Zero margin for error in the braking system
The goal of the team was to not only break the current Hyperloop speed record of 467 kilometer per hour, but also to exceed half the speed of sound. As you can imagine this is a tremendous engineering challenge. Not only does the new pod needs to accelerate to top speed but also brake to standstill again, all within the limited distance of the test tube. This requires the team to constantly work on the edge of what is technologically possible. The pod has to be both fast and reliable, if it does not brake in time a solid steel door will be the harsh reality for the pod. Therefore, the braking system has to work 100% of the time, there is zero margin for error in this critical subsystem. The team has increased the reliability of the braking system by making it fully redundant, but also by closely monitoring the system. This is where Althen Sensors & Controls comes into play, by providing very small, lightweight but still accurate pressure sensors to be implemented in the braking system. The engineers at Althen reviewed the needs for a sensor and came with a suggestion of which they thought would work best. This turned out to be the EB100 Miniature Pressure Sensor.
Update after the competition
After an extended test week, the Delft Team made it to the finals (July 21st) of the 2019 SpaceX Hyperloop Pod Competition! The three others finalists were Swissloop, EPFLoop and TUM Hyperloop. Although the competition takes place in the United States, four European teams entered the finals: two Swiss, one German and the Dutch team. Unfortunately they didn’t achieve the final run they were hoping for. The emergency brakes were activated 91 meters in to the run due to a loss of communication. We are very proud of the overall achievement of the 2019 Delft Team, and are looking forward to our cooperation next year.
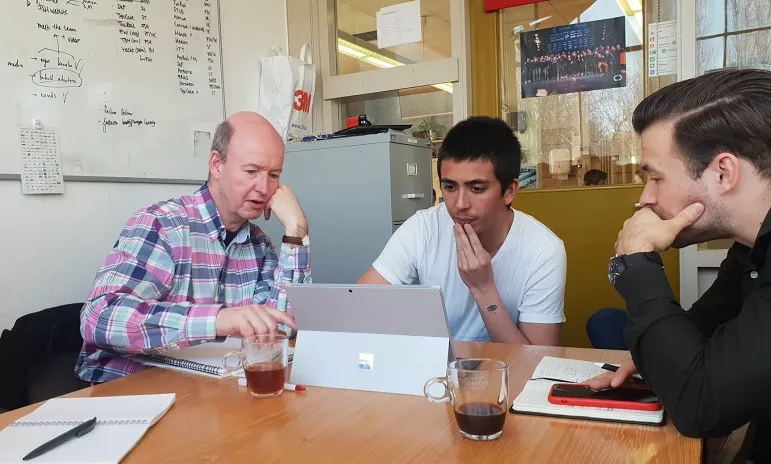
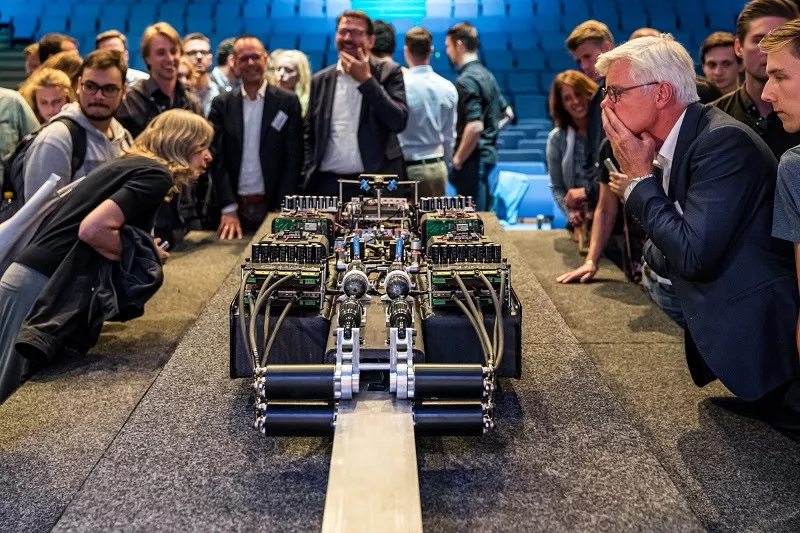
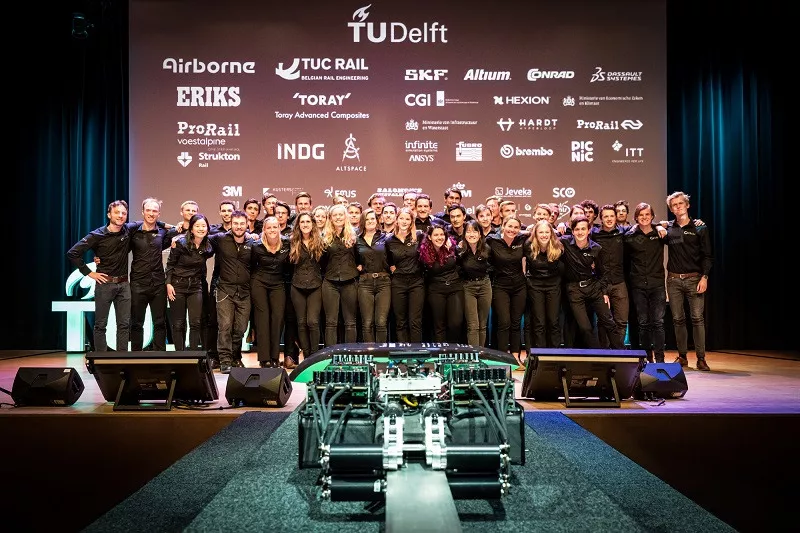
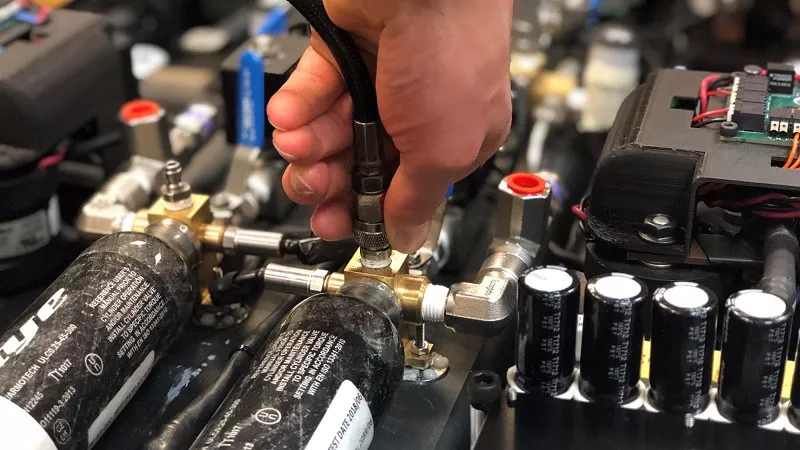
Miniature Pressure Sensor
The EB100 Miniature Pressure Transducer is a very small sensor which can still achieve a high accuracy. It was easy to incorporate these sensors into the pneumatic system design of the Hyperloop because they come with a metric M5 thread. This allowed the team to easily screw the sensor in a connection piece that was attached to the actuation system.
The sensors offered real time information about the pressure within the pneumatic actuation system both during the final run as well as during various leak tests. The high accuracy of the sensors allowed the students to detect even the smallest leak in the system, giving them the opportunity to remake a leaky connection. Ultimately improving the overall performance of the system.
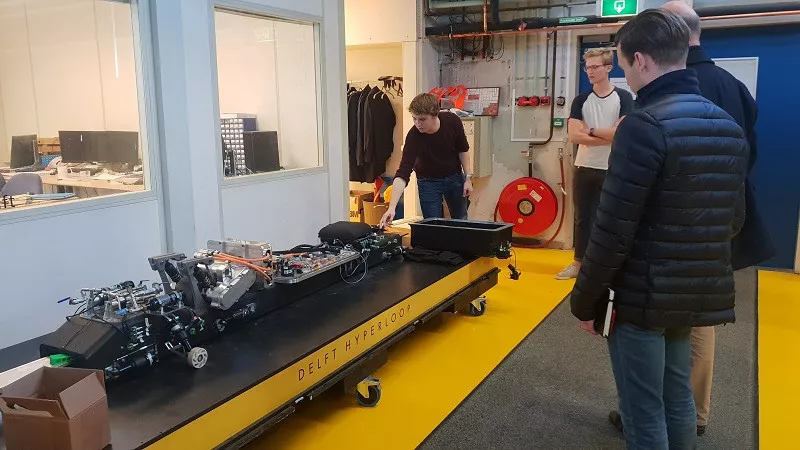
Constant pressure monitoring
The main reason to implement the Pressure sensors in the system is to use the sensor data during the final run to constantly monitor the pressure in the system. This way the navigational algorithm can calculate the braking distance at any moment during the run and adjust the point to brake accordingly. Therefore, allowing the team to know the pod’s braking distance at any time during the run. Consequently, they can keep on accelerating for as long as possible without accidentally hitting the steel door at the other end of the tube or coming to a premature stop. These kinds of small ingenious solutions allows the students to push the limit even further and get the most out of their pod.
In short, the EB100 Miniature Pressure sensors allowed the students to get the most out of their cutting-edge prototype. This was achieved by measuring the pressure in the braking system and constantly recalculating the braking distance using the data from the pressure sensors. This makes it possible to keep accelerating for as long as possible, which ultimately leads to reaching higher speeds.
Product used
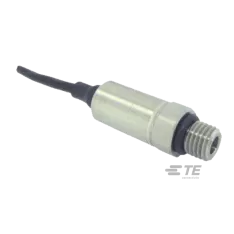
EB100 Miniature Pressure Transducer
- Pressure range: 20 to 350 bar
- Total error band of ±1 %
- Stainless steel connection