Hydro-Motion's boat
The boat is designed with hydrogen propulsion. The boat must also be able to "fly" across the water, so to speak, using two L-shaped and one T-shaped wing under the boat. For the boat to function optimally, the position of these wings must be constantly adjusted. To do this, a tow-wire sensor is used, which is connected to a control plate that measures the steering angle. This angle is used to determine the differential rise.
Draw-wire sensors
Draw-wire sensors (also called pull-wire potentiometers) can measure distances with an accuracy of up to 0.01 mm. They detect the position and movement of an object using a flexible steel cable pulled from a spring-loaded coil. Linear movement at the end of the cable is thus converted into rotational movement..
About the TU Delft Solar Boat Team
The TU Delft Solar Boat Team is a project team of TU Delft and consists of ambitious students from different departments. Each year, the students design and build a fully functional boat together to compete against other universities. While last year the team focused on solar-powered boats, the focus for 2021 was on hydrogen propulsion (Hydro-Motion Boat).
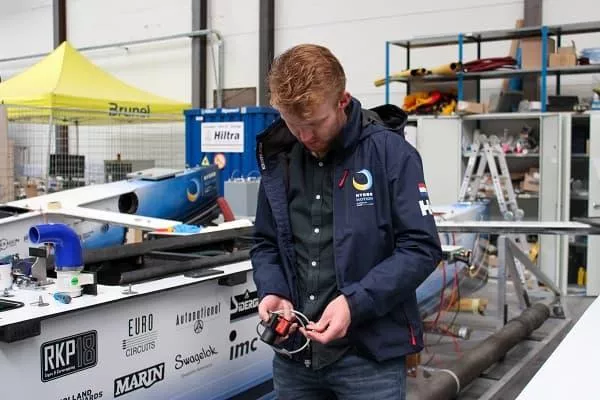
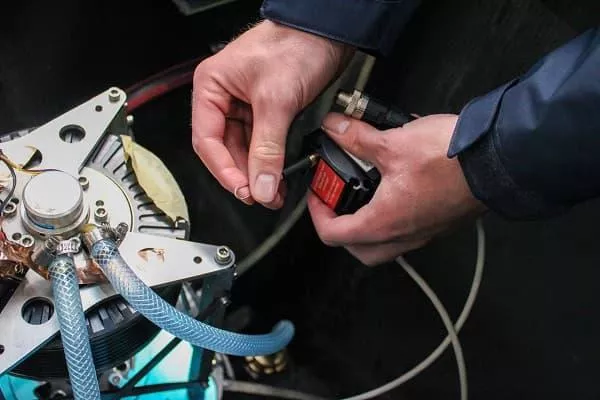
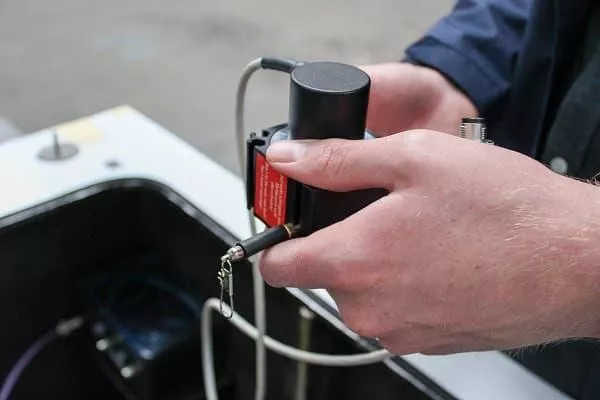
Althen ist stolz darauf, dieAlthen is proud to support this project for the sustainable development of the maritime industry.
"Flying" with a hydrogen-powered boat
Project manager Bouwe Theijse explains how the system works: "Just like an aeroplane, we need sufficient speed to generate lift. At 22 kilometres per hour, our take-off speed, we are fast enough. From then on, our wings, the hydrofoils, will push the boat out of the water and the entire 1,100-kilogram vehicle will fly above the water!" The team designed the hydrofoils to support the entire weight of the large boat. The larger and heavier boat was needed because the 2021 Energy Boat Challenge will be held in Monaco in the Open Sea Class.
When the hydrogen boat "flies" over the water, it manoeuvres using a differential tilt of the front wings. This principle can be thought of as a motorbike that has to tilt sideways in order to turn. The position of the wings must be adjusted for the boat to function optimally. To do this, a cable sensor is used, which is connected to a control plate that measures the steering angle. This angle is then used to determine the differential tilt.
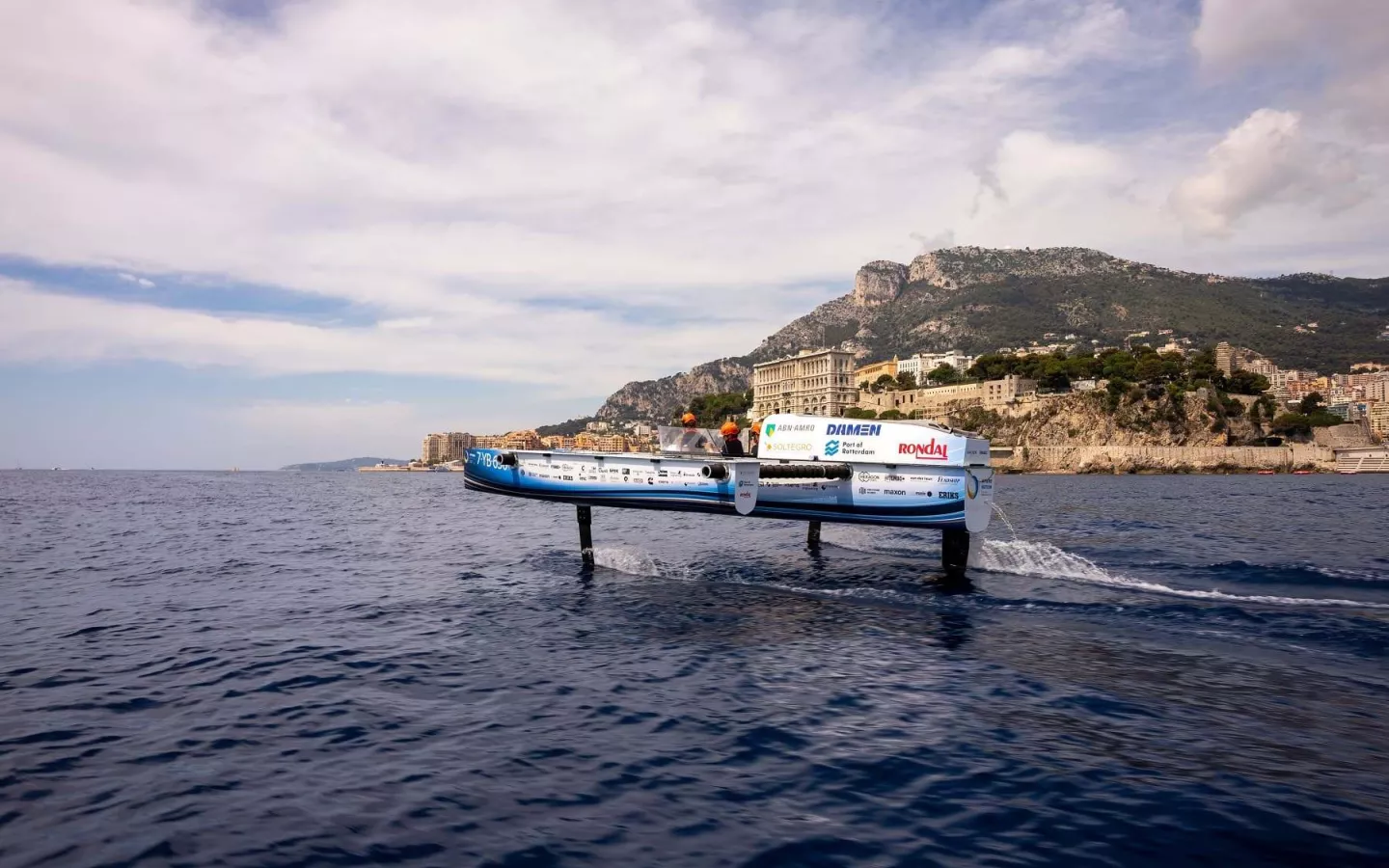
Accept the marketing cookies to view this video.
Click here to change your consent.
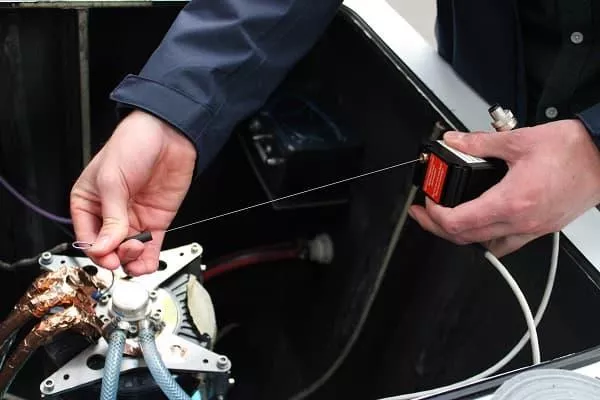
A cable for the steering calculations
Together with the engineers from Althen, the team from TU Delft selected the FD60-500-SR-P draw-wire sensor for this application. The draw wire has a draw length of 500 mm and a potentiometric output.
The sensor is mounted on the stern of the boat. The clip of the cable pull is attached to the other end of the steering plate. The value of the sensor is read by the EMS, the control board on board the boat. The clip of the pull wire is connected to a point that does not move linearly in one direction. For this reason, simple mathematical calculations are used to convert the sensor's readings into the corresponding steering angle. In this way, the steering angle is calculated very accurately and hardly fluctuates.
Althen is proud to be able to support this project for the sustainable development of the maritime industry.
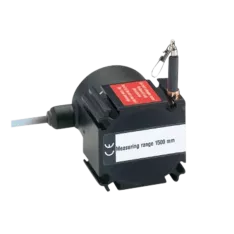
FD60 Series Draw-Wire Sensors (String Pot)
- Measuring range: 100 mm to 1500 mm
- Customized versions for OEM
- Easy and flexible mounting
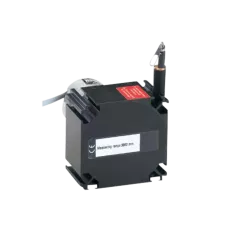
FD96 Series Draw-Wire Sensors (String Pot)
- Measuring range: up to 2.000 or 2.500 mm
- Output: potentiometer, current & voltage
- Digital output: HTL/ TTL/ PB/ CO/ SSI
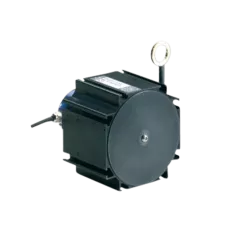
FD115 Series Draw-Wire Sensors (String Pot)
- Measuring ranges: 3.000 mm to 15.000 mm
- Robust aluminium profile housing
- Digital: Incremental/absolute encoder