Precise control during the lane-switch
Central to achieving this milestone is the integration of Althen's IMU8.x.y inertial measurement unit (IMU), a sensor crucial to the precise control of the hyperloop pod during the lane-switch maneuver.
During the hyperloop pod's lane-switch, controlling and stabilizing the pod is paramount. The lane-switch involves navigating a section of the track where the pod must maintain levitation and correct orientation while crossing lateral and vertical beams. The regular optical localization system typically used in the pod loses effectiveness in this area, presenting a challenge in maintaining the pod's stability and control.
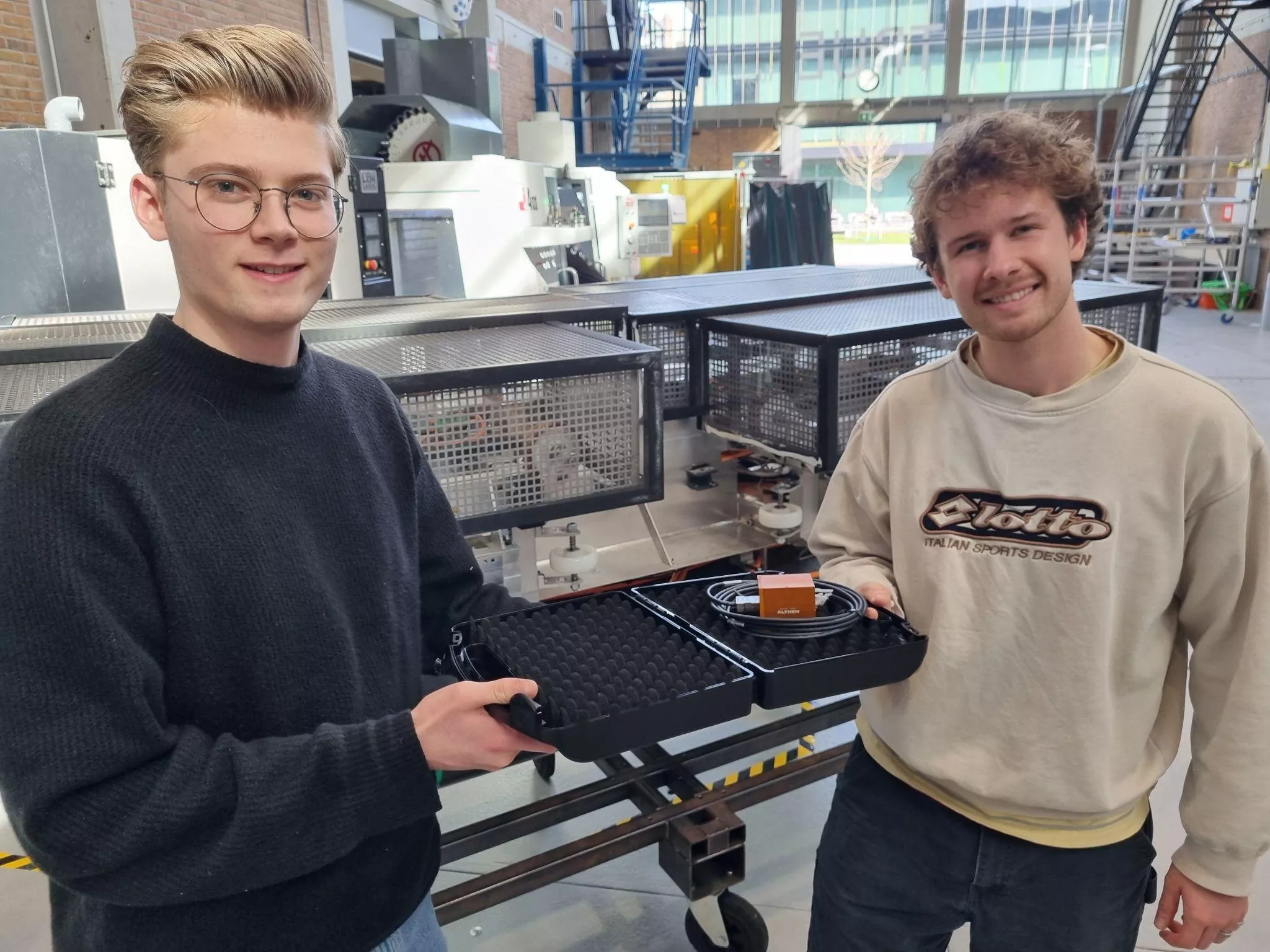
About the ASC IMU 8.X.Y
The ASC IMU 8.X.Y is a highly precise inertial measurement unit (IMU) built on MEMS accelerometers and gyroscopes. It offers 6 degrees of freedom, excellent bias stability, and features both low noise and high shock resistance. Its modular design supports various applications, including automated guided vehicles, robotics, and railway systems. With its lightweight, IP65-rated aluminum housing, and customizable cable options, it provides reliable performance in harsh conditions, making it ideal for projects requiring precise positioning and navigation.
A key to success
In maintaining the pod's stability and control, Delft Hyperloop turned to Althen and ASC for the IMU8.x.y, a highly accurate inertial measurement unit. The IMU was integrated to fulfill multiple critical roles during the lane-switch:
Precise pod localization
The optical localization system loses track of the pod during the beam-crossing segment, requiring the IMU to estimate the pod's position with an accuracy of up to 5 cm for up to 10 seconds. This ensures the pod remains on course during this pivotal moment of the switch.
Monitoring pod orientation
The IMU detects and measures even the smallest changes in the pitch, yaw, and roll of the pod. These measurements are crucial for maintaining stability in relation to the beams, ensuring the pod continues to levitate smoothly and without unexpected deviations.
Force estimation for damping oscillations
The IMU plays a key role in estimating the vertical force exerted by the pod’s magnetic motor, enabling the team to dampen any unwanted oscillations that might arise during the lane-switch. This is essential for maintaining a steady levitation and avoiding disruptions.
Centrifugal force estimation
Through precise measurements of centrifugal force, the IMU helps determine the optimal current to be used during the turn, ensuring that the pod navigates the lane-switch safely and efficiently.
The integration of the IMU did significantly improve the pod’s performance in managing lateral electromagnetic suspension (EMS) forces, which were influenced by multiple complex factors. The quick response of the IMU allowed us to refine our control systems and prepare for the challenging lane-switch maneuver.
Signal processing and control system integration
The IMU’s output signals are split into two channels for different processing needs:
- EtherCAT messaging for motor drives: The IMU’s signals are converted using an IO-block into an EtherCAT message and sent directly to the levitation motor drives. These signals provide real-time data for controlling the pod’s position (pitch, yaw, and roll) as well as the damping and adjustment of vertical and lateral forces.
- Teensy 4.1 ADC for location tracking: The second signal output is converted into a 0V-3.3V differential signal that is fed into a Teensy 4.1 microcontroller. By using the pod’s final velocity going into the lane-switch, the IMU data helps iteratively calculate the pod’s location throughout the turn. This second channel is still under development and testing.
- Advanced filtering with Kalman integration: To ensure accurate data, the IMU signals are processed through a complementary filter and incorporated into an extended Kalman filter (EKF), enhancing the performance of the pod’s control systems. The EKF helps mitigate external disturbances, such as forces from the motor, and allows for faster rejection of these disturbances compared to the traditional PID control loops. The high sensitivity of the IMU (e.g., static noise levels of 150 µrad/s for gyros) allows the system to respond quickly and precisely to any variations in pod behavior.
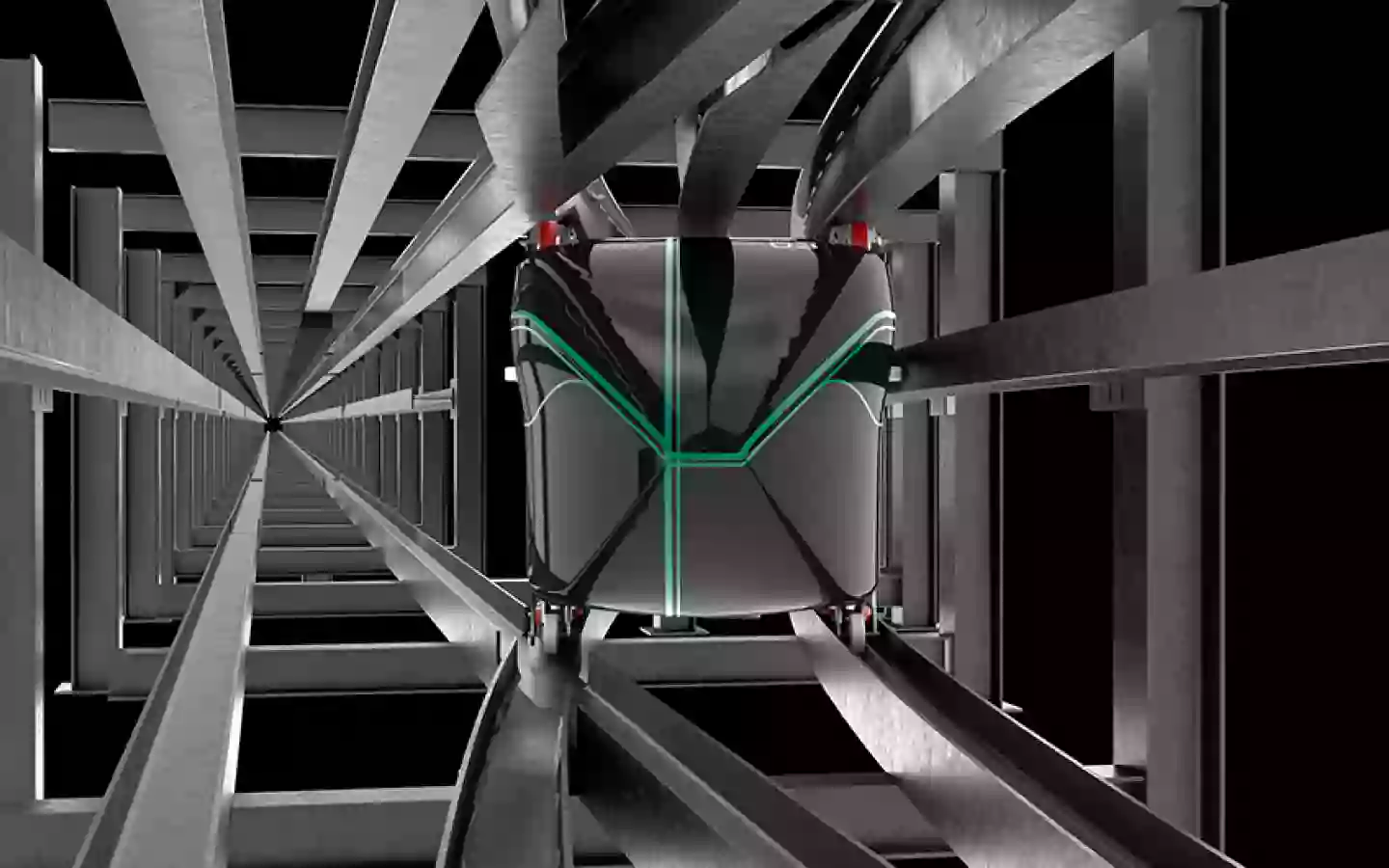
Accept the marketing cookies to view this video.
Click here to change your consent.
Performance results: enhanced stability and control
The integration of Althen’s IMU did significantly improve the pod’s performance in managing lateral electromagnetic suspension (EMS) forces, which were influenced by multiple complex factors. The quick response of the IMU allowed the Delft Hyperloop team to refine their control systems and prepare for the challenging lane-switch maneuver.
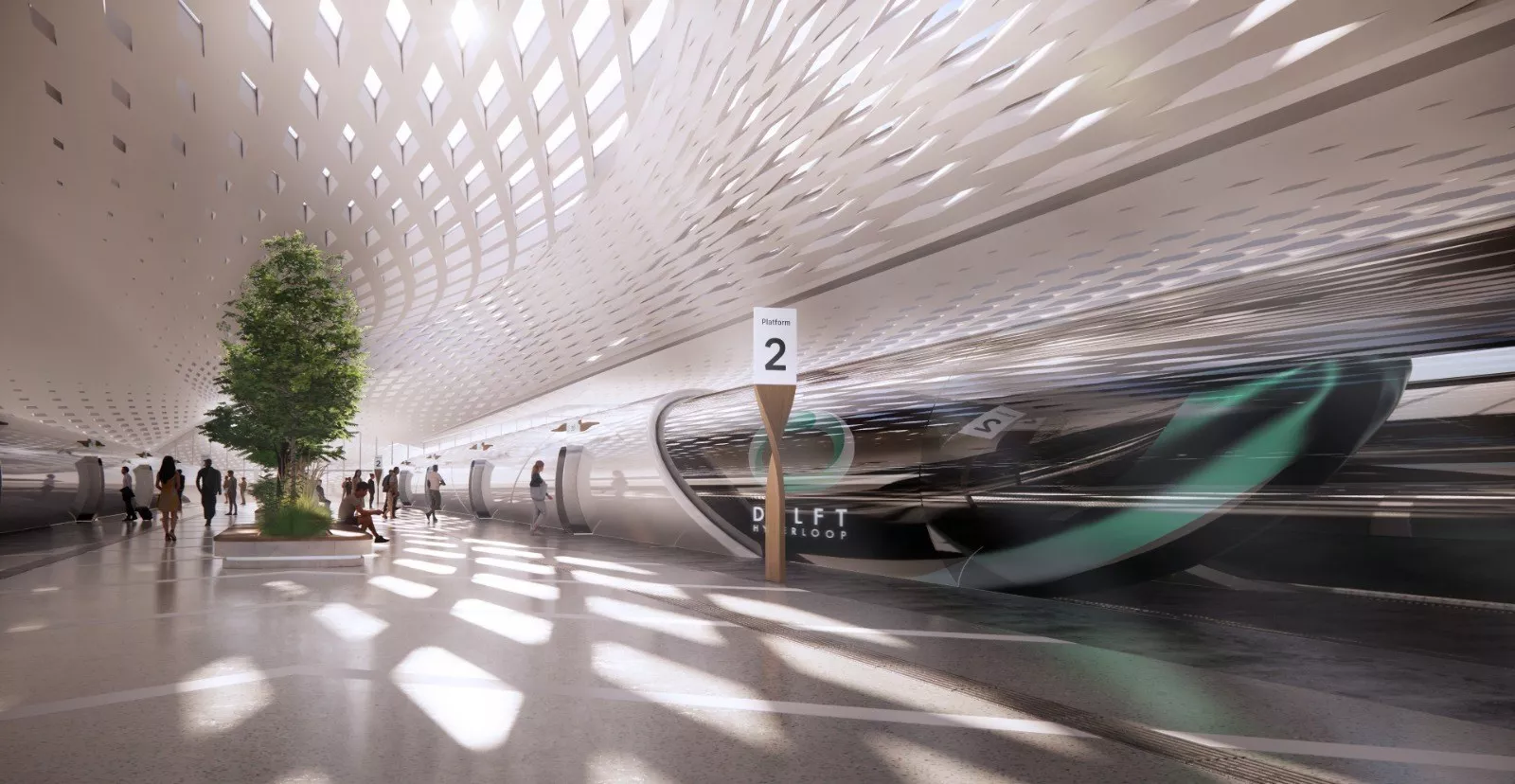
Support and timely integration
The rapid support and communication provided by Althen have been invaluable to the Delft Hyperloop team. With tight deadlines for European Hyperloop Week, the timely integration of the IMU was critical. The partnership allowed the team to implement, test, and fine-tune the sensor just in time for the competition, greatly increasing their chances of successfully achieving the first-ever levitating lane-switch in a hyperloop pod.
An indispensable component
The IMU8.x.y has become an indispensable component of the Delft Hyperloop’s lane-switch system, providing the sensory data needed to precisely control the pod’s location, orientation, and forces during this complex maneuver. The IMU has played a vital role in pushing the boundaries of what’s possible in the future of transportation.
To learn more about how Althen together with ASC can provide tailored inertial measurement solutions for your projects, or to discuss your specific application needs, contact our team today. We're here to help you find the perfect sensor solution for your challenges.
Ideas or questions
We are curious about your project and measurement challenge
Do you need a customized sensor for your project or application? Please get in touch with us.