Applications in plastics manufacturing
Linear position sensors or transducers are integral to injection molding and blow molding processes, where precise control over machine components is essential.
Injection molding: precision at high speed
Injection molding involves tracking the position of critical components such as the injection unit, mold, and nozzle. Linear position sensors provide real-time feedback to optimize the injection cycle, ensuring uniform product quality and reducing waste. Magnetoresistive sensors (rodless and spring-loaded types) are ideal for this high-temperature, high-vibration environment, offering non-contact operation and excellent durability.
Blow molding: accurate control for complex shapes
In blow molding, linear sensors help control mold positioning and air pin movement, ensuring plastic parts meet strict dimensional tolerances. These sensors allow for precision up to 0.005 millimeters, which is essential for blown film production. The rugged durability and long lifespan of these sensors ensure reliable operation in harsh conditions.
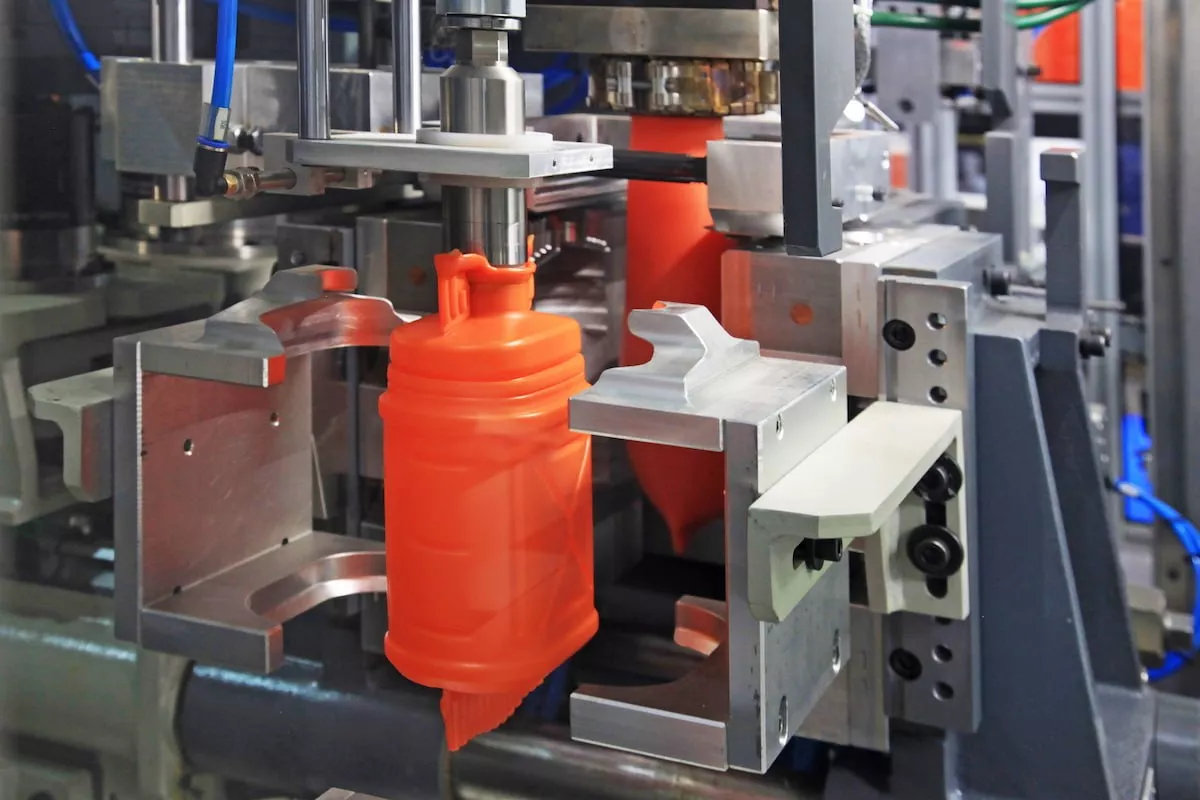
Types of linear position sensors
Various types of linear transducers offer unique benefits in plastic molding:
- Rodless sensors: compact and cost-effective, ideal for space-limited applications like material handling and packaging systems.
- LVDT sensors: non-contact, highly accurate, and resilient in extreme conditions, perfect for frictionless operation.
- Spring-loaded sensors: contact sensors suitable for continuous motion tracking in hydraulic systems.
- Fixed slide sensors: mounted in a fixed position, providing accurate feedback in high-speed assembly and automated production lines.
Conclusion
Linear position sensors ensure accurate positioning, improving product quality with tight tolerances. These non-contact sensors reduce wear and extend equipment life. They can withstand extreme environments like high temperatures and vibrations, making them perfect for plastic molding applications. Linear position sensors play a crucial role in modern plastic molding,
See how our linear position sensors can drive efficiency and reliability in your operations. Contact our team to explore customized solutions for boosting long-term success in for instance the plastics industry.