Strain gauge basics: key technical terms
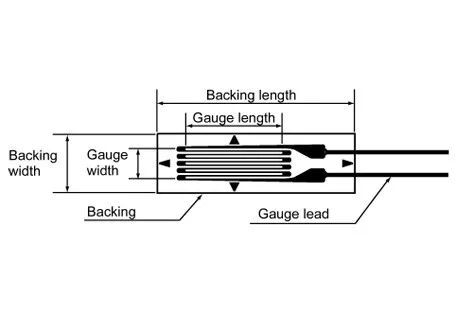
Grid length: The active measuring range
The grid length of a strain gauge represents the strain-sensitive part of the measurement grid. This is the active measurement grid, where strain is actually measured.
- The active measurement area is located between the inverted loops of the measurement grid.
- The choice of grid length depends on the application and the type of material being tested.
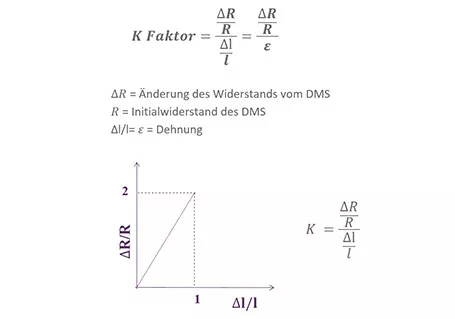
Stretch sensitivity factor (K-factor)
The K-factor, or strain sensitivity factor, measures a strain gauge's responsiveness to strain. It represents the relationship between the relative change in resistance and the applied strain.
- Formula: K-factor = relative change in resistance / relative strain.
- Typical value: Strain gauges typically have a nominal K-factor of around 2, meaning a 2% change in resistance corresponds to a 1% elongation.
The K-factor is a key parameter in selecting the appropriate strain gauge for applications requiring precise load measurements or structural monitoring.
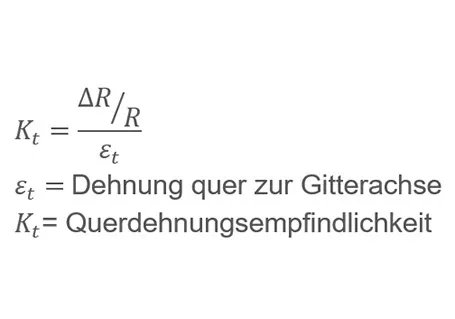
Sensitivity to transverse distortion
Strain gauges not only measure strain along the longitudinal direction of the measurement grid but can also be sensitive to transverse deformation.
- Definition: Transverse deformation sensitivity refers to the strain experienced when the strain gauge is subjected to a load perpendicular to the longitudinal axis of the measurement grid.
- Importance: This sensitivity to transverse deformation can influence the accuracy of measurements under complex loading conditions.
The extent of this sensitivity is quantified by an equation that calculates the effect of transverse deformation when a uniaxial load is applied perpendicular to the measurement grid's axis.
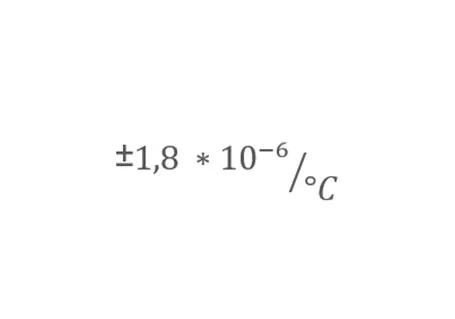
Temperature self-compensation for strain gauges
Temperature variations are a critical factor when using strain gauges. Self-compensating strain gauges are specifically engineered to reduce the impact of thermal expansion, ensuring accurate measurements across diverse conditions. In this section, we explore key considerations and practical applications.
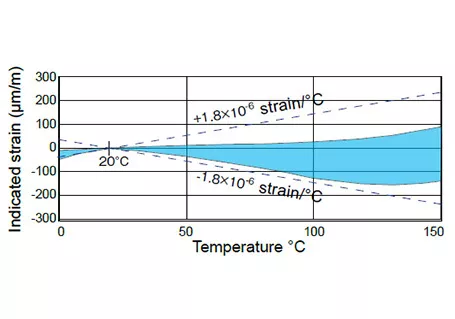
What is temperature self-compensation?
During manufacturing, strain gauges are calibrated to match the thermal expansion coefficient of specific materials, such as steel, which has a coefficient of 11 ppm/°C.
- Effect: While both the strain gauge and the specimen experience thermal expansion, resulting in a small voltage, this minimal signal is compensated for.
- Self-compensating: Strain gauges designed to account for these thermal effects are known as "self-compensating."
For enhanced accuracy, temperature corrections can be applied using a polynomial provided by the manufacturer, further minimizing temperature-related errors. Self-compensating strain gauges are ideal for applications where temperature fluctuations may otherwise lead to measurement inaccuracies.
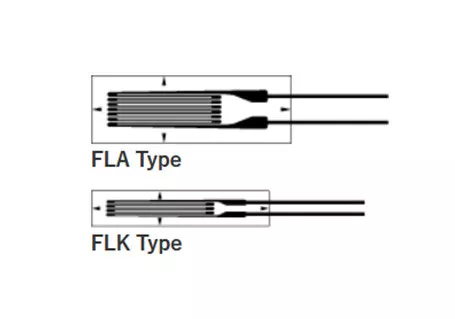
Mesh width of strain gauges
Narrow strain gauges are designed for specimens with limited surface areas, such as tubes and round bars.
- Features: Strain gauges like the FLK series offer the same gauge length but with a reduced width, making them ideal for small or irregular surfaces.
- Applications: These gauges are perfect for measuring small-diameter components or thin structures.
- Example: The TML F-series is a widely used choice for these types of applications.
Operating temperature range of strain gauges
The operating temperature range defines the temperature limits within which a strain gauge can operate reliably over time.
- What does this mean? Within this range, the strain gauge’s performance remains stable, even under prolonged exposure to temperature fluctuations.
- Applications: Strain gauges are used in various environments, from cryogenic systems to high-temperature settings. Selecting a strain gauge that suits the specific temperature conditions of your project is crucial for ensuring accurate and dependable measurements.
Strain limit of strain gauges
The strain limit, or yield strength, is the maximum strain a strain gauge can endure under ideal conditions without experiencing damage or degradation in performance.
- Why is this important? Exceeding the strain limit can lead to permanent deformation or loss of functionality in the strain gauge.
- Practical example: When testing high-strain materials, it is essential to choose a strain gauge with a yield strength greater than the expected maximum strain to ensure reliable results.
Fatigue limit and service life
The fatigue limit refers to the number of cycles a strain gauge can endure under repeated stress before a change of 100 µm/m is observed from the original calibration. This measure helps assess the strain gauge’s longevity in dynamic testing conditions.
Nominal resistance of strain gauges
The nominal resistance refers to the electrical resistance of a strain gauge at room temperature and without any applied load.
- Typical values: Common nominal resistances for strain gauges are 120 ohms and 350 ohms.
- Why it matters: The nominal resistance influences both the sensitivity and power consumption of the measuring circuit. Strain gauges with higher resistance are often preferred in applications where minimizing energy loss is crucial.
Nominal resistance of strain gauges
Strain gauges are available in many shapes. Which shape you choose depends on your measurement task.
Selecting the right gauge length for strain gauges
Choosing the correct gauge length for strain gauges is critical to obtaining accurate measurements. The appropriate selection depends on the material and structure of the object being measured. Below, we outline guidelines for both homogeneous and inhomogeneous materials.
Selection based on the measurement object
The size and properties of the object dictate whether a short or long strain gauge should be used. The goal is to maximize measurement accuracy by considering the material's stress and strain gradients.
Homogeneous materials (e.g., metals)
For materials with a consistent structure, such as steel or aluminum, the following considerations apply:
No strain or stress gradient: Either short or long strain gauges can be used, depending on the measurement area size.
With strain or stress gradient: A short strain gauge is recommended. This helps minimize the averaging effects beneath the grid surface, which is particularly important for high gradients.
Important note: If a voltage gradient exists beneath the grid, running from positive to negative, the output signal may be neutralized by averaging, potentially leading to no measurable result.
Inhomogeneous materials (GRP, CFRP, Concrete)
Inhomogeneous materials, such as concrete, GRP, and CFRP, require a strain gauge with a sufficiently long grid length to account for variations below the surface. For materials like concrete, which consists of cement and aggregates, a strain gauge with a grid length approximately three times the size of the aggregate grains should be used to ensure accurate measurements.
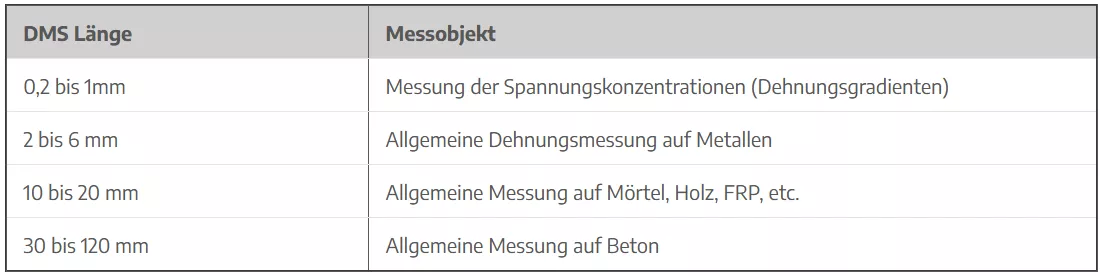
Response behavior of strain gauges / frequency response of strain gauges
The response behavior of a strain gauge is influenced by both the grid length of the gauge and the longitudinal wave propagation in the material being measured.

More information
Do you have questions about strain gauges?
Need more information about strain gauges or perhaps additional questions or a quotation? Contact our technical experts, who will be happy to help you further.