Measuring force on trawl nets
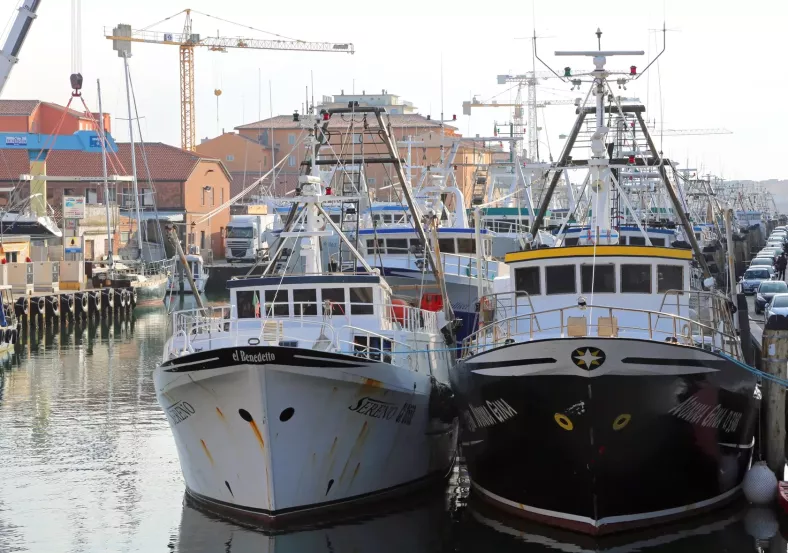
Modern and flexible: force sensors with strain gauges
Force sensors measure static and dynamic tensile and compressive forces -precisely and in virtually any condition. Our force sensors are based on the proven Strain Gauge measuring principle. Their operation relies on measuring strain in a precision metal structure using foil strain gauges bonded to the surface of the metal. From Miniature Force Sensors to Donut Ring Force Transducers, and Bending Beams to Load Cells - we offer a large selection of sensors for a wide variety of applications and industries. We are happy to assist you in the selection of a force sensor or load cell for your application.
Product categories
We offer standard force sensors, but can also help you with a customised design or a complete measurement solution
When you choose force sensors from Althen, you benefit from various advantages.
An external Amplifier allows you to adapt the Force Sensor or Load Cell to your requirements. The Amplifier converts the measuring signal of the strain gauges into an industry-standard voltage or current signal. In addition, you can use it to connect several sensors in parallel or to balance a static zero point.
Strain Gauge Amplifiers are available in three standard versions:
We offer you an extensive range of force sensors. The strain gauge structure can be installed in a variety of forms - depending on the force range and application requirements. An exemplary selection:
Force sensors are advanced devices that detect and measure the magnitude and direction of force applied to them. These sensors come in various types, including load cells, strain gauges, piezoelectric sensors, and more, each tailored to specific requirements. Force sensors can convert a force into an electrical signal. Their operation relies on measuring strain in a precision metal structure using foil strain gauges bonded to the surface of the metal. The structure can be built in a wide variety of forms depending on the force range and the application requirements. Our Load Cells range from 1 mN up to 10 Mega Newton.
We offer a wide range of force sensors. The strain gauge structure can be installed in a variety of shapes, depending on the force range and application requirements. There are, for example, annular or cylindrical force gauges, one-component and multi-component force sensors or special force transducers. Our sensors cover nominal forces from 10 N to 10 MN. The larger the nominal force, the larger load cells are needed. The nominal force refers to the maximum load of a sensor.Thanks to our own development and manufacturing department, there are almost no limits. Upon request, we also combine different measuring channels for you - for example with other physical parameters such as pressure or displacement measurement. We integrate limit contacts and alarm devices for you or build our sensors into housings and control cabinets.
We have the perfect force sensor for every application. We are happy to support you in your product selection. At Althen, we draw on more than 45 years of experience to offer you the optimum solution, customised to your requirements. This also includes customised force transducers as a complete package. The advantage for you is that we are not tied to one manufacturer and can advise you independently. On request, we can customise the measuring system exactly to your needs. Do you have any questions? We are glad to help you!
Force sensors consist of a spring body made of metal, for example a steel cylinder. When a force acts on this spring body, its surface deforms elastically. Its task is to convert the forces to be measured into strains as often as possible in a repeatable manner. The actual sensor element is the strain gauges, which are attached to the spring body. The strain gauges record the mechanical deformation and convert it into an electrical output signal. As a rule, four strain gauges are installed - two expand when a force is applied, the other two are compressed. The four strain gauges are connected via a Wheatstone bridge circuit, which is supplied with an electrical voltage. If the resistances of the strain gauges differ, the output signal changes. This allows the applied force to be determined precisely.
The strain gauge measuring principle impresses with various properties:
When selecting a force sensor for a technical application, a number of criteria must be taken into account to ensure that the requirements of the application are met and that the most accurate and reliable measurement results are achieved. To do this, it is first important to understand the application in order to determine, for example, the required accuracy or the number of interfaces for the force sensor.
The following criteria, among others, must be determined during the selection process: