Accelerometers for railway wheelset bearings and brake systems
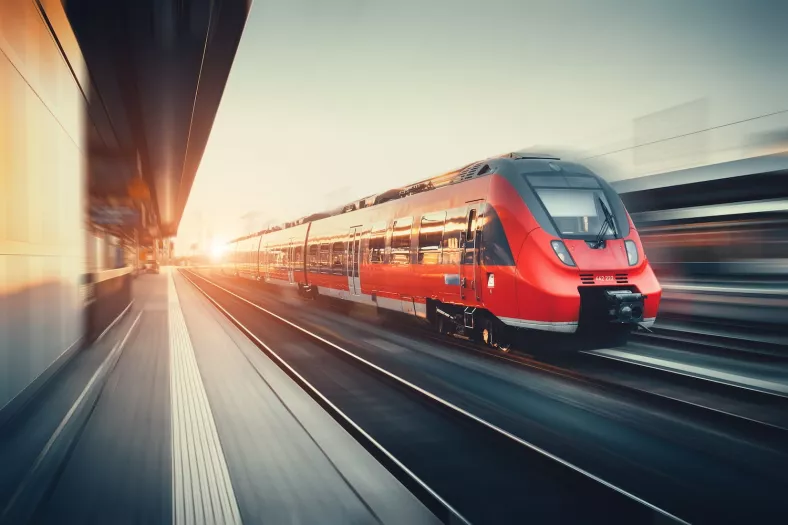
Precise measurements of vibrations, shocks, displacement, velocity, inclination and tilt
Acceleration sensors or accelerometers let you make precise measurements of vibration or shock for a variety of applications. Our accelerometers are based on several different technologies and include piezoelectric, strain gauges, MEMS, and capacitive sensors.All sensors are highly resistant against shock and vibration and are suitable for a wide range of purposes. They operate at frequencies of up to 25,000 Hz, with measurement ranges between ±0.25 g and ±70,000 g, and can be deployed in temperatures ranging from -40°C to +140°C.
We offer standard acceleration sensors but can also help you with a customized design or a complete measurement solution.
Accelerometers are devices designed to measure acceleration forces in three-dimensional space. They utilize various technologies, such as piezoelectric, piezoresistive, and capacitive, to convert mechanical acceleration into electrical signals. Althen Sensors & Controls specializes in delivering high-performance accelerometers that cater to the specific needs of industries like automotive, aerospace, industrial automation, and more.
Under acceleration, the seismic mass of the sensor causes a change in electrical charge in the piezo element, which can be read out as a charge Q that is proportional to the acceleration. Piezoelectric elements behave like a capacitor providing voltage at a set internal resistance. With an optional charge amplifier integrated in the sensor casing (IEPE interface), the output is converted into a voltage.
Direct current acceleration sensors are also called piezoresistive acceleration sensors. A piezoresistive accelerometer is based on changes in electrical resistance in a strain gauge (part of the sensor’s seismic system). To compensate for temperature fluctuations, these sensors require an additional internal or external temperature compensation for their output. Modern piezoresistive sensors accomplish this using special integrated circuits for all forms of on-board signal conditioning as well as on-site temperature compensation. You can either use these sensors with conventional glued-on strain gauges or opt for microelectromechanical systems (MEMS) technology instead.
Capacitive acceleration sensors are based on changes in the electrical capacity of the seismic mass under acceleration. This is a widespread technology commonly used applications such as airbags and mobile devices. Our capacitive acceleration sensors are manufactured using microelectromechanical systems (MEMS) technology. Our high-end silicon MEMS accelerometers in instrumentation quality are resistant against prestress and produce very little noise.
Just as there are many different applications for accelerometers, there are many different ways to build them: We offer acceleration sensors with piezoelectric, piezoresistive, strain gauge, MEMS, and capacitive measurement technology. In order to pick the right accelerometer, you should first analyze the conditions and parameters under which the sensor will be deployed. Our experts at Althen are happy to give extensive, independent advice – and help you find exactly the right accelerometer for your task.
Our acceleration sensors are available with integrated or external electronics. We can also integrate our sensors into your application for you. Althen is your competent partner for accelerometers for any of the following fields:
We offer a special range of Euro-NCAP certified, miniature accelerometers for the automotive industry. In addition to NCAP certification, part of the portfolio is also certified for the use in crash tests according to SAE J211/J2570, ISO 6487 and World SID. Our sensors offer single- and multi- axis measurements. You can choose from versions with integrated measurement amplifiers or full open Wheatstone bridges. The sensors can be mounted by glue joints or using fasteners.
In addition to sensors with directly mounted, shielded, low-noise cables, we also offer models with plug connectors. These are particularly suited for mechanically critical positions where the cables are under great stress (such as on test dummies) and frequently need to be replaced.
But you can not only replace the cables. Several sensors for multi-axis measurement can also be repaired should a measurement axis get damaged from excessive load. The casings are available in stainless steel, aluminum, or fully welded titanium versions.
In conclusion, Althen Sensors & Controls stands as a reliable partner in the realm of acceleration sensors, offering a diverse range of products with advanced features. As industries evolve, the company continues to innovate, ensuring their accelerometers meet the ever-changing demands of modern applications.
We offer standard acceleration sensors but can also help you with a customized design or a complete measurement solution.
Accept the marketing cookies to view this video.
Click here to change your consent.
Abnormal accelerations, vibrations or high temperatures give early signs of machine failure due component imbalance, misalignment, wear or improper use of equipment. Those can also easily be identified without manual measurements or wired equipment. Test our smart industrial IoT measurement solution for condition monitoring applications now! Wireless battery powered industrial sensor nodes and a gateway for communication to transmit data to the cloud is all you need to increase machine uptime and extend mean time between failures.