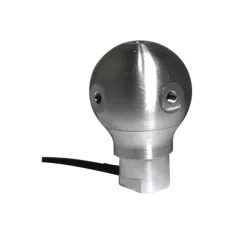
ALF321 Gear Shift Force Sensor
- Measuring range: 0 to 200 N
- Measures gear lever forces for gear selection
- Pure calibrated outputs for each axis
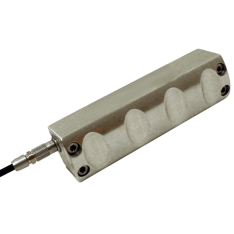
ALF319 Hand Brake Force Sensor
- Measuring range: 0 to 1 kN
- Measurement of an ergonomic force
- Good extraneous load rejection
Why choose Althen?
Althen Sensors & Controls offers high-quality measurement solutions that meet the most stringent requirements of the automotive industry. Whether it's battery testing, crash testing or navigation solutions, we provide the technology you need to excel.
Contact us to learn more about how our sensors can enhance your projects.