De viktigaste delarna av A350 XWB, som flygplanskroppen, vingarna, motorerna och stjärtenheten, tillverkas i Airbus europeiska produktionsanläggningar i Frankrike, Tyskland, Spanien och Storbritannien. I A350 XWB:s slutmonteringslinje (FAL) i Toulouse sätts sedan alla flygplansdelar ihop som ett högteknologiskt pussel.
Flygplanskroppen på A350 XWB består av tre huvuddelar - den främre och den mittersta sektionen samt en bakre sektion. Alla sektioner - inklusive landningsstället - monteras vid den första huvudmonteringsstationen, P50. När detta steg är klart transporteras flygplanskroppen till monteringsstationen P40, där ving- och stjärtsektionerna sammanfogas. Slutmonteringslinjen är extremt flexibel. Den kan användas för både A350-900 och -1000-modellerna.
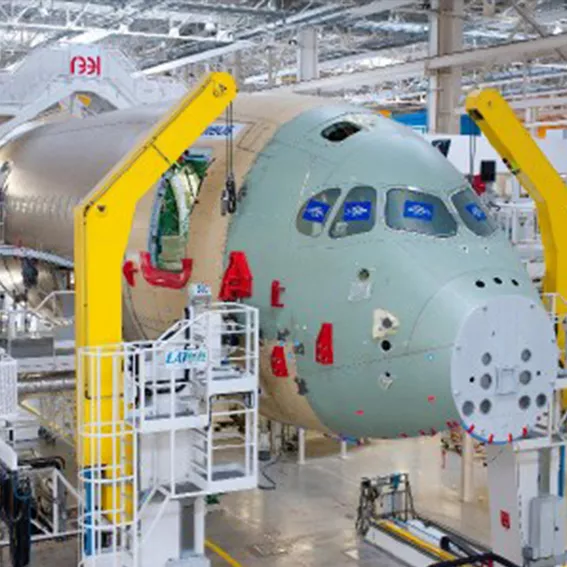
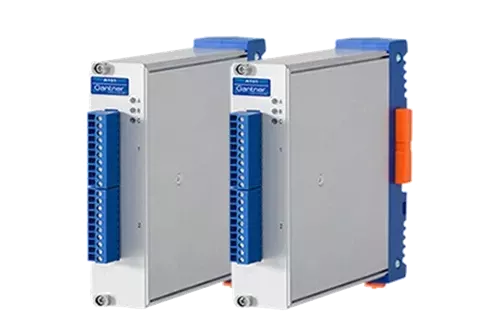
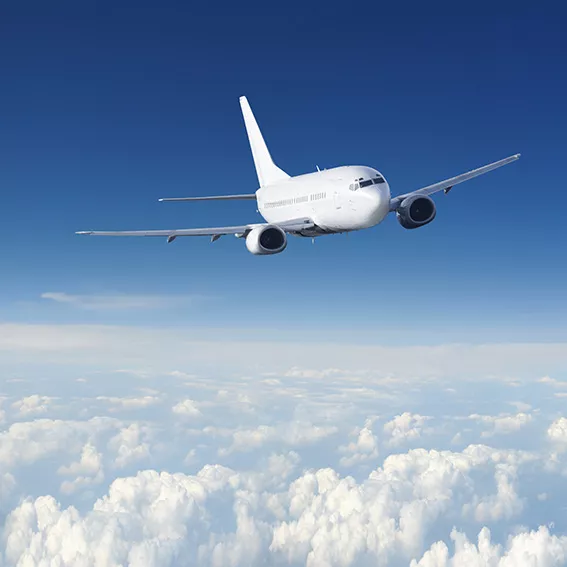
Processen för sammanfogning
Processen med att sammanfoga och ansluta de stora enheterna är en komplex uppgift. Speciellt när det gäller komponenter tillverkade av kolfiberförstärkt plast (CFRP), som används i stora mängder i A350 XWB, leder tyngdkraften och miljöförhållandena till geometriska deformationer. För att säkerställa tillförlitlig lokalisering och positionering av de stora flygplansdelarna stöds monteringssystemet av mätteknik. En serie fleraxliga positioneringssystem lyfter, flyttar och riktar in flygplanskroppen och vingstrukturen för att säkerställa optimal passformsnoggrannhet. Lastceller som är monterade i positionerarens drivmekanism används för att ge bästa möjliga skydd för de stora delarna under uppriktningen. De används för att övervaka de krafter som verkar på strukturen under rörelsen. Eventuella skador som orsakas av spänningar och påfrestningar på delarna under monteringen undviks på så sätt.
Hela monteringssystemet innehåller 300 lastceller. Enkelaxliga lastceller övervakar slaglängden (Fz) och trippelaxliga lastceller övervakar kraften under monteringen (Fx, Fy och Fz). Alla lastceller har en dubbel bryggutgång för att möjliggöra redundans i systemet. Lastcellerna är anslutna till ett Gantner Q.bloxx-mätsystem. Totalt 150 Q.bloxx A101-moduler används för primär kraftövervakning. Dessutom används 300 Q.bloxx A102-moduler för redundant övervakning.
Hur mätsystemet fungerar
Avståndet mellan lastcellen och övervakningssystemet kan vara upp till 75 meter. Att placera signalomvandlarna nära de faktiska mätpunkterna är ett av de viktigaste kraven när man utformar ett mätbaserat monteringssystem. Den optimala kanalfördelningen i Q.bloxx, i kombination med möjligheten att fritt kombinera och distribuera moduler, ger Airbus maximal flexibilitet. Modulerna kommunicerar via RS-485 med en centralt placerad Q.station-styrenhet, som tar hand om datainsamling, synkronisering och styrning. Data överförs via ett högeffektivt protokoll med en baudhastighet på upp till 48 MBaud. Trots den decentraliserade strukturen är mätningen synkroniserad med ett jitter på mindre än 1 µs. Denna arkitektur ger tillförlitliga mätresultat med minimal kabeldragning.
Övervakningssystemet för monteringslinjen omfattar en Schneider Electric Safety PLC. Q.station-styrenheten med öppen arkitektur kommunicerar med Safety PLC via TCP/IP-läge. Genom att separera Q.station-styrenheten från mätmodulerna optimeras kommunikationen och kompatibiliteten med övervakningssystemet avsevärt. En annan fördel för Airbus är möjligheten att byta ut styrenheten om gränssnittet eller prestandakraven ändras - utan stora nyinvesteringar.
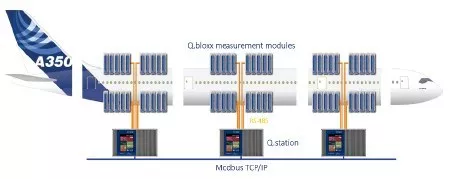
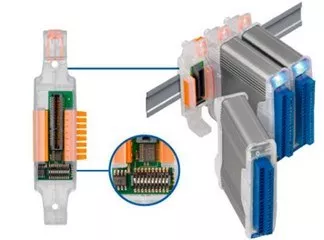
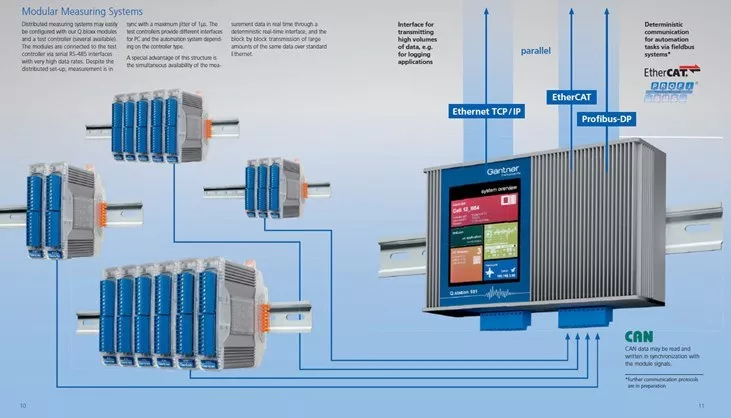
Mätlösningens funktion och struktur
Q.bloxx A101 och A102 har inbyggda mikroprocessorer, 24-bitars A/D-omvandlare, hårdvarufilter för antialias och fullständig 3-vägsisolering upp till 500 VDC på varje kanal. Mätmodulerna stöder samplingsfrekvenser på upp till 100 kHz per kanal.
Eftersom överföringen av stora mängder rådata innebär en hög belastning på nätverksresurserna är varje modul utrustad med en FPGA. Detta möjliggör fullständig signalkonditionering och databehandling direkt vid den punkt där sensordata kommer in i mätsystemet. Det innebär att endast data med processrelevant information, t.ex. medelvärde, min/max och peak spike-mätning, skickas till övervakningssystemet. På så sätt undviks långa laddningstider och svarstiderna förbättras.
Q.bloxx för decentraliserad, snabb och exakt mätning
Kostnaden för att montera passagerarutrymmet kan utgöra upp till 40% av den totala byggbudgeten. Därför är det särskilt viktigt att monteringssystemet är tillförlitligt och tillgängligt. Varje Q.bloxx-modul är ansluten till ett uttag som innehåller ett inbyggt flashminneschip med en kopia av hela modulkonfigurationen. Detta innebär att det inte är nödvändigt att manuellt konfigurera om den nya modulen eller övervakningssystemet om en defekt modul byts ut. Modulerna kan bytas ut under drift utan att strömförsörjningen behöver stängas av. Konfigurationen kopieras från basen till den nya modulen på bara 5 sekunder. Mätningen fortsätter automatiskt så snart konfigurationen har återställts. Q.bloxx ”Hot Swap”-funktion möjliggör effektivt underhåll och service av mätsystemet, minimerar stilleståndstiden och ökar effektiviteten i den slutliga monteringslinjen.
Grafik 1: @AIRBUS S.A.S. 2012 foto av e*m company / P. Pigeyre
övriga foton/grafik: GI