Pressure patch technology
There can be hundreds of pressure tappings on today’s Formula 1 cars, such is their need for detailed aerodynamic analysis of these ever-more complex cars. Each tapping is a drilled and an accurate “tubulation”, a tiny pressure tube, which is fitted into the bodywork. These are connected to short tube runs that feed aero pressure to the pressure scanners. But what if you wanted to measure the surface pressure of a part without drilling holes into it? Scanivalve Corporation have developed pressure patch technology which achieves exactly that.
Use of pressure patches
These Scanivalve pressure patches are small, flat, Aluminium discs, with a port in the centre for pressure measurement, and a small tubulation that connects the disc via tubing to a pressure scanner. These are attached to the surface on-vehicle temporarily, and at less than 20mm wide and c.2mm tall, the influence of these devices on the aerodynamics is negligible. These are taped to the surfaces and removed afterwards.
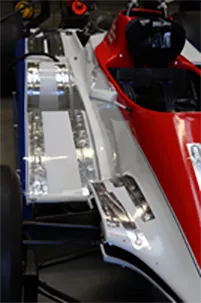
The pressure patches can be seen here on the surface of the body, with the associated cables for the pressure scanners. The small size and shape of the pressure patches have minimal impact on aerodynamics.
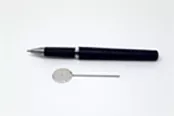
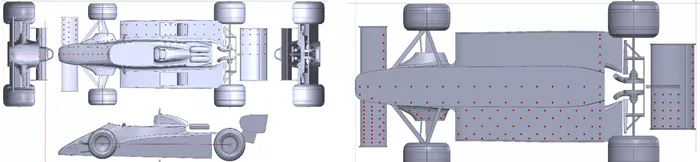
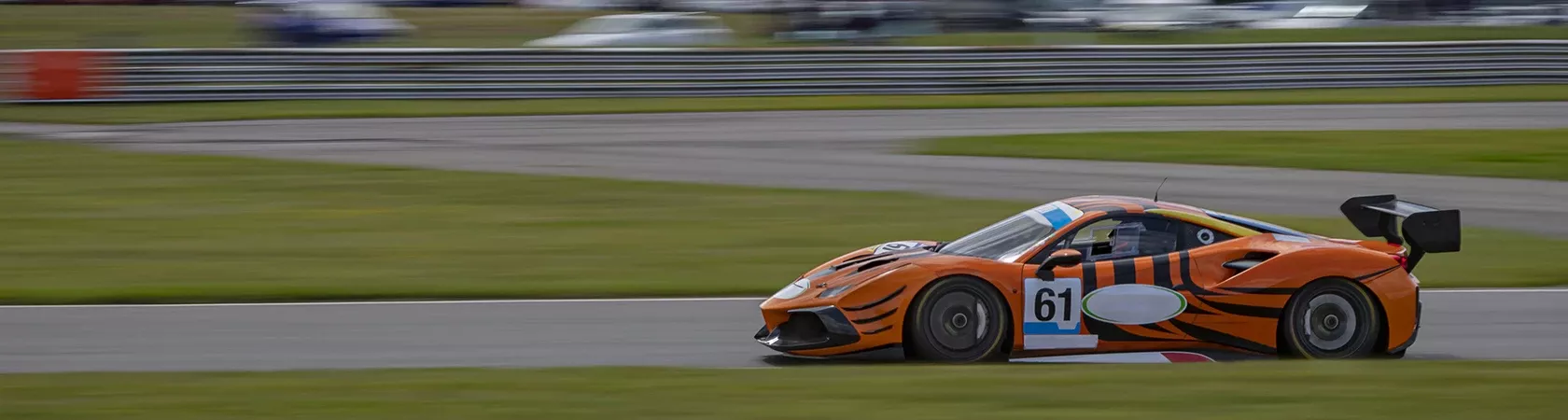
Attach patches directly to the surface
‘Commonly, holes are drilled into a wing to make tappings for surface pressure measurements, but the big advantage with these pressure patches is that you can attach them directly to the surface without permanent installation and drillings,’ explains Iain Gordon, Export Sales Manager at Evolution Measurement. ‘If you wanted to analyse the aerodynamics of a piece of body work on-car, a rear windscreen or for a temporary installation, permanently drilled holes may not be desirable, or even possible, and that’s where Scanivalve’s pressure patches are so useful.’
Like Formula 1 teams
A good example of the use of these pressure patches is on an historic F1 race car, where drilling or modifying the bodywork and aero surfaces simply wasn’t allowed. Dr. Bob Fernley, former Deputy Team Principal at Force India, has facilitated a project at the University of Bolton, where students measure, analyse and optimise the aerodynamics of his historic Ensign 180B ground effects Formula 1 car. Scanivalve Pressure patches, instead of traditional pressure tappings, were applied to various surfaces of the car, on the upper bodywork, the front and rear wings and on the venturi/diffuser/floor with several pressure scanners, providing 256 channels of live, real-time digital Aero pressure data. Therefore, not only have the students been experiencing pressure scanners, but also now have experience with this new pressure patch technology in the same way Formula 1 teams do.
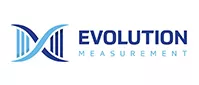