OEM applications
Over the years we have worked with many OEM's to develop high precision, high speed machines for use in pharmaceutical plants and other applications. An engieneering customer has switched to the latest range of torque sensors. The new TorqSense Digital rotary strain gauge series SGR 530/540 measures torque using a full four element strain gauge bridge. With this four separate strain gauges are fixed to the drive shaft of the plant or machinery being monitored. The gauges are aligned so that each measures shaft deflection in a different direction as it rotates under load. Electronics within the sensor collects readings from all four gauges and uses them to calculate the torque value in real time.
Torque sensor for pharmaceutical bottle caps
Strict international rules apply to the manufacturing and packaging of pharmaceutical products and require that the correct environment is maintained within the bottle or other packaging following capping. To this end, Regulation USP 671 provides a guide to the torque range to be used for screw type containers with varying closure diameters. By ensuring that bottle caps are successfully applied to the bottles within the required torque tolerances, the integrity of the product can be maintained.
The heart of the bottle capping machines
The TorqSense transducers are at the core of the bottle sealing machines. These capping machines not only tighten bottle caps within precisely defined tolerance, but also log every detail of every bottle that is capped. Every cap has to be done up to the same torque, and proof of this performance is required. The machine had to run the torque up to 10kgf.cm within tolerances of 10% recording the actual value achieved. This secures the cap at a level of tightness that will ensure security and sterility, yet can be opened relatively easily by an adult. The logged values are saved using TorqView software to provide a permanent record for traceability.
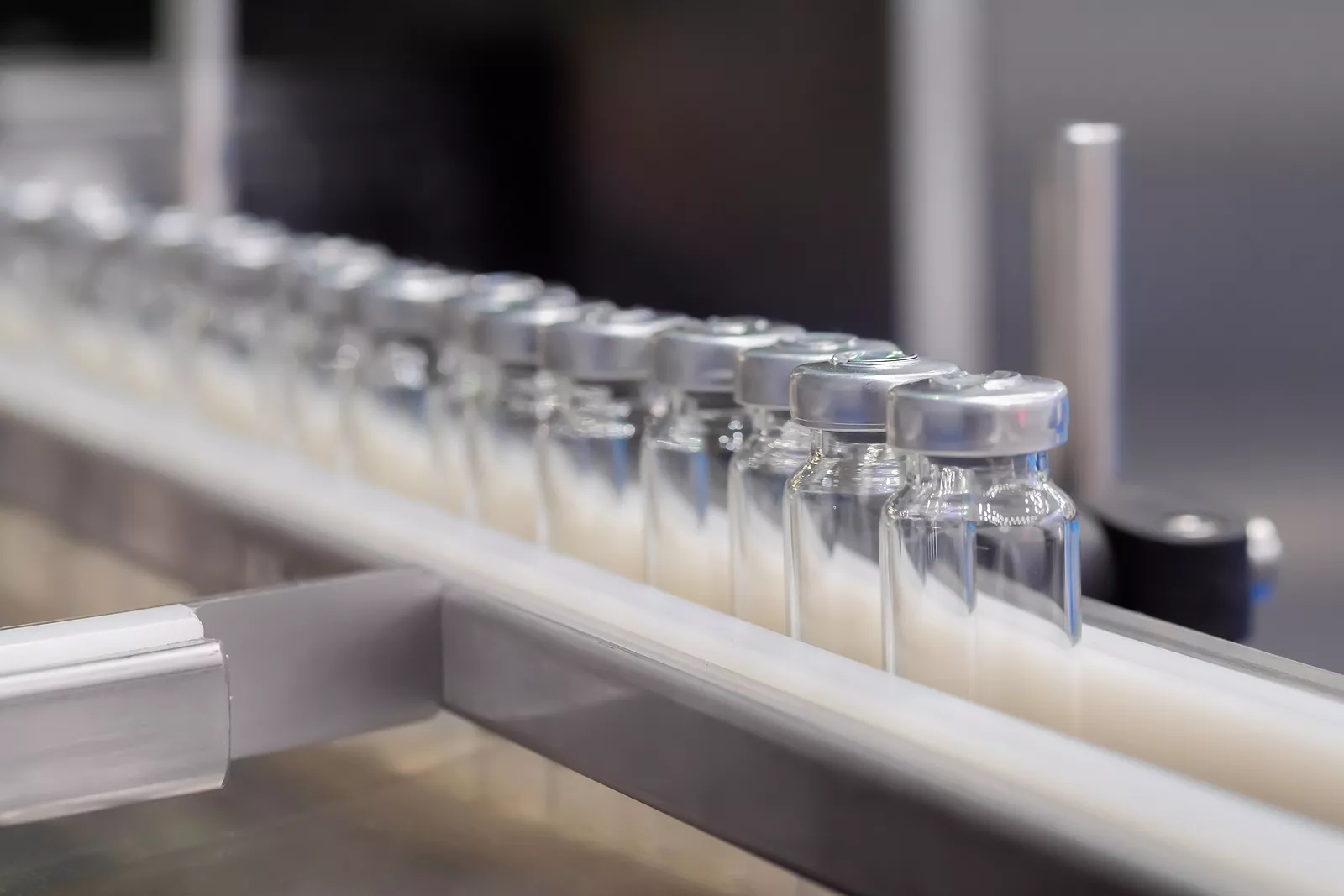
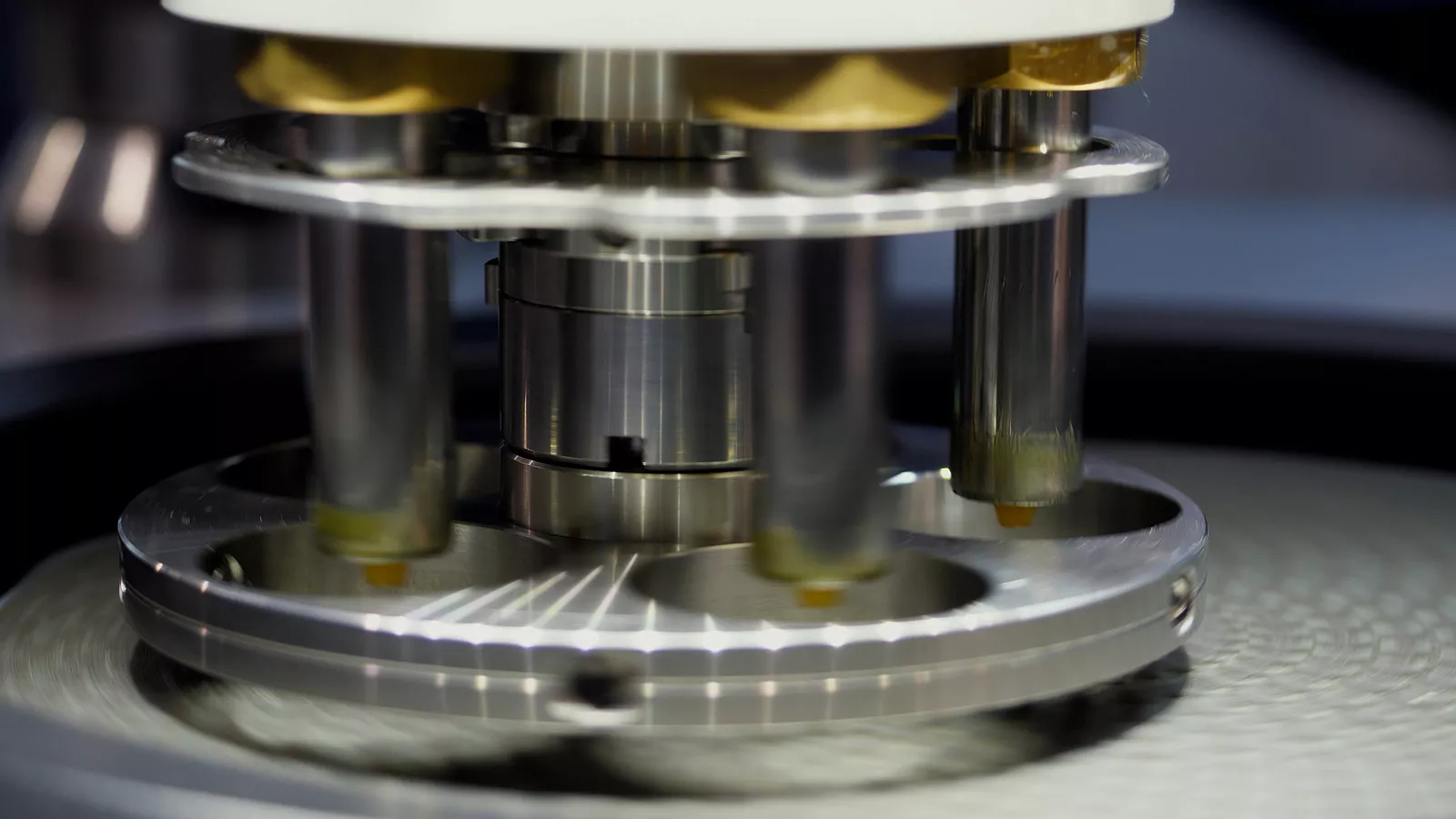
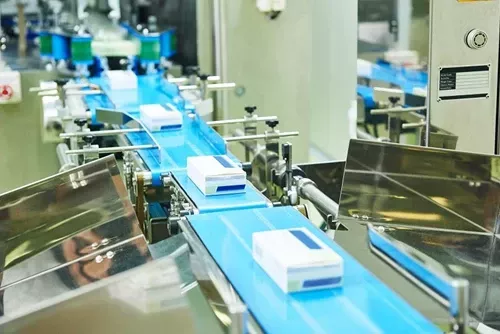
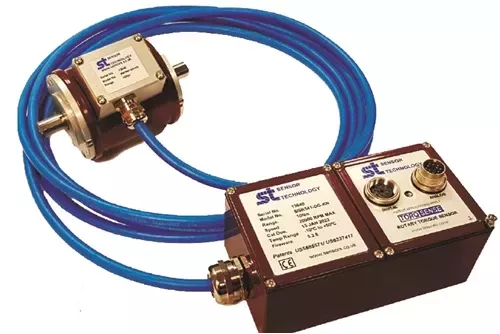
No physical contact ensures fast and efficient runs
Bottle capping is nearly always performed at very high speed, so that production targets are met. A major advantage of TorqSense is that it does not need to physically contact either the bottle caps or shaft of the torque head it is monitoring, instead using a radio frequency link. This means initial set-up and change over to new product runs is fast and efficient while operational reliability is not dependent on delicate slip rings.
Replacement for older Torque Sensors
Significantly, the new SGR530/540 sensors are designed to be drop-in replacements for the older RWT430/440 units they are replacing. They are the same size and shape as their corresponding older model, with the same mounting holes, cables in the same position. All that was necessary to set up a TorqSense transducer in the capping machine and turn it on.
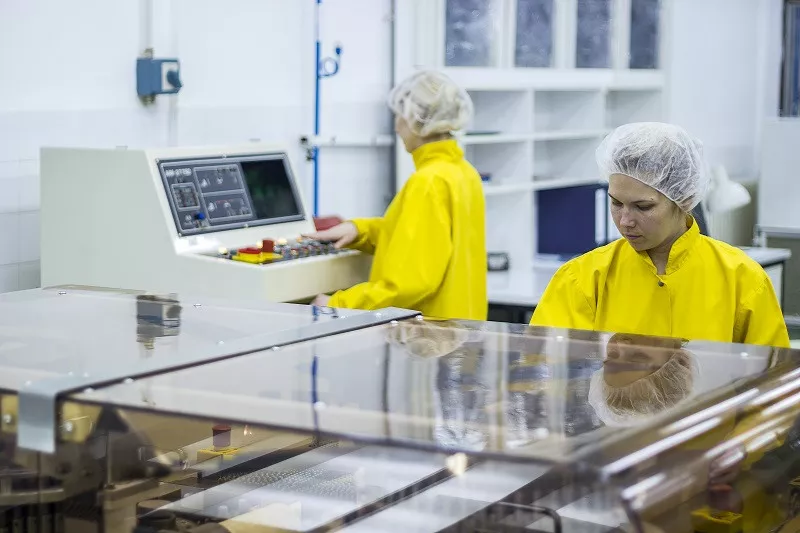
Fast and accutate torque measurement
The pharmaceutical company improved the quality of their products and significantly reduced waste and rework. It also increased production efficiency and obtained very valuable data on the overall production process. Fast and accurate torque measurement is becoming increasingly important as all manufacturing sectors automate their physical processes and at the same time need to improve the recording of production performance data. TorqSense is used in many industries, from automotive to materials processing, testing and measurement, FMCG (fast moving consumer goods) manufacturing and power generation.
Product
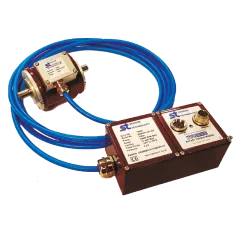
SGR530/540 Torque Sensor
- Measuring range: 1 to 13.000 Nm
- Large fully functional overrange capability of 250% (SGR 540)
- Minimal side & end load errors