Why pressure sensors are important for ballast water
Ballast water is used to improve the draught, stability and strength of an ocean-going vessel when it is not (fully) loaded. About 10 billion tonnes of ballast water are transported around the world every year. However, the water can contain thousands of aquatic microbes, plants and animals, which are transported across the globe during the voyage and end up in a new environment at the ship's destination when the water is discharged. This can lead to potential harm to species and organisms at that local location. Special, resistant pressure sensors help to properly purify ships' ballast water.
Damage and regulations for ballast water management
Chinese crabs, which accelerate erosion in the Thames. Bulgarian mussels, which clog the water intakes of power stations in the US. The spread of invasive species is a global problem. In terms of increased maintenance, destruction of fish stock, clogging of industrial inlets, erosion and other problems, the annual cost is €12 billion a year in Europe alone. In 2019, the International Maritime Organisation (IMO) enacted regulations for ballast water management. The Ballast Water Treatment Systems Convention (BWTS) prescribes the proper control and disposal of ballast water from ships. This is to ensure that proper treatment and procedures are used to minimize water pollution and prevent the introduction of harmful organisms plus pathogens into new ecosystems. This process includes filtration and electro-chlorination of seawater before it is discharged back into the ocean. Very special pressure sensors are used to monitor and control the ballast water treatment and filtration systems.
Special pressure sensors are used for thorough monitoring and control of the ballast water treatment and filter systems
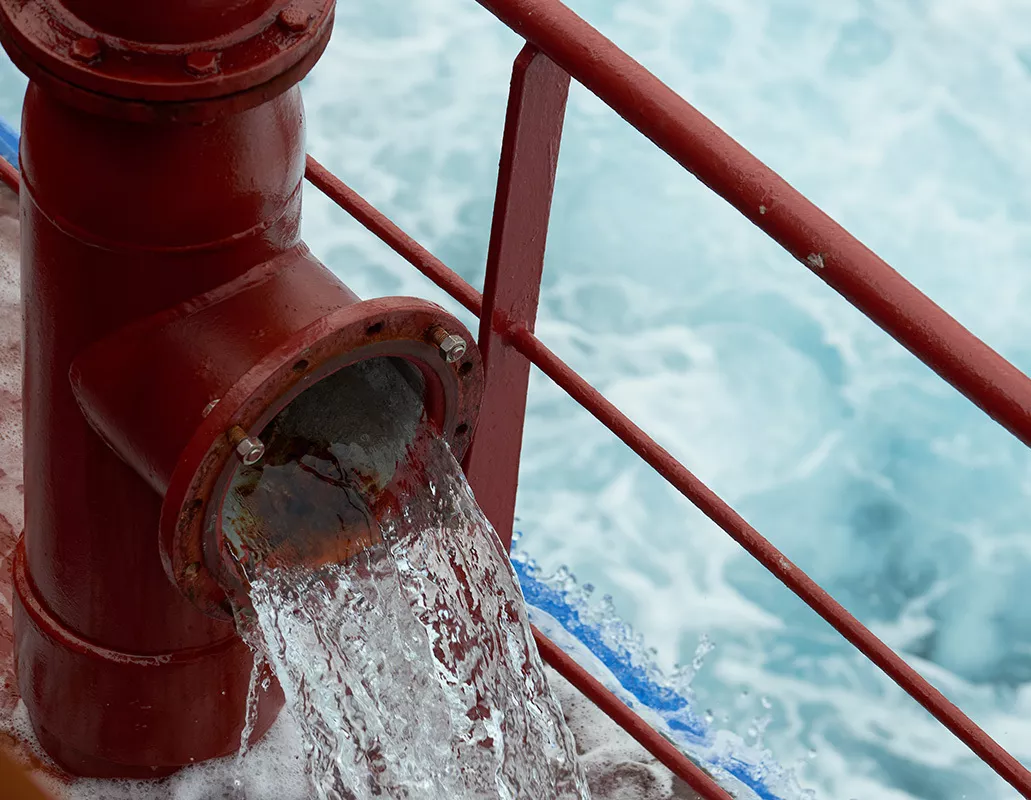
Ballast water circuit
Most ballast water treatment systems use a two-stage approach with some form of mechanical separation (first stage). This is followed by physical or chemical treatment in the second stage. The two most common technologies are systems based on ultraviolet (UV) and electro-chlorination (EC). UV systems use physical UV radiation as a secondary treatment. Electro-chlorination uses a chemical "agent" to inactivate biological organisms. Both systems usually use filtration as the primary treatment process.
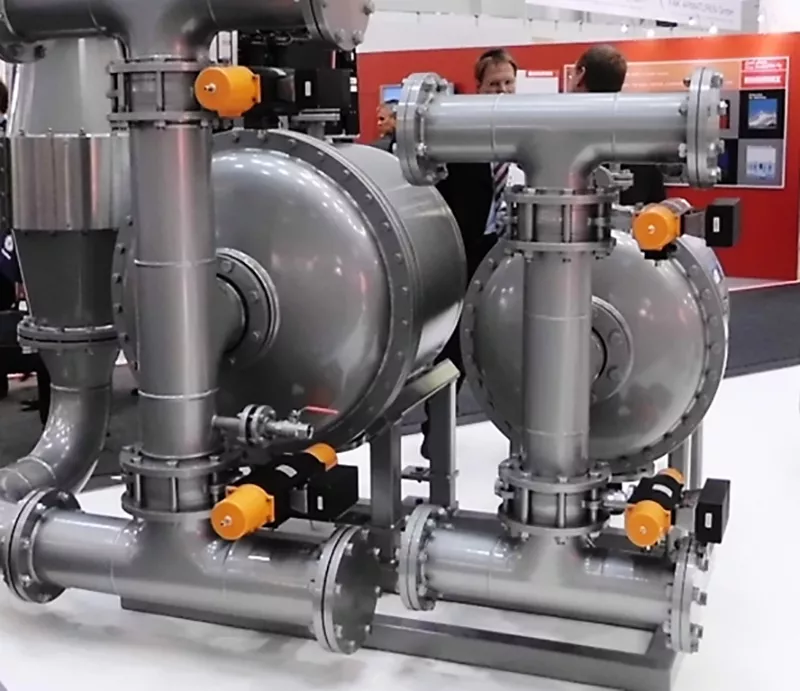
The AGS4200 pressure transmitter
The AGS4200 is also ideal for measuring the dosing pressure of the chemical additives used to treat the water in the system. These additives include sodium hypochlorite - a combination of sea water, chlorinated water, oxygen and hydrogen. The AGS4200 offers perfect resistance to corrosion. Due to its titanium and sapphire construction, the pressure transducer can be used at medium temperatures of up to 125 °C (at ambient temperatures of up to +85 °C). The sensors are equipped with integrated electronics and offer high over pressure resistance. The sensors are available for measuring ranges from 0 ... 500 mbar to 0 ... 1,500 bar and have an accuracy of ±0.25% (optionally ±0.1%).
Related products
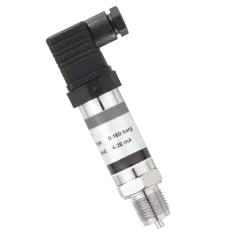
APR3100 High-Precision Pressure Transducer
- Pressure range: 0-2.5 bar to 0-1,000 bar
- Reliable pressure measurement
- Long service life
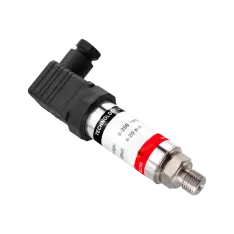
AGS4200H Hydrogen Compatible Pressure Transducer
- Compatible for use within Hydrogen based environment
- Measuring range: 0 - 0,5 to 0 - 1.500 bar
- ± 0.25% accuracy, optional ± 0.1%
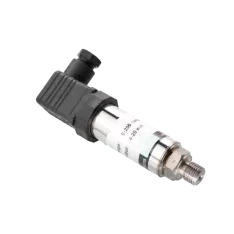
AGS4200 Standard Pressure Transducer
- Measuring range: 0 - 0,5 to 0 - 1.500 bar
- Silicon-on-Sapphire sensor technology
- ± 0.25% accuracy, optional ± 0.1%